The eVTOL aircraft company is now authorized to perform specialized aircraft repair services on crucial aircraft components.
Manufacturing Type V composite pressure vessels, Infinite Composites will match this project with a recently received $1.6 million award from the Army for conformable hydrogen tanks. Fibre Reinforced Polymer
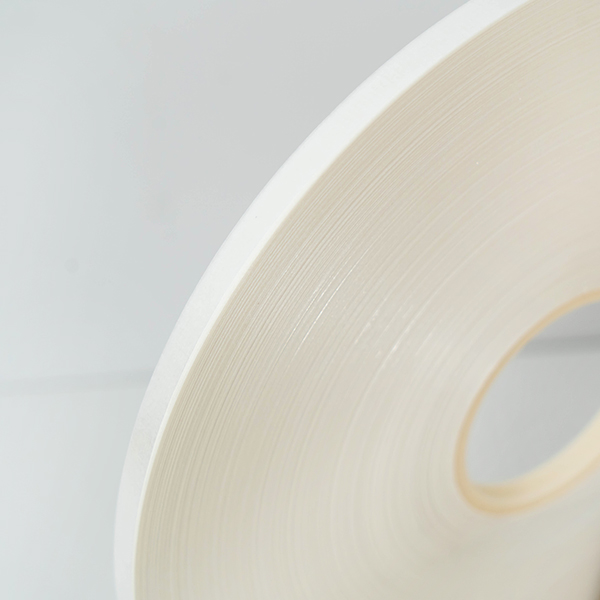
Working alongside partner Bristow, the AAM company exhibited the CTOL aircraft’s capabilities and maneuverability.
The delivery, to include 75,000 GFRP seats, marks Recaro’s entry into the AAM market.
Component assembly of Archer Aviations’ eVTOL aircraft, to be used in FAA “for credit” testing, is well underway, with final assembly on track to begin in the coming weeks.
Propelled by a hydrogen-electric propulsion system, the composites-intensive vehicle will take flight in two version options by 2025.
Kineco Kaman Composites India uses a bespoke Fill Accubot ultrasonic testing system to boost inspection efficiency and productivity.
JEC World 2024: With new logo and rebranding in hand, Composite Test & Evaluation Ltd. invites industry and potential partners to learn more about its decades experience in material, evaluation services.
Through a strategic partnership, the companies introduce the FiberScanner3D module, dedicated to bringing more rapid, reliable and robust fiber structure characterization methods to lab settings.
The new alliance will broaden National Composites’ capabilities in SMC and BMC and tooling, while providing customers with comprehensive solutions, from initial design to final delivery.
A new ASTM-standardized test method established in 2022 assesses the compression-loaded damage tolerance of sandwich composites.
Composites automation specialist increases access to next-gen technologies, including novel AFP systems and unique 3D parts using adaptive molds.
At laboratory scale, functionalized CFRP thermosets can be “released” via heat or chemicals to reincarnate them back into their starting materials.
Ohio-based Canvus Inc. upcycles fiberglass wind blades, car tires and post-consumer plastics to create outdoor furniture that amplifies sustainability messages in community spaces.
The delivery, to include 75,000 GFRP seats, marks Recaro’s entry into the AAM market.
Texas-based Champion Fiberglass, a five-time CW Top Shops honoree, expands its success in the fiberglass composite conduit market into new applications and products, looking toward future automation and sustainability initiatives.
Through the ScrapSeRO project, the system integrator and machine builder successfully processed recycled composites, in addition to more traditional materials, via its highly flexible Staxx One system.
High-end design furniture is 3D printed from bio-based, eco-friendly materials for aesthetic and sustainable home product options.
Caracol continues to evolve large-format additive manufacturing, opening two additional state-of-the-art facilities to accommodate client services, as well as materials and processes R&D.
Texas-based Champion Fiberglass, a five-time CW Top Shops honoree, expands its success in the fiberglass composite conduit market into new applications and products, looking toward future automation and sustainability initiatives.
Through the ScrapSeRO project, the system integrator and machine builder successfully processed recycled composites, in addition to more traditional materials, via its highly flexible Staxx One system.
Carbon fiber-reinforced polyamide, added to CRP’s Top-Line series, is well suited to demands for lightness, stiffness and thermal resistance in composites 3D printing.
