Cubic boron nitride inserts are best used in light semi-finishing and finishing operations.
The manufacture of the hardest cutters on the planet involves some intense processes and chemistry. Polycrystalline diamond (PCD) tools and cubic boron nitride (CBN) are one and two, respectively, on the list of hardest insert materials, but their makeups are quite different. Grinding Wheel

Without getting into the real nitty-gritty of the chemistry, extreme heat, sintering, and pressure all are used to form the different grades of these inserts based on their material-to-binding ratio.
BIG Daishowa, which specializes in holders but also offers CBN- and PCD-tipped inserts with custom chipbreaker forms for its boring tools, often gets questions about this style of tooling. Matt Tegelman, senior product specialist, was asked some of the most common questions. Here, we share his answers.
Q: As a toolholding expert, how do you describe the importance of the tool/holder interface? A: Only the most stable conditions are suited for PCD and CBN. With high hardness comes highly brittle characteristics. If the rigidity of the tooling or fixturing is not ideal, or if a workpiece has severe harmonics caused by excessive voids, vibrations can manifest in the cut. This leads to poor tool life of the diamond cutting edge. In these cases, it is best to stick with carbide inserts.
Q: What’s the biggest difference between PCD and CBN inserts? A: A PCD insert should be the first choice in aluminum and magnesium applications, as well as for carbon fibre parts, because its extreme hardness provides very long tool life in these non-ferrous materials.
Because it is a synthetic diamond (almost pure carbon), it cannot be used to machine ferrous materials, such as steels and cast irons, because at temperatures over 700 degrees F, carbon atoms react with the part material to form iron carbide and cause the diamond structures to collapse.
PCD is especially required when aluminum has more than 5 per cent silicon content to resist the abrasiveness that leads to wear.
CBN uses boron as the primary element. While boron has a similar crystal structure to carbon, it lacks its affinity to iron.
It is the second-hardest known material and can tolerate cutting temperatures over 1,800 degrees F. CBN is suitable for steel or iron machining and is one of the first choices for working with hardened steels, usually more than at least 50 HRC, and should be used for finishing only. Any interrupted cutting requires the highest-stability tool possible, otherwise it won’t work well.
CBN comes in different grades, in which binders, such as ceramics and metals are added to change the characteristics. Grain sizes of the crystal structure also can be tweaked for certain characteristics. High CBN content with ultrafine grain sizes is the hardest combination, suitable for continuous machining of hardened cast iron and powdered metals.
Cubic boron nitride tools come in different grades, in which binders, such as ceramics and metals, are added to change the characteristics.
CBN inserts also can be coated. For example, a medium-grain-size CBN material with a TiCN coating is recommended for machining hardened steels.
Q: What is the best minimum/maximum depth of cuts for PCD and CBN inserts? A: PCD and CBN inserts are best reserved for light semi-finishing and finishing operations. I’d generally recommend a maximum of 0.040 in. stock on diameter and minimums down to 0.004 in., depending on the insert’s nose radius.
Q: What is the relationship between surface finish and a tool’s nose radius? A: A larger nose radius produces a better surface finish for a given feed rate. Therefore, the larger the radius, the faster you can feed the tool and still get a good finish. The trade-off comes in tool pressure. A larger radius causes more deflection on the tool and, at a certain point, can lead to chatter. The trick is finding the largest radius that produces chatter-free results.
A way around this is to use a wiper geometry, which is now offered for some PCD and CBN inserts. A wiper is a secondary, smaller radius or series of smaller radii that follow the main corner radius to additionally smooth the scalloped profile of the main corner’s cut. It’s a way to get a better feed-to-surface-finish ratio.
Q: Should coolant be used with PCD and CBN inserts? A: Use either a lot of coolant or none at all. Thermal fracture of these materials happens with large temperature fluctuations. If coolant is used effectively, it helps increase tool life and improve chip evacuation. If coolant can’t be directed at the cutting action with consistent flow, it will be detrimental to the operation.
Q: Does edge preparation matter with PCD and CBN inserts? A: The extreme processes used to create these very hard cutter materials make edge preparation important for both CBN and PCD tools, both for reinforcement and chip control. What’s more, you’ll always find microscopic edge defects on nearly every tool before edge preparation. When high performance is required, as is often the case with these cutters, preparation eliminates defects that cause erratic performance.
PCD and CBN inserts now are offered with almost as many edge preparation styles as carbide inserts. They are categorized by “land” types, and each type gives advantages for specific materials and cutting conditions.
