Citation numbers are available from Dimensions
Central Glass and Ceramic Research Institute (CSIR), India Metal Zips Uk
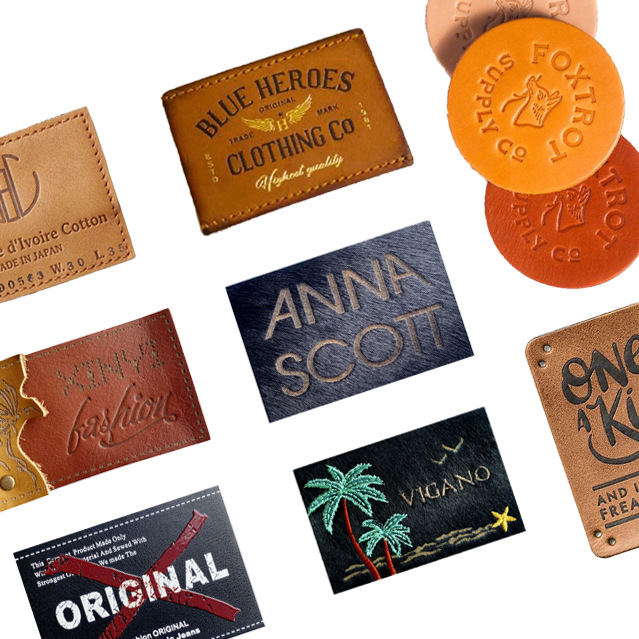
Polytechnic Institute of Leiria, Portugal
The adhesion in 3D-printed composites between dissimilar layers was investigated in response to demand for multimaterial prints. We report the qualitative and quantitative adhesion properties between commonly-printed materials, acrylonitrile butadiene styrene (ABS) or acrylonitrile styrene acrylate (ASA), and flexible TPU. ASTM D1002/D3164 lap shear adhesion tests were performed to measure the adhesion strength between the acrylonitrile plastics and TPU, finding values of 4.7 MPa between ABS and TPU and 6.4 MPa between ASA and TPU. These values are on the same order of magnitude of reported commercial adhesives, suggesting that multimaterial 3D printing can provide an automated, industrially-relevant alternative to handmade fabrication. SEM images are reported to show the quality of adhesion between materials in the composites. These images expose qualitative differences in the interlayer adhesion between materials in the composites that depend on the order of printing. Thermal (DSC and TGA) and rheological characterizations were performed to investigate the processing conditions of the extruded plastics while they are in their melt states. The role of viscosity is shown to have major implications on the adhesion, as materials with lower viscosities displayed improved filling of the interlayer voids and increased strength of adhesion.
Advanced fused filament fabrication (FFF) printers have improved technologies that allow for multiple materials to be printed in a single printing process. With this capability the addition of a low modulus filament, such as thermal polyurethanes (TPUs), could open opportunities to develop many new composites, including 3D-printed functionally-graded composite materials (FGCMs). These graded composites could be printed in a number of ways, including being printed layer by layer in a stepwise composite structure (Udupa et al., 2014). However, layering of the two different materials will form interfaces between dissimilar chemistries that can have significant effects on the overall properties of the printed part, especially the mechanical strength.
As the use of TPU is relatively new to 3D printing (Bates et al., 2016), little information is currently known of the capabilities or limitations. For instance, by examining the thermal properties that are necessary for printability of TPU, we have shown that materials with complex architectures require both thermal and rheological characterization to fully optimize their spectrum of print profiles for 3D printing (unpublished). However, the ability of TPU to coexist in a single print with more traditional thermoplastics (e.g., ABS) needs to be explored for multimaterial 3D printing to be viable. Assuming that TPU will wet the surface of the other filament, TPU's low modulus was hypothesized to create greater interlayer adhesion with a reduced chance of curling or disbonding during a print. For this work we investigated the strength of this adhesion between TPU and standard materials in FFF, as strong adhesion should provide an opportunity to directly bond TPU to traditional materials in FFF printing. We utilized the lap shear joint adhesive strength test as our primary method of comparison.
The plastics that were investigated were acrylonitrile butadiene styrene (ABS), acrylonitrile styrene acrylate (ASA), and thermoplastic polyurethane (TPU). ABS and ASA, obtained from 3DXtech (Byron Center, Michigan, USA), are both amorphous polymers that are commonly used in FFF. TPU, NinjaTek Cheetah™ (Manheim, Pennsylvania, USA), is semi-crystalline with a shore hardness of 95A, providing the potential for additional bonding mechanisms (Kishore et al., 2016). All filaments had nominal diameters of 2.85 mm.
