Located on the east bank of the Mississippi River, River City Landscape Supply, Inc., with its mountains of rock, sand and gravel, presents a strange dichotomy to an unsuspecting visitor. A walk among the looming mounds makes you think of some northern desert, particularly when the 30-deg-F wind is blowing 40 miles/hr, and the air is filling with flying particles, as it was during PD's visit. Yet, as you pass between the mounds, you get sudden glimpses of the Arch and the gleaming buildings of downtown St. Louis on the other side of the river.
Hf/f/s machine runs prefolded film from a roll. Parallel, continuous belts pull the film through the machine. Sequence of operation includes side-sealing, filling and top-sealing. Volumetric Filling Machine
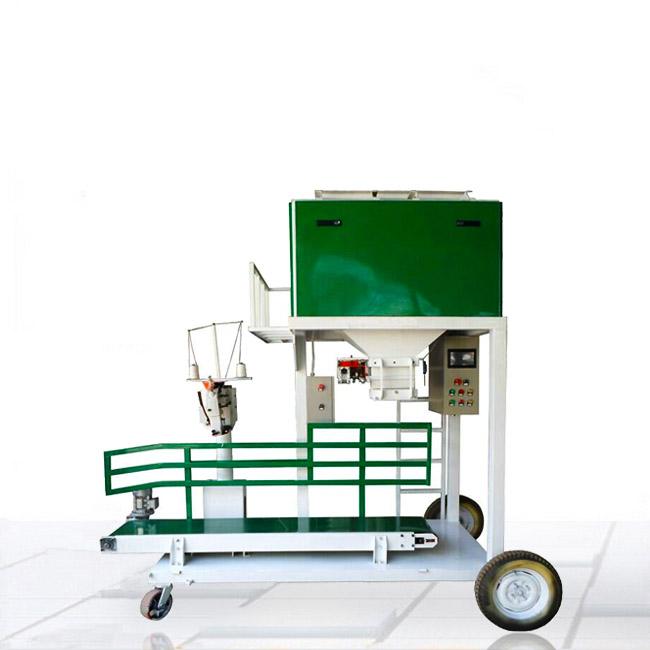
River City Landscape of Sauget, IL, packages a wide variety of landscaping materials, including sand, rock, gravel, mulch and other items in 0.5- to 3-cu-ft plastic bags. It is a major supplier to Wal-Mart, Kmart, Ace Hardware and other large retailers. Founded 12 years ago, the company has progressed from manual operations to two mechanical systems using Hamer Model 2040 horizontal form/fill/seal machines equipped with scales from Inglett & Co. (now Fischbein-Inglett Co.), PASCO palletizers and stretch wrappers from Orion Packaging Systems.
River City Landscape installed its third packaging line a little more than a year ago using equipment from the same manufacturers. "These landscaping materials are abrasive and hard on machinery, particularly the fillers, so it takes rugged equipment to handle them," says plant manager Gary Phillips. "After we installed the first two lines, I worked with Hamer to redesign the filler jaws and make some other changes, and the new line is doing a great job for us." Compared to the previous manual operation, which required six people to produce 3,500 bags in an eight-hour shift, the new line produces 6,000 bags/shift with only two people. Line speed depends on the product being run. For example, the new line runs 24 bags of sand, or 18 bags of lava/min.
Polyethylene bag film, which contains 2-percent UV inhibitor to minimize degradation by the sun, is supplied by De Elliotte Co., Inc. The film, which is 3.5- to 4-mil thick, depending on the product being run, is flexo-printed in four or five colors, and is folded at the bottom before it is put on the roll. Thus, the filler only needs to seal the sides and top.
F/f/s machine features heavy-duty scale system The new line starts with a Hamer Model 2080 hf/f/s machine, which is more sophisticated than the Model 2040 machines on the other lines. The roll of film is mounted on a vertical shaft at the end of the machine, and parallel continuous belts that compress the top edges pull the film through dancer rolls that maintain the proper tension. Machine operation is intermittent through the filling step, after which it switches to continuous operation. The drive motor on the machine runs continuously, but a pneumatic clutch/break system starts and stops the pull-belts during the intermittent portion. An embossing-type code dater and a gusset former are located at the entrance to the machine.
The film then passes through a unit that punches two rows of vent holes just beneath the top-seal area. "This releases air that enters the bags during sealing. Otherwise, they'd look like pillows," says Phillips. The bags continue to the side-sealing station, where a high-temperature element in the center of the heated vertical sealing jaws melts the film in the seal area to separate the bags. After side sealing, the bag moves beneath the filling chute. The pulling belts open at this point, and pneumatically operated jaws pull the top of the bag open. This triggers the scale hopper to open and discharge the product.
