Alberto Bottura, Co-Owner and Managing Director of Italian refrigeration component manufacturer OLAB, detailed the uniqueness and advantages of the company’s weld-free CO2 (R744) ball valve, the Series Revolution, in a recent interview with ATMOsphere CEO and Founder Marc Chasserot. ATMOsphere is the publisher of NaturalRefrigerants.com.
Traditionally, refrigeration valves are attached to piping via welding. However, the proximity of the welding to the ball valve can accidentally burn or weaken the gasket inside the valve during system assembly, Bottura told Chasserot. A weakened gasket can result in refrigerant leaks, especially at the high operating pressures of CO2 systems. Electric Ball Valve
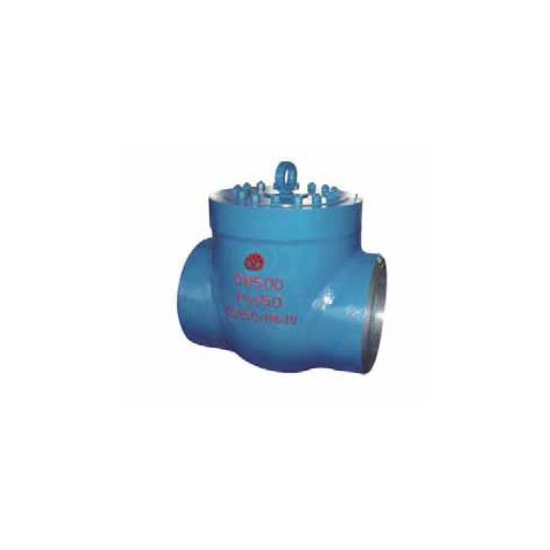
“Our clients don’t have issues with leaky valves because instead of welding the valve directly to the tubing, we provide a flange to weld to the piping with the valve safely on the table,” Bottura said. Stainless-steel screws and washers attach the valve to the welded flange.
“We 100% guarantee that every gasket inside our valve is in perfect condition after installation,” he said. Bottura added that the assembly improves valve serviceability and end-of-life changeout without cutting the tubing and rewelding in a new valve.
OLAB’s Series Revolution ball valve ‒ rated for 150bar (2,176psi), with a safety factor of three (450bar/6,527psi) ‒ now accommodates piping up to 65mm (2.6in) in diameter, according to Bottura.
When it was launched in April 2023, the valve accommodated up to 60.3mm (2.4in)-diameter piping, with 10mm (0.4in)’s being the smallest size available. The valve operates in temperatures ranging from −50 to 150°C (−58 to 302°F).
Bottura indicated that OLAB’s weld-free CO2 ball valve costs roughly the same as traditional ones on the market. “With production technology, I can produce a quality product for around the same price,” he said
OLAB’s Series Revolution stainless-steel flanged ball valve, designed to eliminate leaks in transcritical CO2 systems, was one of three products nominated for the ATMO 2023 Innovation of the Year Award for North America.
At its 30,000m2 (323,000ft2) manufacturing facility in Brescia, Italy, OLAB ‒ a multigenerational family-run business ‒ produces millions of components for various industries annually.
“The vision of total integration and complete supervision of the production process has led us to invest heavily in highly technological machinery designed around our needs,” the company says on its website.
According to Bottura, producing high-quality components starts with a detail-oriented philosophy, including strategic partnerships with material suppliers to obtain the highest-quality grade of raw materials.
“Once we have certified materials, we test and guarantee every product as it passes through production, including checking every dimension step by step,” he said. Individual tests confirm each final component is a “perfect” product.
After a tour of the facility, Chasserot called the amount of testing “mindblowing.”
“As a customer, you will not get a faulty product because of the repeated testing,” Chasserot said.
Bottura noted that four years ago, OLAB decided to invest in manufacturing components for CO2 and propane (R290) systems. “We have the technology to develop solutions for the industry,” he said, with the company currently developing new products in partnership with OEMs.
In addition to the Series Revolution ball valve, the company produces other components compatible with CO2 and propane systems, including solenoid valves rated to 150bar, check valves to 120bar (1,740psi), manifolds at 60/150bar (870psi) and stainless-steel pipe fittings at 150bar.
“We 100% guarantee that every gasket inside our valve is in perfect condition after installation.”
Alberto Bottura, Co-Owner and Managing Director of OLAB
OLAB Series Revolution – Flanged Ball Valve
Username or email address *
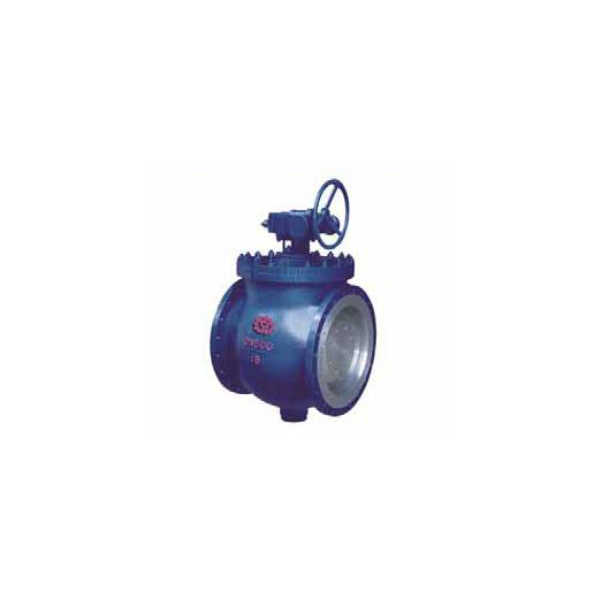
Wafer Check Valve No products in the cart.