Machine vision systems are employed across a wide variety of industries for tasks such as quality inspection, optical character recognition and measurement gauging. Many of these tasks and others are used in applications including manufacturing; autonomous or self-driving vehicles such as cars, agriculture equipment, and unmanned aerial vehicles (UAVs); and inspecting semiconductors, flat panel displays, and labels. The vision systems used for these applications rely on robust imaging lenses for the accurate, reliable and repeatable capture of visual information. However, the standard or base tier imaging lens models that are highly flexible in design feature more fragile moving parts and potential failure points when subjected to more harsh environments. These environments may expose systems to repeated acceleration, also known as shock, or water in the form of submersion or high-temperature, high-pressure jet spray. Ruggedized lenses address these sensitivities with streamlined design and durability-enhancing features.
Industrial ruggedized lenses are machine vision lenses that feature streamlined designs with fewer dynamic components. These lenses are designed and manufactured to take up less space and contribute less weight to an imaging system operating consistently at specific conditions such as F-number, working distance or illumination wavelength. Fewer complex, movable parts also means that these lenses feature an excellent cost-to-performance ratio making them an ideal choice for OEM device integration or for applications that require lenses at high volumes. Waterproof Lenses
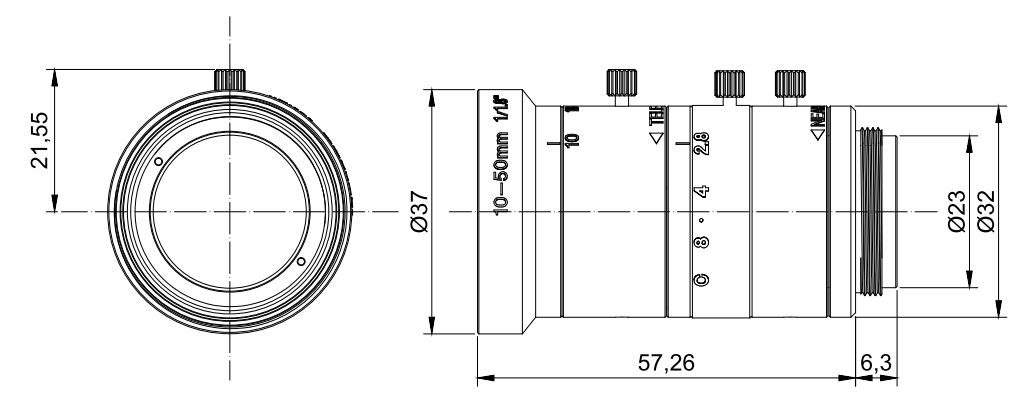
Stabilized ruggedization protects lenses from the harmful effects of shock and vibration. Standard imaging lenses subjected to these environments can fail in several key ways. Besides movable internal components breaking and becoming inoperable, lenses can fail when shock decenters or rotates lens elements within an optical design. Shifts in the nominal placement of optical elements contributes to a degradation of the lens’ optical pointing stability, which is defined as the ability for a lens to reliably and repeatably map a set of points from object space to the corresponding points in image space.
A change in optical pointing stability in situ may also be referred to as pixel shift when specifically referring to a condition in which the light rays passing through the lens have shifted so that image features may appear on different pixels than previously.
To remedy optical pointing stability degradation, industrial ruggedized lenses also have their optical elements glued in place to minimize any potential unwanted motion. Additionally, stabilized lenses have a lockable steel ring used to hold the lens in place to prevent changes in focus.
With the additional ruggedization features of a stabilized ruggedization lens, optical pointing stability is ensured to a pixel shift amount smaller than the size of a single sensor pixel. Stabilized ruggedization lenses are excellent for use in high-accuracy measurement applications such as 3D stereo vision, machine vision sensing for robotics and other autonomous vehicles, and motion tracking of moving objects.