Q: How do you match a land type with an application or material? A: Most edge preps still consist of a radius hone, and a smaller radius typically is preferred so more material is left at the cutting edge, giving longer tool life. A waterfall hone skews the radius to leave more material under the cutting edge to strengthen it for heavier cuts or interrupted-cut applications, but this style also leads to higher tool pressures.
Q: Are there minimum and maximum speeds for PCD and CBN inserts? A: Contrary to most perceptions, PCD has a wide range of allowable surface feet per minute (SFM) settings for aluminum, from as low as 200 SFM to 6,000 SFM, and it typically outlasts carbide inserts by at least 10 times, allowing tools to remain in tolerance without adjustments for very long periods of cutting time.
With CBN inserts, feeds as low as 200 SFM often are used in hardened steel applications.
Polycrystalline diamond tools often are used to machine aluminum that has more than 5 per cent silicon content because it can withstand its abrasiveness.
Speed also depends on the tool assembly as a whole. For boring tools, for example, it often is necessary to consider the tool assembly and workpiece setup rigidity when making the decision to use high-speed machining with these types of inserts. Often a boring head with built-in counterweights for balance is required to be able to run the speeds that these inserts are capable of.
Q: What are the common wear modalities for these inserts? A: Crater wear occurs in CBN machining of iron-based and titanium-based alloys when the heat from the workpiece’s chips dissolves and disperses the cemented carbide binding agents and forms craters on the top of the tool. Once the craters grow large enough to cause microcollapsing of the crystal structure, deformation and rapid flank wear occur.
Built-up edge (BUE) happens when fragments of the workpiece are bonded to the cutting edge by hot-pressure welding (a combination of high pressure and temperature along with chemical affinity in the cutting zone).
This buildup eventually will fail, and when it does, it also can take some of the cutting edge with it. This issue can be identified by abnormal changes in the workpiece’s feature size or surface finish and shiny areas on the cutting edge’s surface. BUE often can be controlled by increasing the tool’s cutting load (higher cutting speed and/or feed) or by altering the coolant flow or concentration in the cutting zone.
BIG Daishowa, www.bigdaishowa.com
Because of their extreme hardness, polycrystalline diamond tools provide a very long tool life in non-ferrous materials.
Read more from this issue
Find Canadian Metalworking on Facebook
Find Canadian Metalworking on X
Keep up to date with the latest news, events, and technology for all things metal from our pair of monthly magazines written specifically for Canadian manufacturers!
Easily access valuable industry resources now with full access to the digital edition of Canadian Metalworking.
Easily access valuable industry resources now with full access to the digital edition of Canadian Fabricating & Welding.
LOGIQ3CHAM drills ensures increasing productivity by up to 50% when compared with a common two-flute drill with exchangeable heads Available in Diameter Range of 12-25.9 mm with 3 & 5xD body overhang.
© 2024 FMA Communications Canada, Inc. All rights reserved.
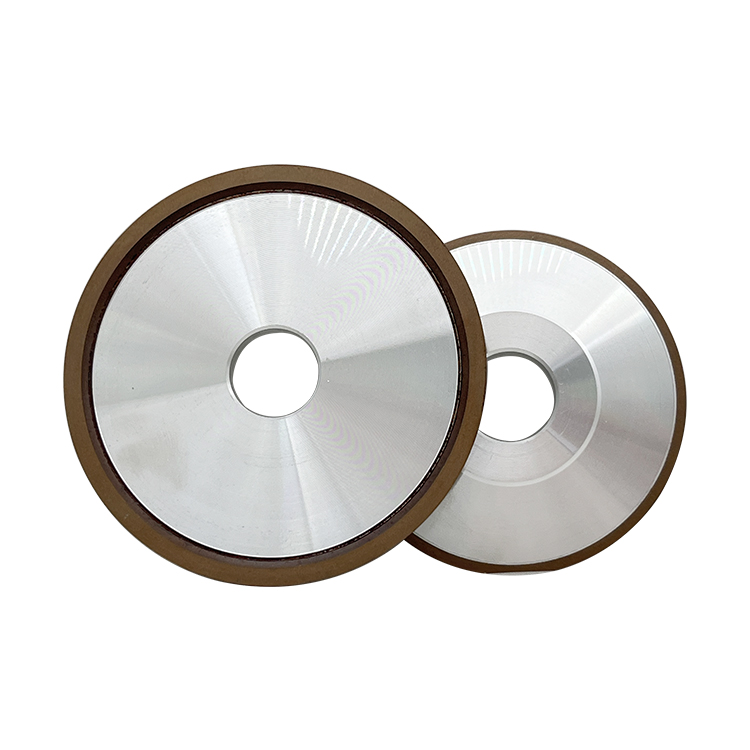
8 Cbn Grinding Wheel Not yet registered? Sign up