Imparting complex geometry on the inside (and the outside) of workpieces requires the right equipment, the right cutting tools and the expertise to make the most of both.
Available with various options for automation, the USC-M series of machines are particularly useful for drilling the lengthy, crisscrossing waterlines used to cool plastic-injection-mold tooling. (Photo courtesy of Unisig.) Deep Hole Gundrill
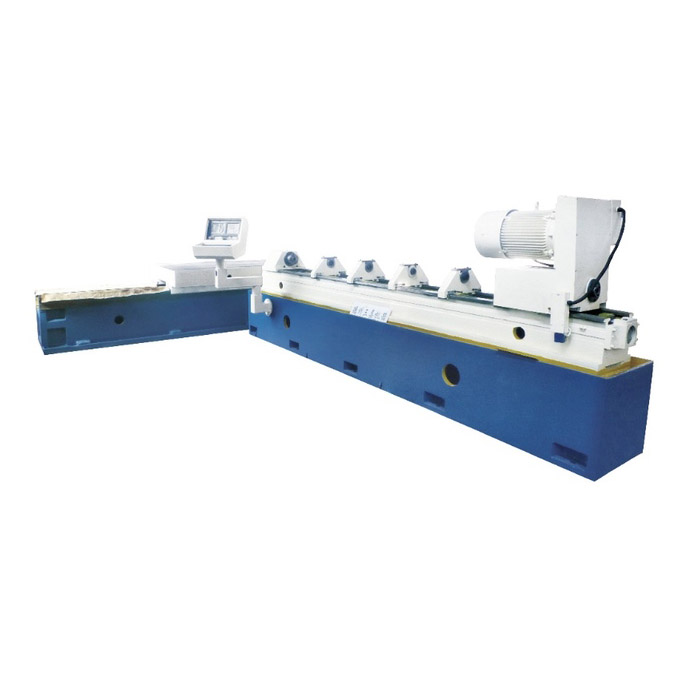
Here are examples of deep holes drilled on Unisig machining centers. (Photo courtesy of Unisig).
Internal geometry like this is a good fit for bottle-boring tools, which use CNC-actuated axes to drive cutting edges away from and back into the shank as needed to create internal profiles. Quality control is a particular concern with deep-hole drilling. Many applications require periodic destructive testing or more creative solutions, such as tracking the process via cameras that monitor changes and trends in chip formation. (Photo courtesy of Unisig.)
Modular fixturing reduced setups for this mold component during machining on a USC-M platform. Unisig’s use of this fixturing in its own machine-building process is a lesson taken from moldmaking customers. Mr. Fettig says it works like “stacking Lego blocks” to provide both repeatable, rigid mounting and single-setup access to six sides of a workpiece.
Here are some examples of gundrills, BTA drills and specialty tools, including solid carbide, brazed-tip and indexable models.
Imagine the sound of a 55-gallon drum filling to the brim in minutes flat with a steady stream of coins dropped unceremoniously from high above. That is how Anthony Fettig, CEO of machine tool builder Unisig, described what it’s like to witness the company’s largest, most powerful deep-hole-drilling machines in action during a recent press event.
With more than 300 horsepower behind the tool, holes can be drilled to extreme diameters and depths (20 inches and 32 feet, respectively) in even the most difficult-to-machine materials, including Inconel and other nickel-based alloys. Automatic toolchangers can accommodate shanks as long as 24 inches on some models, and the machines’ beds can be large enough to require shipping in separate sections, each measuring as long as 25 feet, for precision assembly later.
Unisig’s line of deep-hole-drilling machines is not limited to these behemoths. On the other end of the spectrum are machines designed for holes measuring less than 1-inch deep and no broader than 0.04 inch in diameter.
The most important consideration in drilling, Mr. Fettig says, isn’t necessarily the depth or the diameter of the hole: It’s more about the ratio between the two. “We perk up and get happy,” Mr. Fettig says about being presented with depth-to-diameter ratios ranging to 300:1. “We know we can take (customers’) problems away.”
While the company is known for deep-hole drilling, the term itself does not do justice to the breadth of these machines’ capabilities, nor to the breadth of the company’s engineering expertise. With the typical application defined by more than just challenging hole-making operations, he believes “deep-hole machining” is a better descriptor.
In an era when manufacturers of all stripes seek to consolidate operations on fewer pieces of equipment, Unisig has taken the position that a gundrill does not have to be just a gundrill. Indeed, much of the builder’s equipment demonstrates a focus on external workpiece features as well as internal ones.
Although stock delivery machines are available, a significant proportion of Unisig machines are made to order from modular platforms. One example of such a platform is the USC-M line, which combines powerful hole-making with all the general machining capability of a five-axis mill. This machine is particularly useful for plastic-injection moldmakers that annot afford spending too much time drilling deep water-cooling lines. Unisig machines are designed to perform these operations in the same setup as the complex contouring required for exterior features, Mr. Fettig says. Although the machines trend large, workpieces don’t have to be, he continues, explaining that table rigidity and overall volumetric precision eliminate the need to ensure that smaller workpieces (or features of those large enough to overhang the table) are located in a specific “sweet spot.”
Five-axis capability is a function of this rotary table as well as a dedicated, 50-taper, tilting milling spindle mounted parallel to the machine’s drilling spindle. Machining is said to be just as precise—that is, volumetric accuracy is the same—regardless of the tilting spindle’s angle and position within the workzone. “Performance and accuracy aren’t compromised in seemingly less rigid headstock positions,” he says. “Compound angles are effortless.”