JEC World 2024: Fives invites attendees to learn more about its specialization in providing composites precision and performance, whether its through its Cincinnati, Forest-Liné and Lund lines or its ACE and COAST engineering suites.
Maine-based CW Top Shops honoree Compotech Inc. recently doubled its manufacturing space and team to produce modular composite panels for defense applications via light resin transfer molding (LRTM).
CW explores key composite developments that have shaped how we see and think about the industry today.
Knowing the fundamentals for reading drawings — including master ply tables, ply definition diagrams and more — lays a foundation for proper composite design evaluation.
As battery electric and fuel cell electric vehicles continue to supplant internal combustion engine vehicles, composite materials are quickly finding adoption to offset a variety of challenges, particularly for battery enclosure and fuel cell development.
Performing regular maintenance of the layup tool for successful sealing and release is required to reduce the risk of part adherence.
The composite pressure vessel market is fast-growing and now dominated by demand for hydrogen storage.
With COVID in the past and passengers flying again, commercial aircraft production is ramping up. The aerocomposites supply chain is busy developing new M&P for an approaching next-generation aircraft program.
With advancements in raw materials technology and processing, more sustainable and economical solutions for composite tooling are increasingly available. This webinar will discuss the potential for epoxy tooling prepregs to provide additional benefits and cost savings when producing composite tools for the aerospace and automotive markets. Agenda: Principles of ply reduction: best practices Key benefits of faster lamination Proving the case What's next for the future
The burgeoning advanced air mobility (AAM) market promises to introduce a new mode of transport for urban and intercity travelers — particularly those who wish to bypass the traffic congestion endemic to the world’s largest cities. The electric vertical take-off and landing (eVTOL) aircraft serving this market, because they depend on battery-powered propulsion, also depend on high-strength, high-performance composite structures produced at volumes heretofore unseen in the aerospace composites industry. This CW Tech Days will feature subject matter experts exploring the materials, tooling and manufacturing challenges of ramping up composites fabrication operations to efficiently meet the demands of a challenging and promising new marketplace.
Manufacturers often struggle with production anomalies that can be traced back to material deviations. These can cause fluctuations in material flow, cooling, and cure according to environmental influences and/or batch-to-batch variations. Today’s competitive environment demands cost-efficient, error-free production using automated production and stable processes. As industries advance new bio-based, faster reacting and increased recycled content materials and faster processes, how can manufacturers quickly establish and maintain quality control? In-mold dielectric sensors paired with data analytics technology enable manufacturers to: Determine glass transition temperature in real time Monitor material deviations such as resin mix ratio, aging, and batch-to-batch variations throughout the process Predict the influence of deviations or material defects during the process See the progression of curing and demold the part when the desired degree of cure, Tg or crystallinity is achieved Document resin mix ratios using snap-cure resins for qualification and certification of RTM parts Successful case histories with real parts illustrate how sensXPERT sensors, machine learning, and material models monitor, predict, and optimize production to compensate for deviations. This Digital Mold technology has enabled manufacturers to reduce scrap by up to 50% and generated energy savings of up to 23%. Agenda: Dealing with the challenge of material deviations and production anomalies How dielectric sensors work with different composite resins, fibers and processes What is required for installation Case histories of in-mold dielectric sensors and data analytics used to monitor resin mixing ratios and predict potential material deviations How this Digital Mold technology has enabled manufacturers to optimize production, and improve quality and reliability
SolvaLite is a family of new fast cure epoxy systems that — combined with Solvay's proprietary Double Diaphragm Forming technology — allows short cycle times and reproducibility. Agenda: Application Development Center and capabilities Solutions for high-rate manufacturing for automotive Application examples: battery enclosures and body panels
OEMs around the world are looking for smarter materials to forward-think their products by combining high mechanical performance with lightweight design and long-lasting durability. In this webinar, composite experts from Exel Composites explain the benefits of a unique continuous manufacturing process for composites profiles and tubes called pull-winding. Pull-winding makes it possible to manufacture strong, lightweight and extremely thin-walled composite tubes and profiles that meet both demanding mechanical specifications and aesthetic needs. The possibilities for customizing the profile’s features are almost limitless — and because pull-winding is a continuous process, it is well suited for high volume production with consistent quality. Join the webinar to learn why you should consider pull-wound composites for your product. Agenda: Introducing pull-winding, and how it compares to other composite manufacturing technologies like filament winding or pultrusion What are the benefits of pull-winding and how can it achieve thin-walled profiles? Practical examples of product challenges solved by pull-winding