An inclined conveyor carries product up to the feed hopper of the Fischbein-Inglett CV100 heavy-duty scale on the top of the hf/f/s machine. This scale is specifically designed to handle these heavy, abrasive products. At the beginning of each weigh cycle, a vibrating pan carries product to the weigh scale until the correct weight of product is present. At that point, the infeed stops, and the scale waits for the signal to discharge. The next weighing cycle begins as soon as the scale discharges.
Wide bottom belts installed at an angle form a trough to support the bottoms of the bags leaving the hf/f/s machine, top. Bags pass beneath a roll that squeezes air out of them, middle. Bags are then stacked eight to 15 layers high on pallets, depending on product.
The machine is equipped with a settler that bounces the bag up and down as it is filled to ensure the product settles in the bag. This is only used when running light, fluffy products such as mulch. After filling, the top of the bag is again grasped by the parallel belts, which immediately carry it into a set of wide bottom belts installed at an angle to form a trough to support the bottom of the bags. From here on, the bags are conveyed continuously rather than intermittently.
The bags pass through a top-sealing station where the film is heated by 400-deg-F air, followed by knurled steel rollers that mash the top edges together to make the seal. Jets blow ambient air on the top of the bag to cool the seal area. An angled bar at the discharge of the conveyor ensures that all of the bags fall in the same direction as they enter the palletizer–a requirement for proper palletization.
The filler has digital controls for the side-seal temperatures, and an operator screen where operating parameters, such as side-seal dwell time and cycle time, can be input and where machine diagnostics can be displayed. A photoeye located near the front of the machine looks for the eye mark on each bag to time each machine cycle.
High-level palletizer The bags leaving the hf/f/s machine pass beneath a roller that squeezes the air out and then travel up an inclined conveyor to the high-level palletizer. Bags on each consecutive layer on a pallet must be aligned properly to form the interlocking pattern that keeps them in place. Thus, as the bags enter the PASCO palletizer, they pass through a device that turns them as required. This consists of two parallel plates on a vertical shaft. The plates clamp onto the long sides of the bags, and the shaft turns 90 or 180 degrees to align the bags. The bags then enter a section where they are pushed at a right angle onto a split assembly plate. When the correct number of bags is assembled in the correct pattern, the plate separates in the center, and the bags drop gently to form the next layer on the pallet. Vertical walls on each side keep the bags in place as the plate opens.
Empty pallets are stacked in a magazine on the lower level of the machine. When a new pallet is required, clamps grip the pallet second from the bottom and lift the stack off the bottom pallet, which is pushed onto an elevator that raises it to the upper loading position. River City Landscaping runs eight to 15 layers on a pallet, depending on the product, and each layer has five or seven bags. The palletizer is PLC-controlled with an operator panel to input and receive data. Operations for different products, including speeds and pallet patterns, can be selected from the screen.
When the pallet is full, it discharges from the palletizer and is conveyed to a stretch wrapper from Orion Packaging Systems. The wrapped pallets are stored outside to await shipment.
Hf/f/s machines: Hamer, Inc., 952/927-4678. Circle No. 212.
Scales: Fischbein-Inglett Co., 706/736-1488.Circle No.213.
Palletizers: PASCO, 800/489-3300. Circle No. 214.
Stretch wrappers: Orion Packaging Systems, 901/366-4170. Circle No. 215.
Film: De Elliotte Co., Inc.,913/764-0606. Circle No. 216.
Medical Test Kits Find a New Home
Recycling in an MRF Minute: $50 Million Plus Benefits
Bridge Collapse Triggers Supply Chain Warnings
Best in New Food and Beverage Packaging
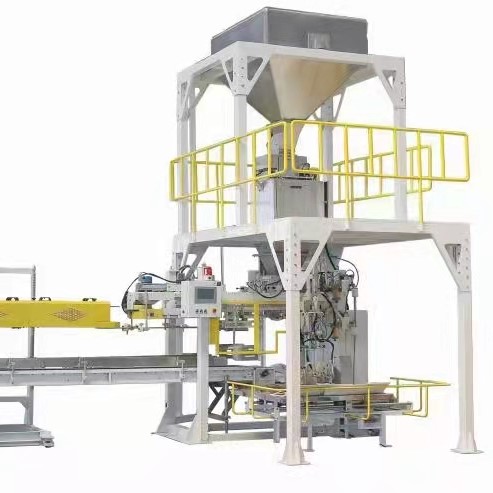
Big Bag Quantitative Packing Machine Copyright © 2024 All rights reserved. Informa Markets, a trading division of Informa PLC.