In this interview, Technetics explores the exciting world of spring-energized and magnetic mechanical seals and their applications.
A spring-energized mechanical seal refers to the force used to maintain the seal face and the mating ring in close contact, which is supplied by a mechanical spring device. This device can be a wave spring, a coil spring, or a metal bellows. Occasionally, you may encounter the term "spring-energized seals" when referring to a secondary seal with a Teflon jacket. However, we specifically address the mechanical spring's role in providing the closing force for this discussion. Wear Ring For Pump
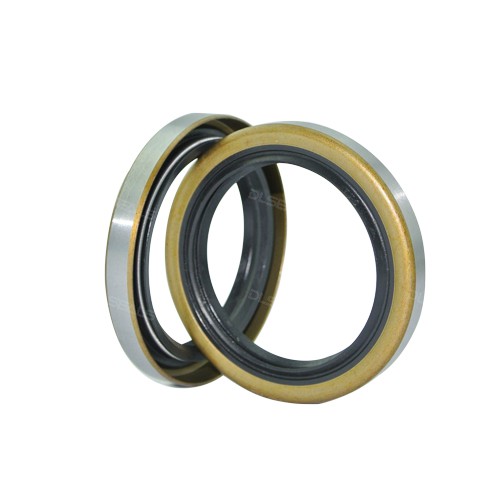
We often hear installation-related concerns from our customers, where it is challenging to handle and maintain the parts together, and they are susceptible to damage with magnetic seals. In contrast, spring-energized seals are more forgiving in such conditions, as the faces can be separated.
Another common issue raised by our customers pertains to performance, specifically regarding the restoring force and temperature limitations. The yield of the process for producing magnetic faces tends to be low, leading to potential delays in on-time delivery, quality control problems, and supply limitations, which can significantly impact the supply chain.
To summarize, these are the recurring issues our customers frequently encounter when using magnetic mechanical seals. They often face challenges in handling the components, as failure to keep the two faces together can result in damage. Performance problems are prevalent.
Yield problems, particularly with the magnet component, give rise to various issues, including supply continuity problems. Additionally, the limited availability of manufacturers for these seals compounds the difficulties for our customers.
The primary challenge we often hear from our customers is that they lack the space necessary to accommodate a spring-energized mechanical seal.
We have successfully collaborated with numerous customers to replace a magnetic seal with a spring-energized mechanical seal, ensuring it fits within their existing envelope and constraints. This process has been accomplished without encountering significant technical obstacles, and we have succeeded in these applications.
We possess extensive experience in replacing these types of seals on aerospace gearboxes and accessory pads that serve various end applications, including helicopters, commercial aircraft, and military aircraft.
Additionally, I would like to mention that we have successfully executed upgrade projects of this nature in the past. Such projects include the replacement of a magnetic seal that entered into service in 2018. The upgraded spring-energized mechanical seal has demonstrated flawless performance, even in a high-running commercial application.
One of the primary disparities between a spring-energized mechanical seal and a magnetic seal is the behavior of the closing force supplied by the spring or the magnet. The closing force, responsible for keeping the seal faces together, is furnished by the spring in applications with low delta-P or low-pressure differentials.
In a mechanical spring-energized seal, this force exhibits a linear relationship with the spring constant and displacement. For instance, the force is doubled if you reduce the spring's distance by half. In contrast, the magnetic force in a magnetic seal adheres to an inverse square law. For instance, if you double the distance between the faces, the force diminishes by a factor of four.
The term “restoring force” in the context of a mechanical seal refers to the force responsible for closing or bringing the sealing faces back together. In various applications, factors like runout, vibration, or maneuver loads may momentarily cause these sealing faces to separate. The spring constant of a spring-energized mechanical seal plays a crucial role, as it establishes a linear relationship with the distance by which the faces separate.
As a result, the force aiming to return the faces to their normal operating position increases proportionally to the degree of separation. In contrast, when dealing with a magnetic seal, the restoring force diminishes according to the inverse square law as the faces move apart, diminishing with the square of the distance.
In the case of a spring-energized mechanical seal, we enjoy a wide array of material options, allowing us to select based on the seal configuration and operational conditions. We can opt for materials with exceptional temperature resistance, capable of withstanding temperatures of nearly 1,000 degrees Fahrenheit or even lower temperature ranges in cryogenic environments. Essentially, there are very few limitations on our material choices.
When dealing with a magnetic seal, the material options are more restricted. This constraint arises from the need for a permanent magnet with high magnetic flux, which tends to exhibit temperature limitations. In high-temperature settings, these materials lose their magnetic properties.
We make design compromises that affect the mating materials' hardness and porosity, which are the wear components. One approach to mitigate these challenges is using multi-piece mating rings and seals, which introduces complexity to the overall system design.
When it comes to a mechanical spring-energized seal, we typically refer to the stator part as the seal and the rotating part as the mating ring. During the assembly process, these two components do not need to maintain close contact with each other. You can install the seal in a housing and the mating ring onto a shaft as separate assemblies, bringing them together later.
However, when dealing with a mechanical magnetic seal, the stator and rotor pieces must remain in close contact throughout the assembly process. Keeping these two components separate in the spring-energized seal also allows for inspecting their surfaces or opportunities to clean these parts during installation and handling.
