I saw so much at the MADE show these past few days. And it was… honestly, it was a bit overwhelming (in a good, bike nerd kinda way). For this story, I will get right to the gist of it. I ran into Charlie Murray, the man behind Heavy Bikes, early on in the show. When I saw the bike that was on display, I was pretty skeptical.
But, after talking with Charlie, it was clear that he was on to something. And his enthusiasm and genuine stoke about it was contagious. So, let’s talk about the bike. Jerrycan Blow Mould
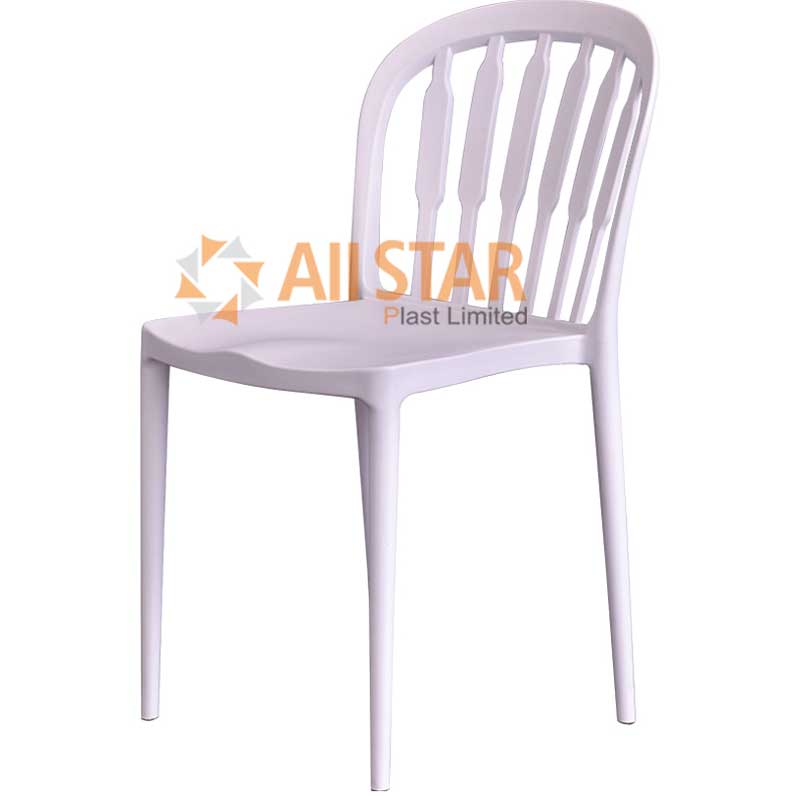
Heavy Bikes utilizes Foundry Casting System’s ‘Pascal Process’ for the pressurized solidification of sand casted parts. They start the process with a custom bike fit. That fit drives a 3D-printed sand mold design. The mold is then filled with molten A356 aluminum.
Heavy Bikes says that “the pressurized solidification ensures a properly filled part with enhanced mechanical properties“. Then, they bust open the frame mold with a sledgehammer before going off to heat treating.
Heavy then machines the interface and “art surfaces” after heat treating the frame. Charlie told me that the dimples that are on the show bike are just there to show the kind of details that can be accomplished with the casting technique.
Heavy Bikes says that they “built the Hypocrite to explore the limits of thin wall casting while adding compliance to a single-piece bike frame“.
On their website, they describe the Hypocrite’s ride as “one of a new sense of momentum not found on hollow tubular bikes“. This, paired with the bike’s nimble wheelbase, provides a connected feel unique to Heavy Bikes.
According to Charlie, they can “get the Hypocrite frame at the show, inside of 6lbs based on a rider’s measurements of 6′ with a 32″ inseam”.
Ron Frazelle is the Cycling Lifestyle Editor for Bikerumor, he has been writing about bicycles and the cycling way of life for 7+ years. Prior to Bikerumor, he worked in the bicycle industry, living and breathing bicycles since 1995. He is based in Anaheim, California, Frazelle is an avid cyclist of all disciplines, camper, father to 6 children, husband, musician and self-proclaimed retro-grouch.
This site uses Akismet to reduce spam. Learn how your comment data is processed.
Did you not have the audacity to ask what the bike weighs? When the brand is called “Heavy” and they are trying to sell the extra momentum, I’m guessing it is not light.
This process does sound awesome. I would love to design my own cast frame.
Hey Jason, I just asked Charlie and I’ve updated the article at the bottom. Thanks for reading!
The CW article about this bike at the MADE show said this bike frame cost $16,000 to make. $16,000! Now you are saying they told you the frame alone in the equivalent of a size M/ML would weigh about 6 lbs. 6lbs!
Is this like some type of really, really early April 1, 2024 joke?
