The diesel particulate filter (DPF) has continued to improve over its 15-year existence. So have other components of aftertreatment systems (ATS) that help send cleaner exhaust through the DPF. However, many fleets say problems with DPFs continue to be among their most frustrating.
“The trick to dealing with DPF problems is figuring out how to make sure everything upstream is working within boundaries the DPF can deal with,” said Kevin Otto, a technical consultant to the heavy-duty truck industry. “Everyone in the industry has had issues with DPFs. A lot of it has simply been figuring out how to protect the darn thing.” OEM Emissions Testing
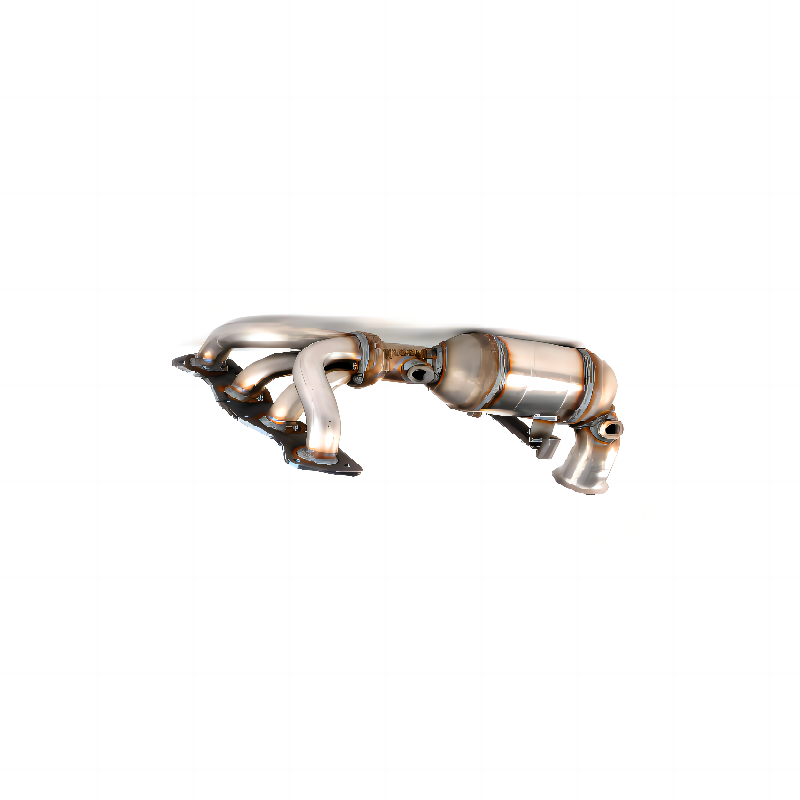
Manufacturers have made significant strides.
“There have been big-time improvements since around 2013,” said Otto, who serves as a technical adviser to the North American Council for Freight Efficiency (NACFE) after retiring from Cummins. “Unless it’s a really severe application, most fleets will tell you that their newer trucks are doing much better than their older ones.”
See also: Dealing with dirty DEF
“When you look at the ATS as a whole, just about every OEM now designs it as a real ‘system’ where the DOC (diesel oxidation catalyst), SCR (selective catalytic reduction), and DPF are all together,” said Chris Hough, vice president of maintenance design and engineering for Penske Truck Leasing, a provider of commercial truck leasing, fleet maintenance, truck rentals, and used truck sales. “No tubing is needed to connect everything. The system has been slimmed down as well, allowing it to maintain heat much better.”
“Detroit has focused on thermal management on both new engine designs, the DD15 Gen 5 and DD13 Gen 5,” said Len Copeland, product marketing manager for Detroit Products, a manufacturer of diesel engines, transmissions, and other products. “Features like thermocoasting and asymmetric injection during driving regens and at idle enable the engine to keep the ATS very warm. This results in efficient regen events and a healthier ATS.”
Additionally, Copeland said the ATS has become better integrated with the engine.
“The Detroit midrange engine lineup, which includes the DD5 and DD8 models, come standard with variable cam phasing (VCP), which has significantly reduced the amount of issues customers experience when operating in midrange applications,” he said. “During low-load or high-idle operation, VCP advances exhaust camshaft timing, opening the exhaust valves earlier in the operating cycle to pass additional heat to the aftertreatment to optimize DPF regeneration.”
The DPF itself also has improved. “Cell thickness and port sizes have gotten better to improve filter flow,” Hough said.
Manufacturers also have gone to designs that are more tolerant of ash. “Some manufacturers have gone to different substrate materials,” Otto explained. “Some DPFs are now made out of a ceramic material called cordierite. Others are made of silicon carbide, which is heavier but also more tolerant of higher temperatures.”
Despite these improvements, fleets still need to understand where their DPF challenges lie—especially mixed fleets with older vehicles.
“A fleet will never get the kind of longevity out of an early aftertreatment system (2007-2015) like it would with today’s systems,” said Bruce Balfour, vice president of CDS (Clean Diesel Specialists), a diesel emissions services company with locations throughout the country. “To achieve the extended cleaning intervals being talked about today, it’s all about the vehicle’s duty cycle and any upstream problems the system has had.”