In most, if not all, of the applications we have examined, the axial and radial spaces we have to work with are sufficient to accommodate either technology. Therefore, we have not found this to be true in the applications we have worked on. We have been able to devise solutions that fit within the available space.
One concern we have received from some OEMs is that these seals are positioned close to critical bearings within the system. When wear debris is generated by gears, shafts, or other system components and transported by the lubrication system, metallic or magnetic particles can accumulate around the seal interface within the magnetic field.
This accumulation can function like a chip collector. The concern is that if this debris buildup dislodges, it could lead to secondary damage to the bearings and potentially result in more severe failure modes.
We frequently utilize carbon materials for the stator, typically the non-rotating part. These materials exhibit low friction characteristics. For the mating materials, we generally opt for hardened steels, such as bearing-type steels. In certain applications, we can also employ ceramics or coatings to enhance wear resistance and lifespan, depending on the application's specific requirements.
When considering a marine environment, our primary focus is material selection based on the operating fluids it may encounter. We take into account factors such as corrosion resistance, especially to saltwater. This leads us to materials like stainless steel, which is known for its excellent corrosion resistance.
Additionally, we carefully choose a seal nose material that does not release substances into the water, among other considerations. With a wide range of material options, we encounter very few limitations in our choices. We review the specific application details and tailor our selections accordingly.
Aaron Glafenhein is a Senior Design Engineer specializing in mechanical seals. His passion for engineering started at a young age, spending his childhood taking things apart, building new things, and experimenting with materials. Aaron's interest in space and engineering led him to pursue a career in aerospace engineering, choosing Embry-Riddle due to its renowned reputation in this field. After graduation, he delved into learning structural analysis, bellows, and fluid system technologies, working on major programs such as the SLS, Ares I, and Orion. Through these experiences, Aaron gained invaluable knowledge in documentation, analysis, and testing. In recent years, he has focused on dynamic face seal technologies and hydrodynamic seals, playing a crucial role in successfully developing, manufacturing, and testing Technetics' first hydrodynamic seals.
Jason Riggs has had a hand in various roles such as Sales, Marketing, Product Management, Engineering and Mergers and Acquisitions to push Technetics' organic and inorganic growth strategies forward. He serves as the Director of Sales for the Americas and the Aerospace Market Manager for Technetics. He holds the responsibility of leading the global Aerospace strategy for Technetics Group. Riggs has a vast experience of working in the aerospace industry. He obtained a BS degree from Arizona State University and an MBA from the University of Phoenix.
This information has been sourced, reviewed and adapted from materials provided by Technetics Group.
For more information on this source, please visit Technetics Group.
Disclaimer: The views expressed here are those of the interviewee and do not necessarily represent the views of AZoM.com Limited (T/A) AZoNetwork, the owner and operator of this website. This disclaimer forms part of the Terms and Conditions of use of this website.
Please use one of the following formats to cite this article in your essay, paper or report:
Technetics Group. (2024, March 13). The ABC of Spring-Energized and Magnetic Mechanical Seals. AZoM. Retrieved on June 21, 2024 from https://www.azom.com/article.aspx?ArticleID=23135.
Technetics Group. "The ABC of Spring-Energized and Magnetic Mechanical Seals". AZoM. 21 June 2024. <https://www.azom.com/article.aspx?ArticleID=23135>.
Technetics Group. "The ABC of Spring-Energized and Magnetic Mechanical Seals". AZoM. https://www.azom.com/article.aspx?ArticleID=23135. (accessed June 21, 2024).
Technetics Group. 2024. The ABC of Spring-Energized and Magnetic Mechanical Seals. AZoM, viewed 21 June 2024, https://www.azom.com/article.aspx?ArticleID=23135.
Do you have a question you'd like to ask regarding this article?
Your AI Powered Scientific Assistant
Hi, I'm Azthena, you can trust me to find commercial scientific answers from AZoNetwork.com.
A few things you need to know before we start. Please read and accept to continue.
Azthena may occasionally provide inaccurate responses. Read the full terms.
While we only use edited and approved content for Azthena answers, it may on occasions provide incorrect responses. Please confirm any data provided with the related suppliers or authors. We do not provide medical advice, if you search for medical information you must always consult a medical professional before acting on any information provided.
Your questions, but not your email details will be shared with OpenAI and retained for 30 days in accordance with their privacy principles.
Please do not ask questions that use sensitive or confidential information.
Read the full Terms & Conditions.
AZoM.com - An AZoNetwork Site
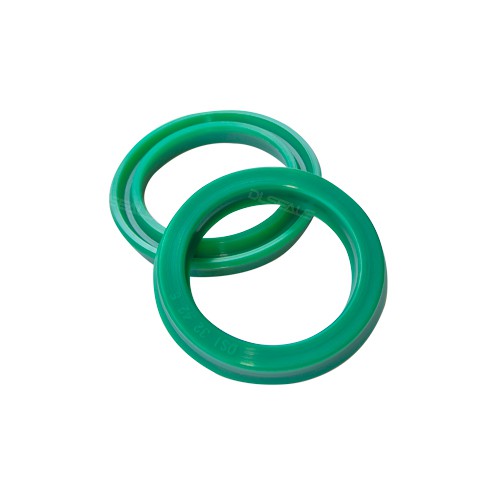
Foam Window Seal Manufacturers Owned and operated by AZoNetwork, © 2000-2024