He attributes this precision to scale feedback and finely tuned, high-performance servo drives that facilitate precise interpolation. He also credits the company’s strategy of building machines “from the ground up” at the Milwaukee factory. Even CNC engineering is performed in house, including the defining of kinematics and other associated tasks, with components sourced directly from such manufacturers as Siemens, Heidenhain and FANUC.
Other platforms are similarly configured for work ranging from oil and gas components to aircraft landing gear and various hydraulic systems. Each machine is made to order, with automation systems in particular differing widely from customer to customer. Beyond robot-tending and mulit-machine cells of multi-spindle drilling machines, automation systems range from pallet changers to complex conveyors, roller steadies and other systems involving in-process gaging and even extra servo-driven axes of motion dedicated to streamlining setup and unloading alike.
Mr. Fettig emphasizes that the reason why “deep-hole drilling” is inadequate to describe what Unisig does has as much to do with what goes on inside a hole as what goes on outside of it. Beyond basic drilling, reaming, tapping and so forth, potential operations include counterboring, slotting and trepanning. Profiling is common as well, including stepped diameters, precisely curved internal radii, sculpted contours and requirements for specific levels of surface finish.
When it comes to this kind of internal machining, cutting tools literally take the initiative. “The majority of deep-hole tools and processes are based around the idea of the tool guiding itself close to the cutting edge,” he says. Standard deep-hole drilling tools come in two basic varieties: gundrills and Boring and Trepanning Association (BTA) drills.
The tools most commonly associated with extreme length-to-diameter ratios, gundrills are available with single-effective geometry. This means the cutting action is all on one side, a contrast with the double-effective geometry that characterizes most conventional drills. This construction provides the necessary clearance for chips and coolant. Typically, wear pads on the periphery help keep the tool in place and provide a burnishing action that smooths the workpiece surface. Point angle and location influence cutting thrust and radial force on the tool at a given set of parameters. The most precise hole making is achieved when tool and workpiece rotate together, he adds, and rotating the workpiece by itself typically produces better results than rotating the tool by itself.
Solid-carbide gundrills are particularly rigid. These tools offer the advantage of resharpening, but they are effective only at diameters smaller than about 300 mm. After that point, they tend to become expensive and/or and fragile, Mr. Fettig says. For larger diameters, tools are available with steel shanks and brazed carbide tips, with “V” notches rolled into the steel for chip evacuation. Alternatively, indexable-insert models eliminate the need to discard the entire tool when worn. That said, these models might not be as precise as brazed-tip tools because each insert-tool connection is subject to variance.
Whereas a gundrill is designed for internal coolant delivery and external chip exhaust, BTA drilling routines involve evacuating chips and coolant through the center of the tool itself, in the opposite direction of the feed. As a result, holes should be at least a certain size—about ½ inch—before considering this tooling, Mr. Fettig says. As is the case with gundrills, BTA tools are available with both brazed and indexable cutting edges. These tools also come in spade-tip geometries, which Mr. Fettig says are particularly useful for cross-holes (such as those typical of the water-cooling lines in the aforementioned moldmaking applications). Although he emphasizes that the gap is closing, BTA drills generally offer higher feed rates, greater rigidity and improved chip control.
Beyond these basic tool types, many applications involve custom form tools for imparting more complex profiles. Generalities are difficult to draw about these widely varied offerings; suffice it to say that even familiar-looking geometries require manufacturing for a specific size bore, at the least. For example, bottle-boring tools use CNC-actuated axes to drive cutting edges away from and back into the shank as needed to create internal profiles. Without precise sizing, such action would be impossible. “Given that these tools have to guide themselves, careful planning is critical,” Mr. Fettig says. The same could be said of applications that require integrating that hole-making process with complex outside machining as well.
Finding a way to fixture contoured marine propellors proved to be this shop’s biggest challenge in developing an effective automated machining cell.
Many job shops start in a garage with a used mill and a manual lathe. The owners of this Utah job shop took a different tack. Along the way to a very successful business, they've debunked a bunch of myths commonly held about job shops.
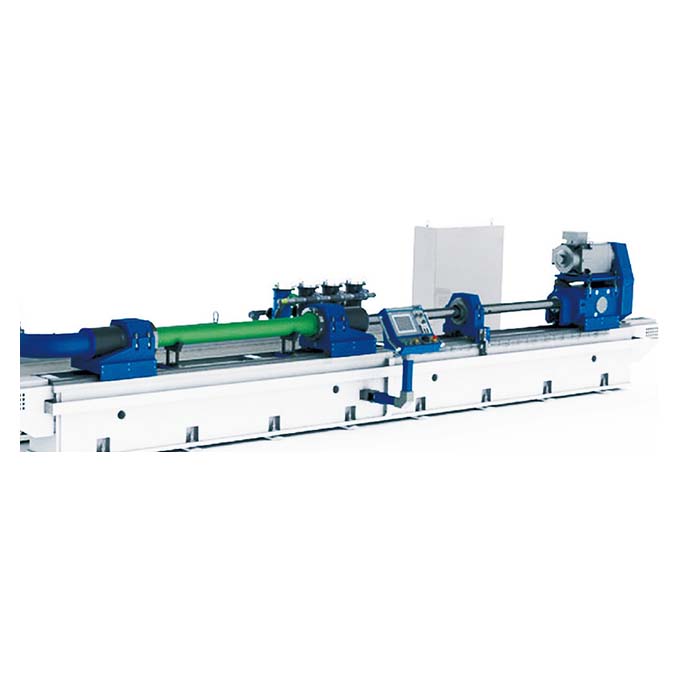
Long Hole Drilling Machine Hand-scraping the mating surfaces of a CNC machine tool’s motion system offers myriad advantages.