Resolving upstream issues requires regularly occurring inspections of the aftertreatment system components, including the exhaust gas recirculation (EGR) system. This is especially vital for older vehicles.
“At Cummins, we’d classified EGR as part of the air-handling intake system, which includes the EGR valve, EGR plumbing, charge air coolers, turbochargers, intake air filters, and other related components,” Otto said. “If any of these components fail and you let them get out of hand, you’ll start making a lot more smoke, which puts considerably more burden on the DPF.”
See also: How to reduce engine and aftertreatment maintenance
“The EGR cooler was a major contributor to downstream failures back in 2010,” Hough related. The EGR cooler is essentially a heat exchanger that is repeatedly subjected to coolant followed by extremely hot exhaust gas. That is stressful to the EGR’s internal materials, which can lead to cracks. Cracks can lead to leaks, allowing coolant to find its way to the DOC, SCR, and ultimately the DPF.
Also upstream is the engine itself. If the engine develops an oil-consumption problem, the DPF will be burdened even more. “The problem with engine oil is that part of the additive package is not hydrocarbon and cannot be oxidized away during an active regen,” Otto explained. “The ash that’s left behind keeps building up until the DPF has to be taken out and put in a cleaning machine.”
Similarly, DPF issues likely will arise when a head gasket failure results in coolant leaking into the power cylinder or exhaust stream. “Coolant has the same problem oil does,” Otto noted. “Coolant is mostly water and glycol, but some of what’s in a coolant turns to ash. If you can catch these things early through regular maintenance cycles, the DPF has a much better chance of living longer.”
In addition to upstream problems, there are certain applications that place an extra burden on a DPF.
“An emissions system needs three things: time, temperature, and pressure,” Hough explained. “If you don’t give the system enough time to build up enough heat and pressure, it is never going to cleanse itself (passive regen). A truck hauling a heavy load from coast to coast will likely have very limited DPF issues because it has the time to do what it needs to do. On the other hand, a city delivery vehicle may run into a lot of issues. Understanding the application and environment can help fleets work through a lot of DPF issues.”
According to Detroit Products’ Copeland, one of the most important things a fleet can do is spec properly. Configuring a truck to its specific application will result in better aftertreatment system performance.
“For example, if extended periods of idling are anticipated, Detroit recommends enabling Auto-Elevate either through upfront spec’ing or turning it on via a parameter update,” Copeland said. Auto-Elevate ramps up engine RPMs during periods of idling to increase temperatures.
Fleets have adopted various strategies for situations that place an additional burden on the DPF. “Some fleets tend to shorten the cleaning interval or replacement cycle simply because too many maintenance issues arise if they don’t,” Otto said.
One thing to keep in mind is that a forced regen isn’t always the answer. In fact, it can be counterproductive.
“Many technicians use a forced regen as their first repair attempt when a fault code indicates an issue with the aftertreatment system,” said Lee Lackey, product manager with Noregon Systems, a provider of diagnostic, repair, and data analytic solutions. “But forcing a regen uses a considerable amount of fuel, typically a gallon or more per regen. Additionally, forcing a regen causes undue stress to the components.”
In some instances, the best course of action is to have the DPF cleaned. Fleets have benefited from vastly improved DPF designs. As Otto pointed out, typical cleaning intervals used to be in the 250,000 to 300,000 mile range. Now some truck manufacturers say a DPF can go as long as 600,000 miles before it needs to be cleaned. It’s critical to understand each asset in the fleet to really dial in the proper maintenance schedule.
With an effective cleaning, Penske Truck Leasing’s Hough said it is common to restore a DPF to 90% capacity. The trick for a fleet is ensuring that the DPF has been cleaned effectively. Regardless, a fleet may still determine that replacement makes the most sense.
When the time comes to clean a DPF, Detroit recommends sourcing a remanufactured (reconditioned) filter rather than having it cleaned by a third party. “Detroit has an extensive, proprietary, environmentally friendly washing service,” Copeland said. “This process utilizes a liquid cleaning followed by the traditional high-temperature ‘bake and blow,’ removing more than 95% of the ash from the filter compared to about 30% on average for just ‘bake and blow’ cleaning.”
Cummins has gone away from reconditioned DPFs. The company’s website says a field cleaning is a cost-effective maintenance option for a DPF’s first recommended service. But when it comes time for a second cleaning, the company recommends replacement with a genuine OE DPF.
With the ongoing supply chain challenges, fleets should know they do have options when replacing a DPF. Unless located in California, which does not allow for the sale of non-OEM filters without CARB approval, a fleet could consider an aftermarket DPF. This is where fleet managers can face a difficult decision when it comes to something as vital and potentially volatile as a DPF.
“Our preference is to always stick with the OEMs,” Hough said. “Then we know that the DPF is what the vehicle has been certified with. I’m not saying there is anything wrong with aftermarket. We’ve just never evaluated aftermarket filters or went in that direction.”
