3D printing news News From Prototyping to Full-Scale Production: The Role of Ceramic Additive Manufacturing in Industrial Applications
Among the different 3D printing materials, technical ceramics generate the most curiosity and interest. This can be seen by the fact that the market for ceramic 3D printing is growing year by year as it finds its place in different industries. For example, according to a recent report by Fundamental Business Insights, in 2023, the global 3D printing ceramic market was valued at about $45.12 million and is expected to reach $519.72 million by 2032, with a compound annual growth rate (CAGR) of 31.2% between 2024 and 2032. Zirconia Ceramic Turbine

This growth can be explained by this increased interest in technical ceramics and their advanced properties, including chemical resistance, electrical insulation, high temperature resistance and biocompatibility. These characteristics make them ideal for demanding industries such as aerospace, automotive, energy and medical.
Ceramic additive manufacturing is an increasingly present technology for industrial applications.
While technical ceramics are ideal for high-performance applications, it is also true that it is not always easy to process these materials. The challenge when dealing with ceramic materials in part production is to maintain material properties and quality for each part. When increasing production or dealing with complex geometries, problems such as porosity, surface roughness and dimensional accuracy may arise.
To meet this challenge today, several companies have decided to specialize in ceramic 3D printing and demonstrate the feasibility of additive manufacturing in ceramics for complex, serial applications. Among these companies is Bosch Advanced Ceramics, which was established in 2014 as part of the Bosch Business Innovations subsidiary within the renowned Bosch Group and has since specialized in industrial production with ceramic additive manufacturing. The goal of Bosch Advanced Ceramics is to bridge the gap between prototyping and high-volume industrial production of ceramic components.
The advantages of using additive manufacturing over traditional manufacturing methods are well known. These include the ability to produce highly detailed and complex parts, a more flexible and optimized process, the possibility to integrate multiple functionalities into a single component for more innovative product designs, faster time to market and savings in terms of money and time. But that is not all.
If we look more closely at ceramic additive manufacturing, it is also important to note AM also makes it possible to avoid the use of expensive molds, especially for small and complex parts. This further helps to eliminate long waiting times and high costs for their manufacture and delivery. Another key point is that ceramic AM provides access to flexible manufacturing, easily adaptable to changing design and production requirements.
Banking on these many advantages, more and more companies today are benefiting from the production of ceramic components at scale through additive manufacturing. This clearly demonstrates that the technology is no longer confined, as is sometimes mistakenly believed, to the world of prototyping.
On this point, Ashu Sharma, CSO Bosch Advanced Ceramics, believes that it is important to communicate these benefits as not everyone is yet aware of them, adding, “As additive manufacturing is a relatively young technology, many of our customers are not aware of all its benefits. We inspire our customers in technical meetings, showing them how to leverage these benefits and get the best use out of the technology.” The challenge to date is therefore to try to make the potential of ceramic AM and the breadth of possible applications known to most people.
But how do these benefits translate into advanced parts? We asked Bosch Advanced Ceramics to show us concrete examples of implemented use cases. Interestingly, this technology and these materials are indeed adaptable to a wide variety of applications and different industries.
Bosch Advanced Ceramics serves sectors that each present unique challenges and require customized solutions. Notably this includes the medical, semiconductor, energy, automotive and electronics industries. Among the company’s most recent projects is the production of a very small and intricate insulation sleeves for a medical technology company. The sleeve was designed to electrically insulate a 0.5-mm wire in a laparoscopic instrument. The challenge was to produce a component with a maximum external diameter of 1.3 mm and a wall thickness of only 90 µm. Requirements almost impossible to achieve with traditional manufacturing methods
AM technology enabled Bosch Advanced Ceramics to meet this challenge by making rapid changes to design and process parameters, enabling them to refine their manufacturing approach. Using Lithoz’s Lithography-based Ceramic Manufacturing (LCM), the company was able to produce up to 1,400 parts in a single printing process and as many as 50,000 parts in a year. The success of the project also enabled the implementation of innovative and less invasive laparoscopic instrumentation for patients.
The 3.65mm-sleeve was manufactured from alumina for excellent thermal resistance, chemical stability and electrical insulation.
Another interesting application of ceramic 3D printing is the one made for leading automated machinery company STIWA. Here, an innovative dispensing needle was needed.
Typically, metal dispensing needles are used in automated adhesive processes to accurately dispense highly-viscous adhesives. These components must be particularly robust and wear-resistant, as downtime in production can result in significant costs. Bosch Advanced Ceramics has developed for STIWA an alternative dispensing needle made of technical ceramics, produced by 3D printing.
The dosing needle was printed on a Lithoz printer with Alumina 99.8%. What is special about this dispensing needle is its complex internal geometry: an internal cone that tapers from a few millimeters down to 0.8 mm, characterized by sophisticated curvature. A geometry that is impossible to achieve with traditional manufacturing techniques. In addition, the high precision of the manufacturing process ensured extremely low surface roughness, promoting a smooth flow of adhesive through the hole.
The ceramic dispensing needle has a complex internal geometry.
