Receive our weekly Newsletter and set tailored daily news alerts.
Karl Mayer Group launches its Energy Efficiency Solution for the smart use of energy. Single Knitting Machine
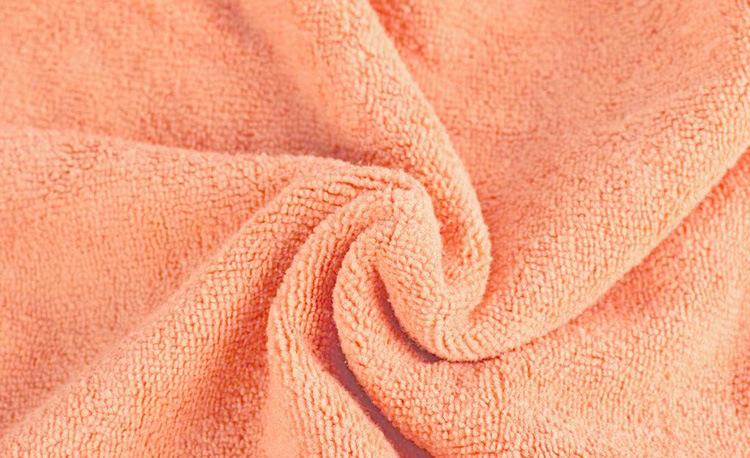
Knitting Industry | Obertshausen, Germany
Energy efficiency and sustainability are becoming increasingly important, particularly for production companies. Rising energy costs, stricter environmental regulations and growing awareness of environmental concerns are making energy consumption an increasingly important success factor, particularly in the machinery sector – the heart of value creation in many companies.
“Both energy costs in general and the energy costs of production facilities have an ever-greater influence on total production costs. Through active and continuous management, huge savings in costs and CO2 emissions are possible,” says Product Owner Digital Markus Bahde at the Karl Mayer Group.
Mastering the challenges around energy demand requires one thing above all - substantial knowledge. Application-oriented, continuously recording and analysing data on real consumption enables companies to manage energy efficiently, but may require a significant amount of measurement technology, personnel and time.
In addition, currently there are only a few experts with real-world experience in energy issues from the field of production. Therefore, the new implementation of energy data analyses often suffers from complex processes with considerable trial-and-error loops.
With its new Energy Efficiency Solution, the Karl Mayer Group is taking a different, efficient and economical path to enable its customers to achieve energy transparency that meets their requirements.
The Energy Efficiency Solution from Karl Mayer is a cloud-based solution that combines the latest sensor technology with a specifically developed analysis software. The high-tech connection enables customers to visualise selected data to identify their energy consumption. The software displays the captured and processed data of networked machines and records the power consumption for production, heating and standby operation modes. Companies wishing to leverage these opportunities will have easy access to the Energy Efficiency Solution via my.KM.ON, the Karl Mayer customer portal.
Different application scenarios, highest efficiency
The Energy Efficiency Solution provides customers with energy management support in a variety of ways. For example, customers can gain an overview of the actual situation of their production processes by displaying the energy data of individual machines and the entire machine fleet in real time, generating an energy data analysis from the past and using it to generate their own energy reports. In addition, it is possible to efficiently control machine heat-up without manual configuration on site.
Display of real-time energy data
Customers benefit from an overview of the current consumption data with a graduated viewing depth. A general compilation contains the values of the entire machine fleet and each individual machine. For more dedicated monitoring, the values for the current day, week, month and year can be output.
A closer look reveals more details. The display contains the details of the performance and energy data of an individual machine, broken down according to the respective machine status, and parameters for the power supply.
Analysis of historical energy data
In addition to recording energy consumption, the Energy Efficiency Solution offers an analysis of the data. On the basis of processed data from an elapsed time period, customers can compare the energy data of different machines or different fabrics respectively articles to each other.
The comparison of the consumption values of the machines can be adapted to the analysis goals by using different variables. The reference range to which the consumption refers for example, per day, month or year, and the period and subject of the comparison can be set. Likewise, it is possible to choose the amount of energy used, costs and CO2 emissions. The respective data can also be accumulated.
The comparative view of textile products includes the total amount of energy consumed and the total costs incurred. Net consumption, i.e. consumption for the actual production process without energy requirements during stoppages, is also visible.
Based on the analysed historical energy data, the Energy Efficiency Solution enables customers to generate energy reports for individual machines or for their entire machine fleet and save them as PDF files. Monthly and annual reports with a focus on the CO2 or kWh value are possible.
To reduce energy consumption, it may be useful to switch off the machine heating system during stoppages. The Energy Efficiency Solution offers the option of managing the heating operation for the entire machine park without manual configuration on site, which is extremely efficient. Customers simply define the desired daily production times in one or more templates and assign the templates to the individual machines. Next, the software develops the respective heat-up times from the input information. With the help of the templates, a weekly timer schedule can also be created. According to it, each individual machine is put into production readiness on the predetermined date.
On the basis of all the information and options offered by the Energy Efficiency Solution, customers can take effective measures to reduce energy consumption and in turn, their CO2 emissions.
“In a real-world pilot project, our Energy Efficiency Solution has already achieved monthly energy savings of approximately 5 to 10%,” says Markus Bahde.
The possible savings depend, of course, on the use and capacity utilisation of each machine and the maturity of the measures taken so far to reduce consumption. It is also possible to quantify and demonstrate the reduction in CO2 emissions.
The launch of the Energy Efficiency Solution is planned for this month and the solution will be rolled out gradually. KAMCOS 2 machines from Karl Mayer will be included in the launch, but Markus Bahde and his team are already working on using the solution on KAMCOS 1 machines. They want to use machine-side product updates for the successive retrofitting. In future, the Energy Efficiency Solution will be available for all Karl Mayer machines.
The advantages of yarn intermingling for warp knitting
Advantages of yarn intermingling for warp knitting
Turkish specialist breathes new life into old circular knitting machines
Business intelligence for the fibre, textiles and apparel industries: technologies, innovations, markets, investments, trade policy, sourcing, strategy...
This week's key stories, direct to your inbox. Be the first to know.

Tubular Knitting Machine © Copyright Knitting Industry. Knitting Industry is an online publication of Inside Textiles Ltd. PO Box 271, Nantwich, CW5 9BT United Kingdom Registered in England No 04687617