All 3D-printed parts were built using an A4v3 FFF printer from 3ntr (Oleggio, Italy). Print or nozzle temperatures are provided in Table 1, while the chamber temperature and the bed temperature were 70 and 110°C, respectively. Printed parts were developed layer by layer at a thickness of h = 0.2 mmperlayer. Raster orientation was defined by printer specifications at angles of ±45°. The amount of infill that was used for all prints was set at 100%. The skin overlap was set at 1, which indicates full overlap between the outer perimeter and the infill. G-code for each trial was generated using KISSlicer software, and printing was initiated with Repetier Server Pro. During initial testing substantial adhesion both between TPU and ABS and between TPU and ASA was observed to form without any applied pressure or additional heating. Thus, no further processing or post-processing was completed on any of the samples except where otherwise specified.
Table 1. Print profiles and thermal characteristics of printing materials.
All tests of adhesion strength using lap shear joints were performed on a 5960 Dual-Column Mechanical Testing Machine from Instron (Norwood, Massachusetts, USA) with wedge action grips. Lap shear tests were designed based on ASTM D1002/D3164 with a width of each sample of w = 25.4 mm (Figure 1). As recommended by ASTM D1002, the thickness of the substrate was set to t = 1.62 mm when TPU was used as the adhesive layer. To ensure that the substrate would not fail before disbonding, the thickness was set to t = 3.00 mm when ABS and ASA were used as the adhesive layer. The measured substrate thicknesses after printing are reported in Table 2. The thickness of the adhesive at the joint was designed to be a single layer thick, such that h = 0.2 mm. The overlap length was adjusted to ensure a successful disbonding at the joint. The overlap length was tested initially at ℓ = 5 mm, based on ASTM D1002 recommendations. If more than two replicates were unsuccessfully disbonded (i.e., the substrate was broken) for a configuration, the overlap length was reduced by increments of 1 mm until the lap shear tests were successful for four or more replicates. Final values for each configuration are shown in Table 2. The extensional pull velocity was set at u = 1.3 mm/min. The temperature for these measurements are ambient room temperature (T = 20°C).
Figure 1. Dimensions of the geometry that is used for the lap shear joint adhesive strength test follow ASTM D1002/D3164.
Scanning electron microscopy (SEM) was performed with a FEI Quanta 600 SEM (Thermo Fisher, Waltham, Massachusetts, USA) for composites of ABS / TPU / ABS and ASA / TPU / ASA. Rectangular composite bars were 3D-printed as a representative lap joint, each consisting of a three-layer sandwich structure with ABS or ASA on the outer layers and TPU on the inside. Each of the three material layers was 0.6 mm in thickness, yielding an overall bar thickness of 1.8 mm. To examine the cross-sectional area of the composites, the bars were dipped into liquid nitrogen for 10 s and then broke into pieces that were 5 mm in length. These pieces were then mounted onto aluminum SEM mounts and sputter coated with palladium-gold.
Thermal properties of the 3D-printing materials (as received filament) were determined using a Q2000 Differential Scanning Calorimeter (DSC) and a Q500 Thermogravimetric Analyzer (TGA), both from TA Instruments (New Castle, Delaware, USA). DSC provided glass-transition and melt temperatures. DSC measurements were run from T = –50 to 300°C at heating rates of dTdt=10 to 20 C∘min. Two heating and cooling passes were made for each sample. TGA measurements were made by heating 15 to 20 mg of material from 25 to 600°C.
All rheological measurements were completed with standard rotational rheometry using a AR2000ex (TA Instruments, New Castle, Delaware, USA) with an environmental test chamber (ETC). Disks were 3D printed to 25 mm in diameter and 1.5 mm in thickness. Using disposable aluminum plates that were 25 mm in diameter for the upper and lower geometries, the ETC temperature was set to the specific processing temperature at the nozzle that is used by the 3D printer (Table 1). A frequency sweep at a strain of γ0 = 0.01 for frequencies of f ∈ [0.01, 10.0] Hz was used to determine the complex moduli of each sample.
Adhesive strengths or apparent shear strengths were tested using a single lap joint (lap shear) specimen to determine the strength of adhesion between materials. Further, we report the interlayer adhesive strength for ABS and ASA using the same material as the adhesive, noting that these cohesive disbonding failures resulted from cooling of the material between each individual pass of the printer. Adhesive strengths (σmax) were determined by taking the ratio of the maximum force (Fmax) that was required to cause failure in the joint,
such that w is the width, and ℓ is the overlap length. Figure 2A presents the raw force-extension curve for a single lap shear test for the adhesion of TPU between two substrates of ABS (ABS / TPU / ABS). The point at which the force dropped significantly correlated with the disbonding of the sample, as confirmed via visual inspection, and the maximum force was obtained at this point. At short times that corresponded to small deformations during the extension, the adhesive material underwent linear shear deformation that was completely recoverable (as an example see the red region in Figure 2A; ΔzL ∈ [0, 1.03], mm). Assuming that the substrates exhibited negligible deformation, an estimate of the shear modulus (G) of the adhesive in the joint was obtained from this region by
where FL is the linear force that occurs over displacement ΔzL, and h is the layer thickness. Since ASA / ASA / ASA experienced observable stress-whitening that resulted in an initially non-linear force-extension curve (Bucknall and Smith, 1965), we consistently used the displacement at one half of the maximum force, FL=Fmax2. Note that the apparent shear rate (γ˙) for these trials can be calculated from the ratio of extensional pull velocity to the overall layer thickness to be γ˙=uh=0.1 1s. These values confirm that, at room temperature, TPU is at least four-times lower in shear modulus than ABS or ASA.