Ingress is defined as the act of going inside or entering something. An ingress protected or IP ruggedized imaging lens has its entry points sealed away from water and sometimes also small debris particulates. Ingress protected lenses also have the same mechanical design simplifications as industrial and stabilized imaging lenses due to the susceptible nature of complex movable components to water. Per IEC 60068 and 60529 standards, ingress protection is not a one-size-fits-all designation. Components protected from ingress have a two-character code designation. The first character designates how much if any protection the component has from solid particles and may be a number from 0 to 6 or an X indicating that the component was not tested for this type of ingress.
The second character designates protection from water ingress and may also be an X or a number ranging from 0 to 9 with the option for an additional qualifying character suffix for more specificity. Additionally, many products may feature multiple IP designations due to the particular nature of the water used for testing (static submersion versus high-temperature, high-pressure jets). For example, a lens may be rated IPX7 and IPX9K. IPX7 indicates that a lens may be submerged in a depth of one meter of water for up to 30 minutes and IPX8 indicates the same depth of water but for a duration of one hour. IPX9K indicates that a lens has protection from high-temperature, high-pressure water jets.
Ingress protected lenses are sealed from water typically with the use of O-ring seals and occasionally RTV silicone as well and may feature hydrophobic coating technologies to prevent the buildup of water droplets, which have the potential to interfere with the optical design of the lens when on optically active surfaces.
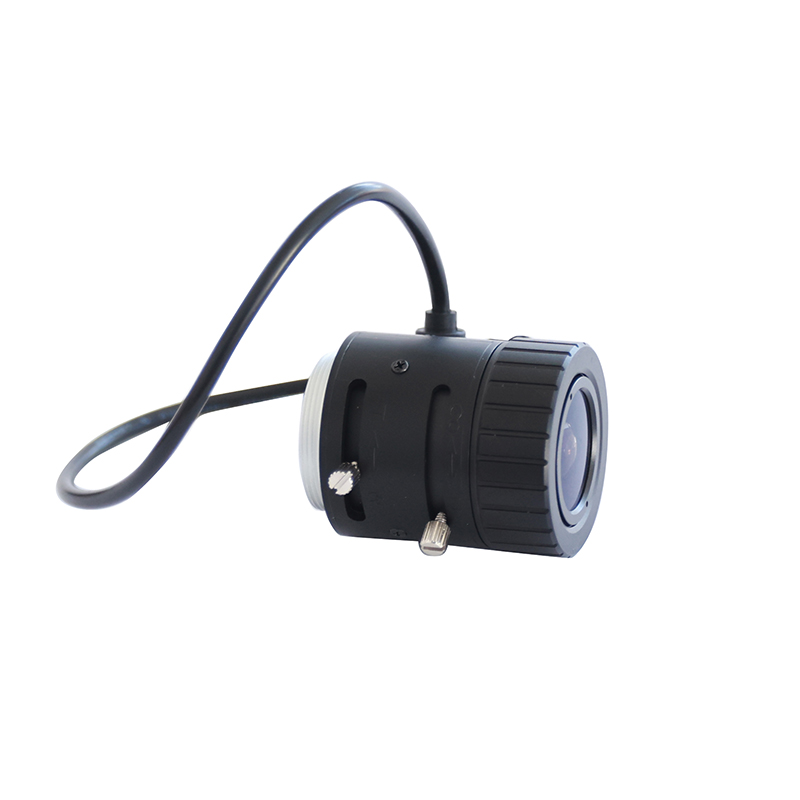
Narrow View Angle Lens Lenses can be ruggedized for many different extreme environments, many of which are not covered in this work or offered as off-the-shelf solutions. For example, two environmental factors not mentioned are temperature and pressure. However, full custom imaging lenses can be designed and manufactured to withstand a wide array of extreme conditions. For this reason, it is crucial to understand the specific demands of the environment in which an application is to be deployed. As ruggedized performance specifications increase in magnitude or if products require multiple types of ruggedization, the price for a solution will also increase. However, lens manufacturers should be able to provide end users with performance specification documentation such as modulation transfer function (MTF) curves and other literature. Manufacturers should also be able to explain how these metrics will inform the outcomes of integrating products into an application. Novel applications that require different types of robust vision systems appear in industry often, so it is critical to understand application requirements to be confident that a specialized product will necessarily perform without fail.