6 lbs for a size M/ML frame and a cost of $16,000?
Do any of these guys have even the slightest comprehension regarding the relative cost of other goods? My brand new Kawasaki Ninja 650 motorbike was $7,000 out the dealer door including sales tax this past year. $7K out the door for a brand new street motorcycle! And they are putting out there the idea of a 6 pound size M/ML nonpowered bicycle frame with a cost of $16,000? Really?
I knew the bicycle industry had lost its collective mind when they started selling cheaply fabricated Chinese mainland made CF cookie cutter frameset bikes for the price you could buy some entry level brand new motorized cars for and certainly a load of very, very good lightly used cars as well. But this takes the recent bicycle industry Tulipmania pricing phase concepts to a whole new level.
I mean seriously, what is going to come next – a 5 pound 3D printed saddle being sold for $2,000 US? This is not helpful to the bike industry or helping to promote cycling in general. This is promoting utter nonsense and nothing more.
They said it cost $16,000 to make not that it would retail for that. And given this is a first go with new tech the fact it’s only 6lbs is pretty impressive.
Yes, and I’m fairly certain I said “cost” not “retail” above several times. If it costs $16,000 to make it is a pretty safe assumption it would retail for more than that unless you think they’ll operate their business by selling bikes below cost.
If you find a 6lb frame in a M/ML size “pretty impressive” at a cost of $16K when even mid level steel frames at the present can easily be made multiple pounds less than that weight and CF can build into frames at less than 1/3rd that weight at less than 1/4 the cost I’ll agree to completely disagree with you on that observation. LOL
I guess $16k was a cost to manufacture the first unit so including all overhead costs so it does not mean that every next unit would cost as much.
Pretty high tooling costs for something that uses very little fixed tooling to make. 3d printed lost wax for the mold which is then sand cast. No molds necessary. Some fixturing for machining afterwards for sure. This is an ultra low fixed cost bike- assuming the printer and sand casting unit are not owned by the bike brand (not likely, or those machines are owned by another part of the bike brand’s business). This manufacturing process would (MAYBE) make sense for a high volume low performance bike, like a bike share program bike, but even then it is possible to design hollow tube bikes that can be robot welded and give all the weight and performance gains that hollow tubes entail. There is a reason the bike industry went to hollow tubes well over 100 years ago!
Anyway, there isn’t much to say about this bike that the market won’t tell it.
the first iphone cost 150million
You can be sure every major manufacturer’s carbon bikes would cost much more than that if they only made one of them…
You realize 6lbs is just the frame, right? What exactly does this expensive technology accomplish, aside from advanced wallet extraction?
Proof of concept, that is what it establishes. The cost of 3d printed parts is still very high. But this method may provide a level of precision builders are looking for on scale. May, I am not holding my breath. However, progress is progress. Providing and refining different manufacturing methods keeps us moving.
Complete bike start at $16,000 for the bike as displayed at the show. This includes the custom fit and the ability to customize the frame and cutouts with art to the rider’s preference and design. A bespoke bike is a piece of rideable art therefore it should not be compared to a high volume motorcycle produced by a major manufacturer.
I think the innovation from that prospective is turn around time. I don’t think we can argue the nature of being “Bespoke” as no know has review the ride quality. The shape/structures chosen for their proof of concept don’t look very compliant. I would guess the ride is pretty harsh.
Heavy is the new light.
Hey man, $7k otd is a great price for a new Ninja 650. Enjoy it!
Buuuuuuut, you are comparing a basic entry level street bike with relatively old technology to a bespoke handmade bicycle with brand new technology. Hardly a comparison. A Ninja 650 is comparable to a “Canyon Grizl AL” in the bike world, which is currently on sale for $1599. Still cheap, but about 1/4 the price of a motorcycle.
They got ripped off if it actually cost $16k to make. I’ve had a few prototype one-off aluminum parts made the same way with the same alloys. About 5 pounds each with similar small details. Some precise machining but only one machining setup. Cost was $2-3k each.
I agree, stupid brand name. There are so many out there: “Hotpoint” refrigerators, “Coldspot” stoves, a local company named “Moist” a word that repels 50% of the population. I just bought a replacement battery, by the company “Puredick.” The trademark is registered, I checked.
Cool looking bike to demonstrate their capabilities, but where do the bottle cages mount? And why don’t they have their own brand of frame bags?
We have frame bags from Rogue Panda designed – an example was on the other bike at the show.
Simply ran out of time in machining to add the King Cage bottle cages. We’ll get them added and post the update this weekend on our Instagram @heavy__bikes
I’m wondering it they could use the ‘Lost foam casting’ that General Motors used to cast the Saturn engine blocks and transmission housing back in the 90’s. You basically injection mold the item in styrofoam, encase it in plaster, melt out the stryofoam and then inject molten aluminum. You would have a smoother finish, and possibly a thinner wall construction.