Figure 2. Experimental lap shear results. (A) Load F vs. extension Δz. The maximum point represents the maximum force that is required to disbond the lap shear. The red highlighted section of the data (ΔzL ∈ [0, 1.03], mm) represents the linear region of the force-extension curve. An associated shear modulus G is also provided. (B) Adhesive strength for configurations. Adhesive strength of Loctite® U-05FLTM Hysol® is given for comparison1. Error bars represent standard deviation over multiple trials (n = 4). Lap shear designs are indicated in the graph by the upper substrate (blue), the joint (red), and the lower substrate (blue).
Figure 2B shows the average adhesive strength between the composites for each configuration (n = 4). The configuration refers to the layer arrangement between the different plastics. Within Figure 2B the layer arrangement is shown based on the 2D image of a lap shear with substrates colored in blue and the joint colored in red. Each bar graph corresponds to a different configuration, indicated by the blue (top and bottom) text corresponding to the substate and the red (middle) text corresponding to the joint. Lap shears of the same plastics exhibited greater interlayer adhesive strengths than lap shears with TPU. Composites that were made with ASA and TPU demonstrated statistically stronger adhesive strengths than composites that were made with ABS and TPU. Published data on the strength of a commercial polyurethane adhesive, Loctite® U-05FL™ Hysol®1, is presented for comparison. In that study, Locitite U-05FL adhesion strengths were characterized using ASTM D4501 tests (ASTM D4501, 2014). Overall, the 3D-printed TPU showed comparable adhesive strengths to the commercial adhesive. The adhesive strength between 3D-printed ABS and TPU was 15% greater than the reported strength of the commercial adhesive, while the adhesive strength between 3D-printed ASA and TPU was 3% less. During the lap shear tests one common observation was that, for all lap shear specimens that were printed with ABS or ASA substrates and a TPU (bonded) joint, the TPU disbonded from the top substrate, with regards to the layer-by-layer printing. Thus, TPU appeared to adhere better to the bottom substrate, which prompted further investigation.
Rheological characterization and electron microscopy were used to access the effect of print order on adhesion. The rheological properties of ABS, ASA, and TPU were examined at their defined print temperatures of 240, 240, and 218°C, respectively (Table 1). Elastic (G′) and viscous (G″) moduli of each plastic was acquired over a frequency range of f ∈ [0.01, 10.0]Hz (Figure 3A). Complex viscosity, which can be found from |G⋆| = 2πf|η⋆| where G⋆ = G′ + iG′′, is also shown for comparison (Figure 3B).
Figure 3. Rheological characterization. (A) Moduli [Pa] vs. frequency [Hz]. The moduli of TPU at its print temperature are significantly lower than the moduli of both ABS and ASA. (B) Complex viscosity [Pa·s] vs. frequency [Hz]. The viscosity of TPU at its print temperature is significantly lower than the viscosity of ABS or ASA at each specific print temperature. This behavior reveals that TPU can flow much more easily than either acrylonitrile plastic during print.
Evaluation of this data revealed that TPU had a much lower complex viscosity (and moduli) at its print temperature than ABS and ASA. The difference in viscosity gives evidence that TPU can flow much easier than either of the acrylonitrile plastics during a print. This behavior would allow TPU to settle more easily into the grooves of ABS or ASA, meaning that if TPU were printed onto ABS or ASA, the adhesion would be inherently stronger than if ABS or ASA were to be printed onto TPU.
To examine this idea more closely, SEM was used to look at the cross-section of a composite that was made of ABS or ASA on the outside with TPU in the middle (Figure 4). The SEM data revealed that TPU indeed settled much more than the other thermoplastics. All images showed that the layer between ABS or ASA and TPU on the bottom adhesion layer were flush and coexisted with one another much more smoothly than the top adhesion layer did, creating a larger effective bonding surface. The top adhesion layer had a smooth layer of TPU with filament-like strands of ABS or ASA sitting on top. The air gaps that can be seen between the extruded top layers reveal weaknesses between the top adhesion layer and TPU. Thus, TPU appeared to adhere much better when it was extruded onto the acrylonitrile plastic rather than when the acrylonitrile plastic was extruded on top of TPU.
