by Bradley van Paridon | Dec 11, 2023
From cellphones to solar panels, electronics are getting thinner and more flexible. While the advantages are numerous, manufacturing flexible devices comes with several drawbacks. Hpmc Uses In Detergent
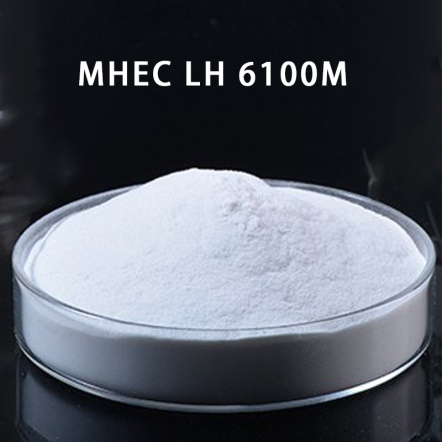
Thin electronics are made from plastics, leading to a stark sustainability problem, and manufacturing often requires potentially toxic chemicals, like hexane and toluene. To “green” the flexible electronics industry, a team of researchers in Italy are turning to a familiar, plant-based material to inspire a new crop of functional materials with applications in wearables, biomedical sensors, and edible electronics.
According to Luca Maiolo, a researcher at the National Research Council Institute for Microelectronics and Microsystems in Italy, and his colleagues Elena Palmieri and Francesco Maita, cellulose, the main component of plant cell walls, may have the right blend of properties to act as an alternative to conventional plastics.
In a paper published in Advanced Materials Technologies, the team describes a new method to use derivatives of cellulose to make suitable substrates for future sustainable, flexible electronics.
The basis for flexible electronics hinges on finding a thin yet durable material onto which the specific electrical components are placed. Plastics have long been an obvious choice because of their durability, flexibility, and the fact that plastics are already made around the world.
Displacing plastic as the top choice with a sustainable alternative is hard because potential bio-based materials are less durable and not as amenable to current manufacturing techniques.
“Our choice of materials for experimentation centered on cellulose derivatives,” said Palmieri. “This decision was influenced by our prior experience with these polymers, albeit in different applications, such as cultural heritage preservation.”
Cellulose is made of long chains of sugars and is a structural compound in plants. Derivatives of cellulose are molecules that result from processing, resulting in cellulose with different chemical groups, such as methyl cellulose or cellulose acetate. These derivatives are already used in many products, and Maiolo and his team hypothesized that two derivatives, ethyl cellulose and hydroxypropyl cellulose, could serve as suitable substrates that could be manufactured without harmful chemicals.
For these derivatives to work, they needed to be flattened to nanoscale thickness and not fall apart. As Maiolo explained, “To make these biodegradable substrates compatible with thin film technology requires the use of materials in the range of a few tens of nanometres in thickness with a mean roughness of below 50nm and which are very uniform.”
The team chose ethyl cellulose and hydroxypropyl cellulose because each has existing properties that would make them useful in electronics.
Ethyl cellulose, for example, is extremely hydrophobic, which means it does not mix with water, making it potentially resistant to damage during the chemical manufacturing process and for outdoor use, such as in precision agriculture. Hydroxypropyl cellulose, on the other hand, is hydrophilic — mixes well with water — and amenable to certain printing techniques and the production of thin films.
From these two derivatives, the team produced three new substrates. Palmieri explained the two main challenges they faced: “The first obstacle revolved around developing suitable formulations for substrate production and refining the substrate preparation steps.”
After many tests, the team found it was possible to achieve different mechanical and chemical properties of the thin substrates by changing the compositions of the derivatives. The hydroxypropyl substrate had better flexibility but was less chemically stable while the ethyl cellulose substrate was chemically stable but more brittle.
However, a blend of the two, “may represent a good compromise in terms of mechanical properties and chemical stability, being able to withstand fabrication process while enduring thousands of bending cycles,” said Maita. Importantly, the team was able to make these substrates using a one-step process that didn’t waste materials, adding to the efficiency and eco-friendliness of the technique.
