The biggest vertical shot blast machine ever built by Rösler goes to China.
Stainless steel is one of the most important raw materials for many industries, such as medical engineering, ship building, aerospace, etc. Accordingly, high volumes of stainless steel are used all over the world. To cope with the increasing demand, TISCO, one of the largest manufacturers of stainless steel, modernised the production line in its hot rolling mill for stainless steel plates. As partner in this challenging project, Rösler built the biggest vertical shot blast machine in the company’s history. Elbow

As part of the China Baowu Steel Group Corporation Limited the Taiyuan Iron and Steel Group Co., in short TISCO, is one of the largest and most renowned suppliers of steel in the world. For a long time the company, located in Taiyuan in the Chinese province Shanxi, has specialised in, among other industrial goods, the development and production of stainless steel products such as plates and sheets. Since 2020 a huge modernisation project has been underway for this business division with the goal to update the production line in the hot rolling mill for stainless steel plates with state-of-the-art equipment, including a new shot blast and pickling system. Once the project is completed, the entire line will run fully automatically. The technical specifications for the shot blast system, processing steel plates up to 4,100mm long, 160mm thick and with a maximum weight of 35 tons, were very detailed and strict; particularly with regard to the shot blasting results and the workpiece handling. The challenge for the Rösler engineers was to design and build a machine that guarantees a high-quality, high-precision finish in the micrometre range and high throughput. With regard to size and production speed the new shot blast system dwarfs the equipment that the company has ever built in this field.
Some of the TISCO requirements were that the steel plates must pass through the shot blast machine at a speed of 7m/min, the surface roughness cannot exceed Ra = 4.0µm, and the surface finish must correspond to A/B Sa 2.5. To prevent even minimal damage on the workpiece surface by the transport rollers, the customer demanded the plates to be transported through the shot blast machine and the subsequent pickling system in vertical position. A challenge was that the plates are delivered horizontally and must be changed to vertical position before entering the shot blast machine.
To meet the customer’s surface quality demands within the specified timeframe, the Rösler engineers developed an innovative equipment concept. It combines two identical shot blast machines into one system, where the stainless steel plates are passing through the two machines sequentially, and each machine uses a different blast media. The individual machines are equipped with 12 Gamma 400G turbines with an installed power of 37kW per turbine. On each side of the blast chamber six turbines are mounted at an angle. This turbine arrangement ensures that the plates are evenly covered by the blast media across their entire width. The total blast media throughput per machine amounts to 12,000kg/minute – a huge quantity compared to the throughput of between 2,000 and 3,000kg in standard shot blast machines. The high media throughput posed a particular challenge for the wear protection of the two machines. This challenge was met by fabricating the blast chamber from manganese steel and lining it with 10mm thick, easily replaceable, wear plates – also made from manganese steel.
For shot blasting operations, where a higher surface roughness is specified, each machine can be run separately. In such cases the transport speed of the steel plates is reduced to 4m/minute. To prevent media spillage, each machine is equipped with a high-performance blow-off system.
The large size of the steel plates and their high weight demanded an extremely sturdy design of the two shot blast machines. For example, the maximum load per running meter amounts to four tons. The overall machine dimensions are also impressive: The entire system is 17m long and 14m high. It was placed in a pit with a depth of 2.5m. The blast media cleaning system and media hopper were placed on the roof of each shot blast machine. For quick and easy maintenance the machines are equipped with four inspection platforms on different levels that can be easily reached by suitable stairways. This enhances the already impressive appearance of the shot blast system, designed for processing 315,000 tons of stainless steel plates.
The production unit consisting of the two Rosler shot blast machines and the pickling line is equipped with a level 2 control system. This upper-level system provides all the data required for the process, for example, the plate type and the required surface roughness. The information also specifies whether a special plate type must pass through both shot blast machines or just one. This ensures that the required surface roughness and finish values are achieved without any manual intervention whatsoever.
The entire vertical shot blasting system was designed and built in Germany. It was shipped to China by sea in 21 containers. Rösler service engineers, some of them from Germany, installed the system at the customer’s location. Another challenge was that the installation had to take place during a time of strict Chinese travel restrictions and quarantine regulations. In addition, the installation had to be carefully coordinated with the service engineers of the company supplying the pickling line. Vasili Schaermann at Rösler reports: “Only after the installation at TISCO could we test the entire system. Because of the extraordinary size of the shot blast system, such a test was not possible during the production phase at our plant in Germany. Fortunately, the commissioning at the customer location was successful. Actually, the entire project went very well. In the future we will build other vertical shot blast machines, and I would like to point out that we are pleased with the cooperation between TISCO and Rösler.”
The customer was very satisfied with how the project was handled and the achieved shot blasting results. The customer’s employees were particularly impressed by the ability of the Rösler experts to fully satisfy the TISCO demands. The big, sophisticated shot blasting system from Germany will certainly help TISCO to strengthen its position as one of the leading stainless manufacturers in the world.
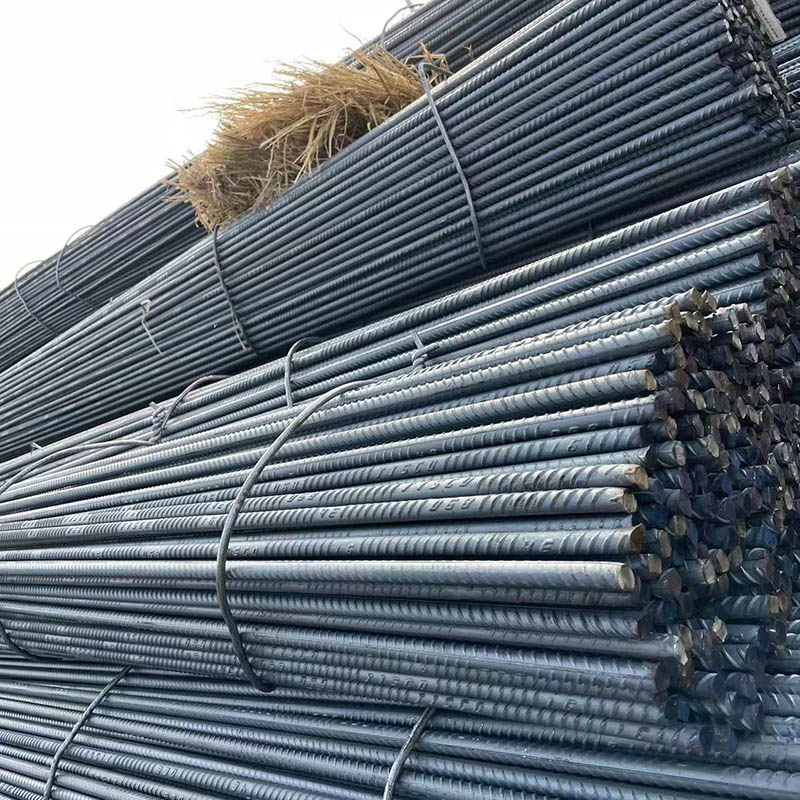
Hot Dipped Galvanized Rectangle Pipe © Setform Limited 2019-2024 | Privacy policy | Archive