Composite systems consist of two sub-constituents: woven fibers as the reinforcement element and resin as the matrix. The most commonly used fibers are glass and carbon, which can be processed in plane or satin structures to form woven fabrics. Carbon fibers, in particular, are known for their high strength/weight properties. Thermoset resins, such as epoxies and polyurethanes, are used in more demanding applications due to their high physical-mechanical properties. However, composites manufacturers still face the challenge of designing the right cure cycles and repairing out-of-shelf-life parts. To address these issues, Alpha Technologies proposes using the encapsulated sample rheometer (premier ESR) to determine the viscoelastic properties of thermosets. Premier ESR generates repeatable and reproducible analytical data and can measure a broad range of viscosity values, making it ideal for resins such as low viscous uncured prepreg or neat resins as well as highly viscous cured prepregs. During testing, before cure, cure and after cure properties can be detected without removing the material from the test chamber. Moreover, ESR can run a broad range of tests, from isothermal and non-isothermal cures to advanced techniques such as large amplitude oscillatory shear tests. During this webinar, Alpha Technologies will be presenting some of the selected studies that were completed on epoxy prepreg systems utilizing ESR and how it solves many issues in a fast and effective way. It will highlight the advantages of this technique that were proven with the work of several researchers. Moreover, Alpha Technologies will display part of these interesting findings using the correlations between the viscoelastic properties such as G’ and mechanical properties such as short beam shear strength (SBS).
The Program of this Summit consists of a range of 12 high-level lectures by 14 invited speakers only. Topics are composite related innovations in Automotive & Transport, Space & Aerospace, Advanced Materials, and Process Engineering, as well as Challenging Applications in other markets like Architecture, Construction, Sports, Energy, Marine & more.
JEC World in Paris is the only trade show that unites the global composite industry: an indication of the industry’s commitment to an international platform where users can find a full spectrum of processes, new materials, and composite solutions.
Charting the Skies of Tomorrow: The Sustainable Aviation Revolution Welcome to a new era of air travel where innovation meets sustainability. Electric, hybrid-electric and hydrogen-powered aircraft represent a promising path to reach climate neutrality goals, with the aviation industry and governments jointly pushing boundaries to bring disruptive aircraft into service by 2035. From cutting-edge technologies to revamped regulations and greener airports, the pursuit of sustainable aviation requires unparalleled collaboration throughout the whole aviation value chain and ecosystem. Join us at the Clean Aviation Annual Forum from 5 until 6 March 2024, as we navigate towards cleaner skies together.
Composites 2024 is an international conference that focuses on advanced technology and development of composite materials. It brings together participants from academia and industry who share an interest in Composite Materials. It is a unique opportunity for composite specialists and newcomers alike and has long been a venue where researchers and industrialists network and share with colleagues from around the world and establish long term partnership. The conference includes plenary talks, keynote and oral presentations as well as posters sessions, an exhibit area for industry partners and sponsors, and an entertaining social program.
The European polyamide market is going through unprecedented times as it grapples with rising energy and feedstock prices, as well as declining consumption levels with lower demand from almost all application segments (including automotive, construction, fibres and E&E). Coupled with the growing emphasis on sustainability, recycling and the circular economy, this is a challenging period for the polyamide market in Europe. Is 2024 the year that the polyamide segment looks to emerge from the crisis tunnel? The industry needs to adapt to the new market reality, to innovate and invest in new technologies and processes to meet the new market demands and requirements with regards to economic sustainability and a circular economy. The Wood Mackenzie European Polyamide Conference takes place at the Kap Europa Congress Center in Frankfurt, Germany on 13-14 March 2024, combining integrated analysis across the polyamide value chain with sessions focused on feedstocks, polymers, and key application markets, deep dives into emerging trends and technologies. Themes for 2024 include: Is there any hope for the European polyamide industry? Is the polyamide profitability gone? What can we expect in the coming years? Will China's importation threat permanently change the European polyamide market? What are the future polyamide price trends and forecasts? Who will be the winners and losers of the current situation Is the circular economy a threat or an opportunity for the polyamide industry?