Figure 4. SEM images of TPU composites along the cross-section. (A) Composite of ABS / TPU / ABS. (B) Composite of ASA / TPU / ASA. The images reveal a more flush interface for adhesion between the TPU layers and bottom layers, as the bottom interface is coalesced and flush. In turn, the adhesion between the TPU layers and top layers are less than ideal, as the top layer contains holes, which could be a product of higher moduli at print temperatures.
TPU has the ability to adhere to ABS and ASA at strengths that are comparable to commercial adhesives. With the capability to print multiple plastics during a single print, TPU can be confidently incorporated into multimaterial 3D-printed parts that include ABS and ASA. The ability to print both rigid ABS or ASA and soft TPU provides opportunities to expand the versatility of additive manufacturing to areas such as healthcare. Further, users can leverage TPU to immediately adhere parts together without having to remove parts from the bed, allowing the possibility to build more intricate parts that need adhering. Such systems may include items where differences in the coefficient of thermal expansion may resist fractions when cooled or heated significantly.
However, increased adhesion has been shown to be dependent on the print order of the build, and this work should provide guidance to future print parameters when building a multimaterial part. Layer-to-layer adhesion was shown to be affected by the viscosity of the polymers that were printed. Adhesion was increased further when materials with lower viscosity were printed onto materials with higher viscosity, as the lower viscosities provided the capability to infiltrate void spaces, providing additional contact area to increase bond strength.
CH completed the work. NJ initially started the project. WR oversaw the project. TW funded and led the project.
This material is based upon work that was supported by the National Science Foundation under Grant Nos. 1652958 and 1842580.
The authors declare that the research was conducted in the absence of any commercial or financial relationships that could be construed as a potential conflict of interest.
The authors thank 3ntr and Plural AM for assistance with the A4v3. The authors thank Bailey Puetz and Renuka Bhatt for collecting thermal characterization data.
1. ^The Loctite Design Guide for Bonding Plastics, Vol. 6. Available online at: www.ellsworth.com/globalassets/literature-library/manufacturer/henkel-loctite/henkel-loctite-design-guide-plastic-bonding.pdf (accessed Feburary 24, 2018).
ASTM D4501 (2014). Standard Test Method for Shear Strength of Adhesive Bonds Between Rigid Substrates by the Block-Shear Method. Available online at: http://www.astm.org/cgi-bin/resolver.cgi?D4501-01 (accessed December 20, 2018).
Bates, S. R., Farrow, I. R., and Trask, R. S. (2016). 3D printed polyurethane honeycombs for repeated 198 tailored energy absorption. Mater. Design 112, 172–183. doi: 10.1016/j.matdes.2016.08.062
CrossRef Full Text | Google Scholar
Bucknall, C., and Smith, R. (1965). Stress-whitening in high-impact polystyrenes. Polymer 6, 437–446. doi: 10.1016/0032-3861(65)90028-5
CrossRef Full Text | Google Scholar
Kishore, V., Chen, X., Ajinjeru, C., Hassen, A. A., Lindahl, J., Failla, J., et al. (2016). “Additive manufacturing of high performance semicrystalline thermoplastics and their composites,” in Solid Freeform Fabrication Symposium (Oak Ridge, TN).
Udupa, G., Rao, S. S., and Gangadharan, K. (2014). Functionally graded composite materials: an overview. Proced. Mater. Sci. 5, 1291–1299. doi: 10.1016/j.mspro.2014.07.442
CrossRef Full Text | Google Scholar
Keywords: 3D printing, TPU, fused filament fabrication (FFF), additive manufacturing, adhesion strength
Citation: Harris CG, Jursik NJS, Rochefort WE and Walker TW (2019) Additive Manufacturing With Soft TPU – Adhesion Strength in Multimaterial Flexible Joints. Front. Mech. Eng. 5:37. doi: 10.3389/fmech.2019.00037
Received: 14 November 2018; Accepted: 04 February 2019; Published: 03 July 2019.
Copyright © 2019 Harris, Jursik, Rochefort and Walker. This is an open-access article distributed under the terms of the Creative Commons Attribution License (CC BY). The use, distribution or reproduction in other forums is permitted, provided the original author(s) and the copyright owner(s) are credited and that the original publication in this journal is cited, in accordance with accepted academic practice. No use, distribution or reproduction is permitted which does not comply with these terms.
*Correspondence: Travis W. Walker, travis.walker@sdsmt.edu

Cool Zipper Pulls Design and Development of Functional Composite Materials for Digital and Additive Manufacturing