“The second challenge involved the adaptation of the standard photolithographic process to the material,” said Maita. Photolithography is a process in electronic manufacturing that uses light, often UV light, to build the detailed patterns of circuits onto a chip or board.
If the cellulose-based substrates could survive this process, it makes them a more viable alternative as manufactures wouldn’t need new machinery or workers to produce a sustainable product.
The team successfully used UV photolithography to deposit metal contacts onto the substrates and build two types of working sensors, one which could measure strain placed on an object, and a capacitive humidity sensor to gauge relative humidity, proving the feasibility of the method and the new materials.
Having achieved the first proof that cellulose derivatives can replace plastics in flexible electronics, “the natural next step is to use these materials with standard microfabrication facility, removing all the toxic and unsafe chemical compounds from the process,” said Maiolo.
Guaranteeing, as he said, “a complete integration of these materials with conventional manufacturing companies [which could] generate the idea of a new sustainable electronic industry, mitigating its impact on Earth.”
Reference: Elena Palmieri, et al. Towards sustainable electronics: exploiting the potential of a biodegradable cellulose blend for photolithographic processes and eco-friendly devices, Advanced Materials Technologies (2023) DOI: 10.1002/admt.202301282
Feature image credit: Elena Palmieri and Francesco Maita
Sign up for our weekly newsletter and receive the latest science news directly to your inbox.
Sign up for our weekly newsletter and receive the latest science news.
This ocean-safe putty was designed to help seed new coral reefs, offering a much-needed replacement for hardware store products.
New technique uses waste metal shavings to catalyze hydrogen production, turning nothing but trash and water into clean, renewable fuel.
Scientists are using carbon filaments from mushrooms in supercapacitors, paving the way for a sustainable energy future.
A material derived from avocado pruning waste and bio-polyethylene combines high strength with biodegradability.
Researchers are tackling the growing problem of electronic waste by designing wearable electronics from sustainable and recyclable materials.
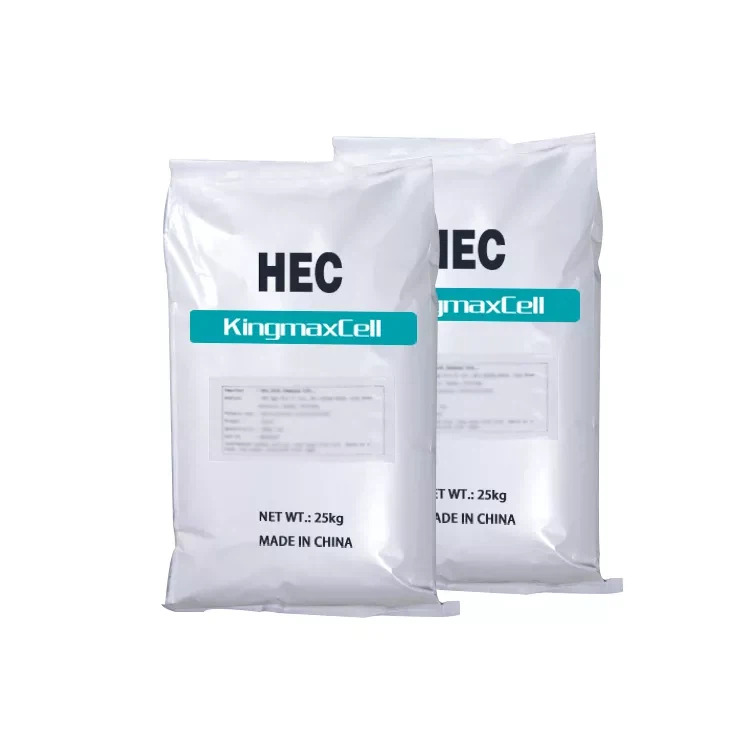
Cellulose Methyl E-CASE liquid metal adhesive enables flexible connections to make better, tougher flexible electronics for wearables and robotics.