Finally, another area that can benefit from ceramic 3D printing because of the incredible properties of this material is undoubtedly semiconductors. One successful use case, Bosch Advanced Ceramics tells us, was the fabrication of a 200 mm large ring blade for the handling and processing of wafers from cassettes or process chambers. What is interesting is that this piece, made of >99.8% alumina, measures an impressive 250x200x3.5 mm and weighs only 280 grams. A 120-mm continuous inner channel was made inside the piece to allow for the flow of gas or liquid.
In addition, unlike metals, alumina does not contaminate wafers or compromise purity in semiconductor manufacturing, significantly reducing contamination risks. Its nonreactive nature, combined with excellent chemical and temperature resistance, makes it ideal for the semiconductor environment, ensuring consistent and reliable performance. For this application, Bosch Advanced Ceramics used a printer from 3D Ceram, which enabled the production of the sizable ring with excellent density and precision in one piece.
Ceramic additive manufacturing allows scalability and flexibility in both part design and production.
These use cases highlight the transformative potential of ceramic additive manufacturing for a broad range of industrial needs. By delivering reliable, high-quality solutions for even the most demanding applications, this technology is proving to be a game-changer. Partnering with experts who can support a project from concept to full-scale production—such as Bosch Advanced Ceramics—provides a significant competitive advantage in today’s industry.
“By mastering the entire process chain from design iteration to final component, we’ve grown the technology beyond the prototype stage and are now actively producing ceramic components in series using 3D printing, demonstrating the viability and reliability of additive manufacturing for a range of industries. The ability to produce high precision technical ceramics with complex geometries offers real benefits, from reduced lead times to more efficient use of materials. As technology continues to develop, it’s clear that additive manufacturing will be a key driver of innovation, helping industries to remain competitive in a rapidly changing landscape,” added Sophie Berninger, CEO of Bosch Advanced Ceramics. To learn more about Bosch Advanced Ceramics and Ceramic AM applications, click HERE.
What do you think about the role of ceramic additive manufacturing in industrial applications? Let us know in a comment below or on our LinkedIn, Facebook, and Twitter pages! Don’t forget to sign up for our free weekly Newsletter here, the latest 3D printing news straight to your inbox! You can also find all our videos on our YouTube channel.
*All Photo Credits: Bosch Advanced Ceramics
Download from online (Thingiverse, Printables, etc.)
Design yourself (3D modeling/CAD)
Your email address will not be published. Required fields are marked *
Name *
Email *
Website
I agree to have my personal data saved in accordance with the privacy policy.
3Dnatives is the largest international online media platform on 3D printing and its applications. With its in-depth analysis of the market, 3Dnatives gets over 1 million unique visitors per month and is currently available in English, French, Spanish, German, Italian. 3Dnatives works with key Additive Manufacturing market players and offers a variety of services such as a 3D printing price comparison engine, B2B consulting and B2B brand content, event management and much more!
84 countries and 60k+ stakeholders strong, SPE unites plastics professionals worldwide – helping them succeed and strengthening their skills through networking, events, training, and knowledge sharing. For more information, visit www.4spe.org.
Compare Desktop 3D Printers Compare Professional 3D Printers Compare 3D Scanners 3D Printing Directory Choose a 3D printer 3D Printing Directory Event Board Job Board Newsletter Advertising
3Dnatives Europe 157 Boulevard Macdonald 75019, Paris France
SPE US Office 83 Wooster Heights Road, Suite 125 Danbury, CT 06810 P +1 203.740.5400
Speed Europe Serskampsteenweg 135A 9230 Wetteren Belgium P +32 498 85 07 32
SPE Middle East Office N. ESO:14, Desk 34 Sheikh Rashid Tower, Seventh Floor Dubai World Trade Center P.O. Box 9204 Dubai, UAE
Download from online (Thingiverse, Printables, etc.)
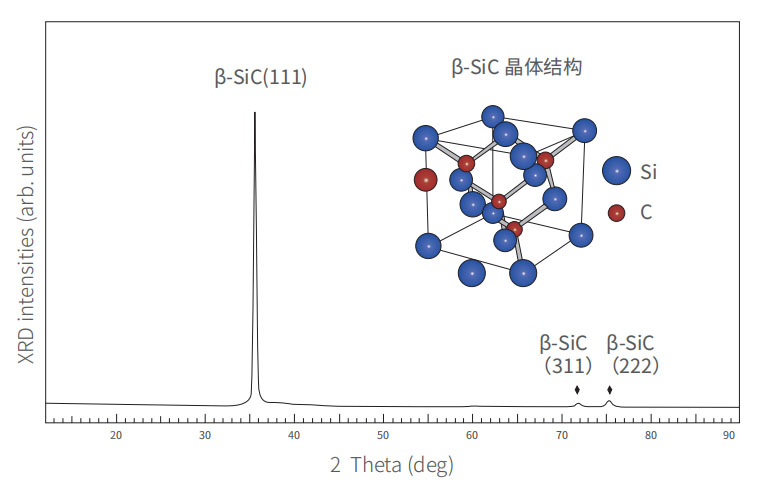
Silicon-Based GaN Epitaxy Design yourself (3D modeling/CAD)