TIG welding, or tungsten inert gas welding, is a process that uses a tungsten electrode to produce the weld and inert gas to protect the weld area from atmospheric contamination.
Welding is a process that joins two or more pieces of metal or thermoplastics using heat, pressure, or both, creating a continuous, strong joint.There are several welding methods, but in this article we will focus on one specific type: TIG welding. Welding Electrode E6013 Machine

TIG welding, or tungsten inert gas welding, is a process that uses a tungsten electrode to produce the weld and inert gas to protect the weld area from atmospheric contamination.It is a highly controllable and precise method, highly valued for its ability to produce high quality, highly clean welds, often used in the aerospace industry, automotive manufacturing and in applications requiring precision joints.
One of the essential elements in this process is the TIG welder, a device specifically designed to carry out this type of welding.This equipment, the TIG welder, has a series of features and functions that allow the precision and control that define this welding method.
TIG welding is an electric arc welding process, meaning that an electric arc is created between an electrode and the base material to melt the metal and form the joint.In this case, the electrode is made of tungsten, a metal that is very resistant to heat.
The "TIG welder" emits an electric arc that melts the base metal, and at the same time an inert gas, usually argon or helium, is used to protect the welding area from any air contamination.This process can be carried out with or without filler metal, depending on the thickness of the base material and the type of joint required.
TIG welding has several advantages.Firstly, it is capable of producing high-quality and very clean welds, thanks to the protection provided by the inert gas.Additionally, the TIG welder offers precise control over heat and welding speed, allowing you to create fine, precise joints.
However, TIG welding also has some disadvantages.Firstly, it is a relatively slow process compared to other welding methods, which may not be ideal for large scale productions.Additionally, it requires a high level of skill and experience to be performed correctly.TIG welding is also more expensive than other methods due to the cost of the inert gas and specialized equipment required.
Thanks to its precision and the quality of the welds it produces, TIG welding is used in a variety of industries and applications.It is common in the aerospace industry, where exceptional precision and strong joints are required for aircraft components.
It is also used in automotive manufacturing, especially high-end and racing cars, where precise, high-quality welds are essential.Other applications include bicycle manufacturing, shipbuilding, and electronic component manufacturing.
Learning TIG welding takes time, patience and practice.Specific training is typically needed to learn how to properly operate a TIG welder and to understand the many factors that can affect weld quality, such as gas selection, equipment setup, heat control, and technique. welding.
There are many technical schools and training programs that offer TIG welding courses.These programs often combine classroom instruction with workshop practice, allowing students to learn theory and then apply it in a practical setting.
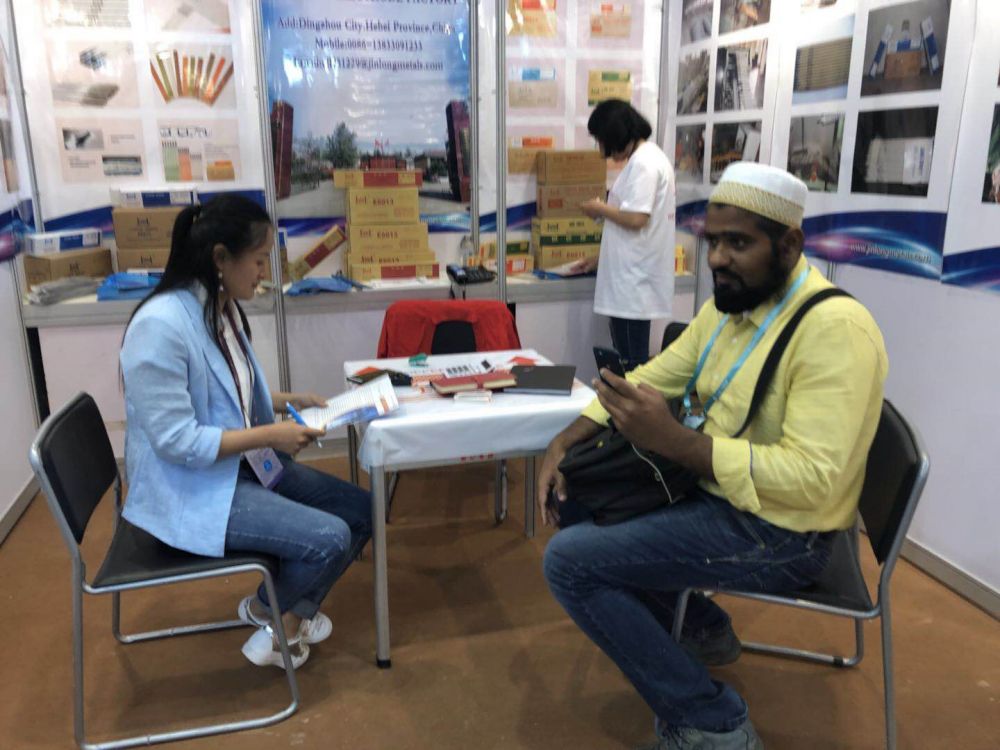
Stainless Electrode In conclusion, TIG welding is a highly specialized welding method that offers exceptional precision and quality.Although it requires a significant investment of time and money to learn and equip properly, its ability to produce high-quality joints and its application in a variety of industries make it invaluable to those willing to master this craft.