From 20-22 March, WindEurope’s annual on- and offshore wind energy event will be heading to Bilbao for a three-day conference and exhibition. You can expect 10,000+ attendees to join us for a look at the shape of European wind energy today. There’ll be dozens of conference sessions, hundreds of speakers, and 400+ exhibitors from the whole value chain looking to showcase their innovations and seal new deals. We’ll have social events across the event for you to reach out to new colleagues and educational sessions showing you all the ins and outs of wind energy. And plenty of time in between it all to sample all the gastronomic and architectural delights Bilbao has to offer!
Thousands of people visit our Supplier Guide every day to source equipment and materials. Get in front of them with a free company profile.
Jetcam’s latest white paper explores the critical aspects of nesting in composites manufacturing, and strategies to balance material efficiency and kitting speed.
Arris presents mechanical testing results of an Arris-designed natural fiber thermoplastic composite in comparison to similarly produced glass and carbon fiber-based materials.
Cevotec, a tank manufacturer, Roth Composite Machinery and Cikoni, have undertaken a comprehensive project to explore and demonstrate the impact of dome reinforcements using FPP technology for composite tanks.
Initial demonstration in furniture shows properties two to nine times higher than plywood, OOA molding for uniquely shaped components.
The composite tubes white paper explores some of the considerations for specifying composite tubes, such as mechanical properties, maintenance requirements and more.
Foundational research discusses the current carbon fiber recycling landscape in Utah, and evaluates potential strategies and policies that could enhance this sustainable practice in the region.
Texas-based Champion Fiberglass, a five-time CW Top Shops honoree, expands its success in the fiberglass composite conduit market into new applications and products, looking toward future automation and sustainability initiatives.
Kineco Kaman Composites India uses a bespoke Fill Accubot ultrasonic testing system to boost inspection efficiency and productivity.
The GBI: Composites Fabricating contracted in January to about the same degree it did in December, representing a move in the right direction.
The use of composites in industrial applications is increasing, driven by the need for higher performance and longer life, whether its parts for industrial machinery, EOAT components, corrosion-resistant equipment and more.
Maine-based CW Top Shops honoree Compotech Inc. recently doubled its manufacturing space and team to produce modular composite panels for defense applications via light resin transfer molding (LRTM).
GA-ASI demonstrates a path forward for the use of additive technologies for tooling, flight-qualified parts.
Affordable, lightweight and sustainable composite materials made from mycelium — mushroom roots — may have potential for packaging materials, insulation panels, floor tiles and furniture.
Bringing on Syensqo as its main materials and technological partner, Swiss explorer Bertrand Piccard hopes to stimulate climate action by demonstrating disruptive solutions in this 2028 aircraft design.
CW provides examples of current developments and collaborations in sustainable fiber development, accessibility.
U.K. initiative, with the NCC, CPI, SHD Composites, Scott Bader and Polestar will work to convert biomass byproduct into lignin for automotive plastics, resins and composites.
Projects use Duplicor prepreg panels with highest Euroclass B fire performance without fire retardants for reduced weight, CO2 footprint in sustainable yet affordable roofs, high-rise façades and modular housing.
To incorporate more environmentally conscious practices into its manufacturing processes, VSC is working with Carbon Conversions to reclaim, recycle and reuse its carbon fiber materials.
The composites industry is increasingly recognizing the imperative of sustainability in its operations. As demand for lightweight and durable materials rises across various sectors, such as automotive, aerospace, and construction, there is a growing awareness of the environmental impact associated with traditional composite manufacturing processes.
CW’s editors are tracking the latest trends and developments in tooling, from the basics to new developments. This collection, presented by Composites One, features four recent CW stories that detail a range of tooling technologies, processes and materials.
CompositesWorld’s CW Tech Days: Infrastructure event offers a series of expert presentations on composite materials, processes and applications that should and will be considered for use in the infrastructure and construction markets.
This CW Tech Days event will explore the technologies, materials, and strategies that can help composites manufacturers become more sustainable.
Closed mold processes offer many advantages over open molding. This knowledge center details the basics of closed mold methods and the products and tools essential to producing a part correctly.
Explore the cutting-edge composites industry, as experts delve into the materials, tooling, and manufacturing hurdles of meeting the demands of the promising advanced air mobility (AAM) market. Join us at CW Tech Days to unlock the future of efficient composites fabrication operations.
During CW Tech Days: Thermoplastics for Large Structures, experts explored the materials and processing technologies that are enabling the transition to large-part manufacturing.
