Maintaining a safe workplace is everyone’s responsibility. This section offers information and tools to help you manage risks and protect health, safety and wellbeing.
Everything you need to know about worker’s compensation insurance, whether you’re an employer needing to insure your workers or a worker who’s been injured at work. Horizontal Elbow
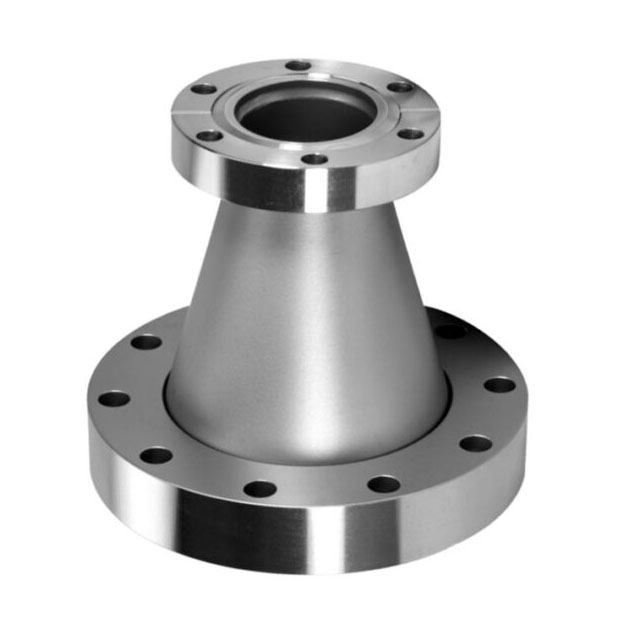
Your rehabilitation and return to work journey will be easier if you know your options, the steps to take, and who’s responsible for what.
Information about work health and safety and electrical licensing, registration and training.
Learn about the Acts, Regulations and codes of practice we are responsible for and find information on workplace inspections and prosecutions.
Find health and safety information and guidance about your industry and the kind of work you do.
A listing of useful resources available on the website. Use the in-page search or filters to find what you need.
The purpose of this safety alert is to highlight the risk of elastic energy being released when wear plates on excavator buckets or similar parts on other equipment are being removed or repaired.
Persons conducting a business or undertaking (PCBUs) and workers involved in similar work tasks should observe the risks identified and apply the principles outlined in this alert to manage the risks of exposing workers to the sudden release of stored energy by parts of the equipment.
In August 2017 a coal mine worker received fatal injuries while removing a large wear plate from the bottom of a large excavator bucket.
The worker was using an air arc gouging process to remove the wear plate by cutting it into smaller sections. At some point, the stored energy in the plate resulted in an uncontrolled spring-back of the plate, which sprang upwards and struck the worker.
Photographs 1 and 2 below show the underside of the excavator bucket and the wear plate involved. Similar incidents have also occurred with equipment other than excavator buckets.
An investigation into the incident by the Queensland Department of Natural Resources, Mines and Energy (DNRME) identified the primary contributing factor of the incident was an indentation of the excavator bucket. Although the wear plate was originally roll formed to the shape of the excavator bucket, the indentation (deformation) of the bucket and wear plate induced additional stresses in the wear plate and storage of elastic spring-back energy in the material.
In addition, most of the vertical welds on the sides of the plate had cracked, which did not prevent the plate from springing rapidly when the lower section of the plate was cut. It appears the larger wear plate design was a previous modification from the original equipment manufacturer's (OEM) bucket design where multiple smaller wear plates were used. There was no evidence that any risk assessment was conducted prior to modifying the design of the external wear plates.
There are additional factors that can cause elastic spring-back in plates. The factors listed below were not necessarily all present in the August 2017 incident. However, these factors may be present in other configurations, either alone or in combination:
DNRME safety alerts and investigation report provides additional information about this incident and the factors that can contribute to potential spring-back (refer to Further information below).
All work tasks involving the removal or repair of wear plates on excavator buckets or other similar tasks on equipment must be risk assessed for the potential for spring-back energy to be released during the process. The level of risk of spring-back will depend on the size of the plate, the contributing factors described above and the process by which the plate is to be removed. Greater precaution and planning of the removal procedure will need to be taken for larger wear plates, even if signs of the potential for spring-back are not obvious. For example, even if there are no signs of indentations, cracking or wear, excessive force may have been applied to the plate during installation to fit it to the rest of the structure. Removal of wear plates should be done in a systematic manner to control the release of energy. This may include reinstating cracked welds or bolts or alternate bracing or restraint of the plate as the elements of the plate are released or removed.
In general, designs using several smaller wear plates instead of one large wear plate are recommended, as this will reduce the amount of stored energy and elastic spring-back potential that must be controlled at any one time during removal. People who alter the design of plant have designer duties to assess the risks of the altered design and ensure it is safe and without risks to the health and safety of workers throughout the life of the plant.
Additional considerations to control the risks of spring-back include:
More information can be obtained from the following:
Give us feedback about this page
We appreciate your input into making our site better. You can let us know your thoughts here. If your enquiry is about something more specific, please visit our Contact us page.
If you'd like someone to get back to you about your feedback, include your contact details below.
WorkSafe.qld.gov.au is the official home of:
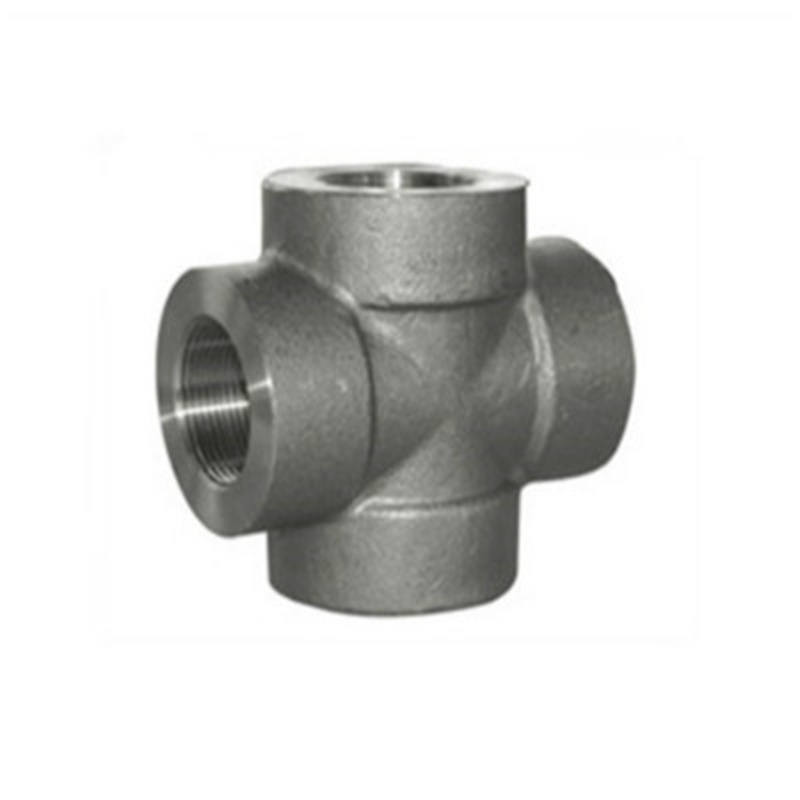
Female Threaded Elbow We deeply acknowledge and pay respect to all Aboriginal and Torres Strait Islander peoples, and their Elders past and present. We thank the Traditional Custodians of Country throughout Australia for their ongoing custodianship of land, waters, culture and community.