Lost foam is possible but if you ask around GM it’s a not a technique they like to remember. Mercury Marine utilizes lost foam to great result for their engine blocks. We’re exploring other molding techniques like the AMEC process from Skuld. For now we utilize 3D printed sand for each mold specific to the rider’s desired geometry, ride style and gear.
That casting was infamous for porosity. This is why modern manufacturing is high pressure die casting like Gigapress, but owners are already reporting cracks in those castings.
So a steel gravel frame – my medium Ritchey Outback for example – weighs 2175 grams or 4.78 lb. They could probably get their frame down to a competitive weight. That frame would be a bitch to clean when it’s dirty.
We’re on track to get the Hypocrite down below 5.5lbs however it becomes a race to the bottom where carbon wins. Our goal is to offer a more confidence inspiring ride to a wider audience and aim to build bikes for more challenging requirements, faster.
Or just weld alloy tubing for even less weight and cost. Why does this industry insist on so much BS marketing.
Its not an industry. Its a guy trying something cool. Calm down.
i had a kirk precision magnesium cast bike – very cool design – TERRIBLE bike – that frame flexed like hell – and surely wasnt light
The Kirk Precision story is full of dynamic challenges staring with magnesium. Aluminum is much more forgiving and won’t burn down your building.
That’s one of the foundational problems with these type of solid alloy structure bike designs. They lack the ability of a thin walled tube at increasing diameters to provide sufficiently stiff structures that can resist lateral and torsional forces at a relatively low weight. Because the frame structure is solid and not connected tubes you are forced to use a lot of material to get any decent type of stiffness of those solid structures to resist the lateral and torsional forces a typical bike frame encounters during a ride. That’s why I’m skeptical they could ever get the weight down to any respectable weight without the bike riding like a wet noodle. And I doubt they can ever get the cost of these bikes down that much off the reported $16K cost they stated. Casting might be an excellent app for a golf club head, but I don’t see it being a great choice for a bicycle frame. Just MO.
People have such short memories. This is a bargain to some other experiments. I remind you of American Bicycles Beryllium MTB, in 1993 it was a $36,000. that’s like $76k in todays money!
Beryllium is extremely toxic, that’s why it costs so much to produce one. This aluminum thingy though…
That’s why my ping i2 beryllium golf clubs are no longer made. I love those, despite them being 30+ years old!
As far as ‘April Fools’ bikes go, at least this one looks interesting. The TV program, ‘Myth Busters’ showed dimples, like on golf balls, improve aerodynamics and fuel efficiency when they dimpled a car. This bike is overweight. Heavy Co may have better luck with a fancy cruiser design if the price is reasonable. Some things are just not feasible to produce. Maybe they can weld their front to a tubular rear to give this thing a diet.
This is a great article. Innovation starts with a lot of pessimism. It will be interesting to see what comes of it.
They were doing this in 1893
That’s a nice build kit. But it’s how you’d spec an $8k bike. Not a $16k bike.
“Art bikes” are great and all, but this ain’t that.
People with short memories don’t know these cast frames and carbon/alloy frames people are freaking out over have been tried so many times in the past and there’s a bunch of reasons none of them succeeded…
Great article Sir. I am very interested in the evolution and future of Heavy_Bikes. Very Cool Ron.
That Frame is one huge inclusion failure waiting to happen.
This metal alloy makes a bike comeback in various guises/forms, then quickly disappears, being the wholly impractical material it is for the purposes of a bicycle frames … yawn
Only those loaded with too much cash, and little sense, would waste coin on this idiocy.
A O.2% percent improvement doesn’t sound like much, but apparently it is when you’re talking about aerodynamics.
Rockshox goes for the long haul with new Flight Attendant trail and enduro forks and shocks for longer travel bikes.
DT Swiss unveils all-new lightweight 1200-series carbon MTB wheels built on new manufacturing tech to make them lighter & tougher, from XC to Enduro, even eMTB…
Fizik finally did it. Partnered with GebioMized, Fizik One-To-One Adaptive brings full custom 3D-printed saddles to all cyclists…
Curious Creatures expands men’s line with riding gear that is built different.
Donate to help build trails in the Lost Sierra and win a bad ass bicycle for doing it!
Going big or going fast? The Smith Payroll helmet is certified to take the hit.
Raw carbon or full paint? The new Team 31 Ibis Exie USA gives paint fans a choice.
Sign up to receive BikeRumor content direct to your inbox.

Motorcycle Candy Molds Sign up to receive BikeRumor content direct to your inbox.