Otto concurred. “When it comes to a product as technically sophisticated as a DPF, I would not be too quick to jump to an aftermarket product,” he noted. “From what I have seen, will-fit products copy designs but often thrift on certain things.”
Dave Jerman, sales director for Roadwarrior Inc., said a quality aftermarket replacement can be a viable alternative to an OE DPF. However, a fleet should resist the urge to purchase the cheapest aftermarket product it can find.
“Not all aftermarket manufacturers are created equal,” Jerman said. “Fleets should do their homework and talk to other fleets. Don’t just take it from the manufacturer. Ask people who already use the product, and then let the product speak for itself.”
Jerman said Roadwarrior has worked to keep pace with product evolution. For example, when the industry started to shift from a cordierite substrate material to advanced cordierite, Roadwarrior followed suit. “The key is making sure your aftermarket product is a true OE replacement,” Jerman said. That means an aftermarket DPF’s characteristics and performance must match the OE version to work correctly with the engine ECM.
Jerman said supply chain challenges have driven new customers to Roadwarrior over the past year. “Many of the major U.S. dealers carry our products, including Rush Enterprises. We’ve been getting orders from places we normally would not expect, including some OE dealers. We had supply when a lot of others didn’t.”
Copeland said Detroit Products is not one of those that haven’t had supply. “Detroit’s robust production, remanufacturing, and distribution centers are in the United States with American-made and sourced technologies. We are happy to report that there is no shortage of DPFs in our pipeline,” Copeland said.
On the topic of supply chain, the computer chip shortage also is affecting aftertreatment systems. As Noregon’s Lackey explained, component manufacturers gained approval from the EPA earlier this fall to reprogram their systems to ignore DEF quality sensors because the chip shortage has been making it impossible to replace faulty sensors.
“Fleets should ensure that all truck components are operating the latest software versioning to help mitigate side effects from parts supply shortages,” Lackey advised.
“It’s always important to keep up with engine ECU (electronic control unit) updates,” Otto added. “You never know when an update includes something designed to improve ATS performance.”
Lackey said technology also can help fleets alleviate supply chain headaches through analytics and forecasting.
“We’ve learned from analyzing fault data that one manufacturer’s engines consistently register a fault around 400,000 miles, advising that the DPF be replaced,” Lackey said. “Instead of being caught off guard with limited options due to supply chain issues, projecting maintenance gives the fleet more time to order parts and not rely on just-in-time delivery when a fault occurs.”
Not allowing oneself to be caught off guard is the essence of DPF management today. DPFs can still be volatile, but as Otto phrased it, “The DPF is typically the victim, not the villain.” That’s why it’s a good idea for fleets to start babying the DPF instead of blaming it.
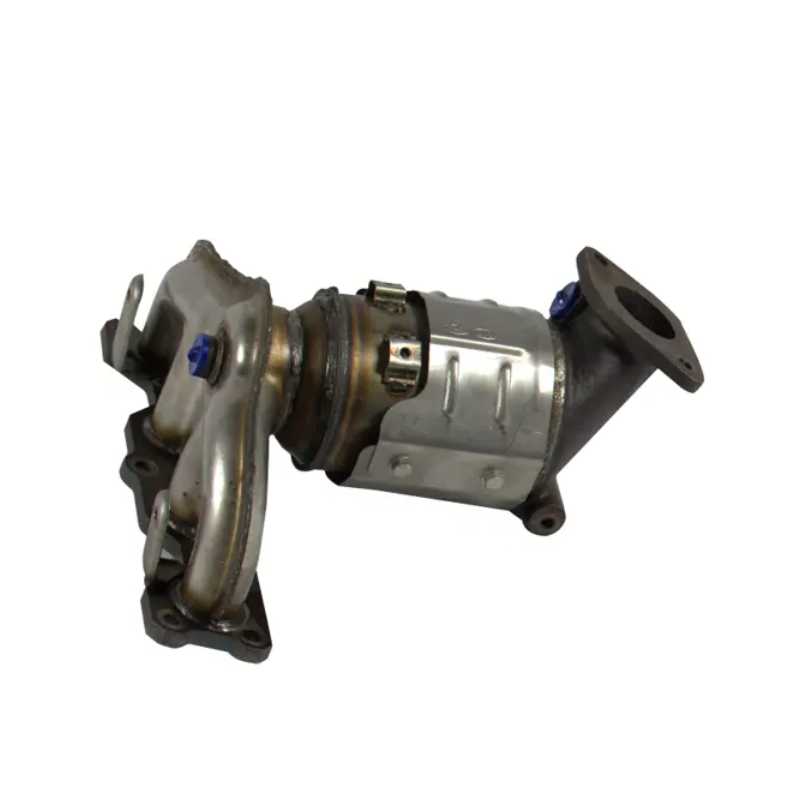
ODM Universal-Fit Catalytic Converter Gregg Wartgow covers the trucking and maintenance industries for Endeavor Business Media's Commercial Vehicle Group, which includes Fleet Maintenance and FleetOwner.