In the Automated Composites Knowledge Center, CGTech brings you vital information about all things automated composites.
CompositesWorld’s CW Tech Days: Infrastructure event offers a series of expert presentations on composite materials, processes and applications that should and will be considered for use in the infrastructure and construction markets.
Explore the cutting-edge composites industry, as experts delve into the materials, tooling, and manufacturing hurdles of meeting the demands of the promising advanced air mobility (AAM) market. Join us at CW Tech Days to unlock the future of efficient composites fabrication operations.
Thermoplastics for Large Structures, experts explored the materials and processing technologies that are enabling the transition to large-part manufacturing.
Explore the technologies, materials, and strategies that can help composites manufacturers become more sustainable.
A report on the demand for hydrogen as an energy source and the role composites might play in the transport and storage of hydrogen.
This collection features detail the current state of the industry and recent success stories across aerospace, automotive and rail applications.
This collection details the basics, challenges, and future of thermoplastic composites technology, with particular emphasis on their use for commercial aerospace primary structures.
This collection features recent CW stories that detail a range of tooling technologies, processes and materials.
Extruded PP (XPP) foam core offers lightweight, high-performance monomaterial panels that are easily recycled for truck flooring, sidewalls or cabinet/furnitureboards as the transportation industry seeks a replacement for plywood.
Hardex XPP foam core offers lightweight, recyclable composite panels as replacement for plywood. Photo Credit: (top left) Spur (top right, bottom images) Getty Images
Multiple companies worldwide have developed new grades of polypropylene (PP) foam aiming for higher properties and lower weight, mostly for injection molding interior parts for the automotive industry (see recent market report). Toray Industries (Tokyo, Japan) has also developed a new cross-linked PP foam core for helmet and cushioning applications. But what Spur (Zlín, Czech Republic) is offering is much different, targeting sandwich structures using fiber-reinforced composite skins — a market considered by most large plastics companies as ancillary or niche.
“We too are a plastics manufacturer,” says David Pospisil, business manager for Spur, “but we saw a need developing 5-6 years ago for lightweight, high-performance panels that can be easily recycled. So, we started developing what is now our Hardex XPP (Extruded PP) closed-cell foam core.”
Spur shreds Hardex PP foam-cored sandwich panels and regranulates that material for extrusion into profiles for kitchen cabinets and furniture. Photo Credit: Spur
Is it indeed easily recycled? “We have been producing XPP foam for lamination with PP skins in full PP lightweight panels used by Better Shelter for refugee housing,” says Pospisil. “And the waste from this production we are upcycling into other products in our factory, such as kitchen profiles and edge bands for furniture. But we can definitely recycle the whole panel, even with skins using fiber reinforcement, back into an extrusion-grade material, which we are doing in-house.” To learn more, watch the Spur webinar hosted by CompositesWorld on May 24, 2023, “Thermoplastic Foam Cores for Composites: Light, Productive, Recyclable XPP.”
Pospisil says there is a lot of demand for lightweight materials in trucks and trailers. “We have done a lot of testing with our materials in floors and sidewalls of truck trailers,” he explains, “and we have a number of products in development. More broadly, there is a huge demand in the automotive market to replace PVC [polyvinylchloride] and PET [polyethylene terephthalate] foam with PP foam in order to achieve monomaterial parts that are easier to recycle. Previously, these types of parts used several different types of materials usually glued together, so that separating was required and a bit difficult, making recycling more challenging and expensive. With our material, you can produce a PP sandwich panel with PP skins and Hardex XPP foam core, fused together with thermal bonding. When you’re done, you can shred that panel and regranulate it into a material for extrusion. This is what we are doing now, so it’s proven technology.”
“By replacing plywood with Hardex XPP foam in these flooring panels, it is possible to drop 300-400 kilograms per truck trailer.”
This approach is what Spur is pursuing in truck trailers, where Hardex XPP is the foam core and the skins are typically glass fiber-reinforced PP. “If our customers use a heated double belt press with cooling to join the skins to the core, they can produce these panels at a rate of 4 meters/minute. Currently, production of truck panels is very slow, where FRP [fiber-reinforced polymer] skins are glued and vacuum-formed with foam and other cores, often taking hours for the adhesives to cure. With our materials, you replace that system with thermal lamination. We are merely making the foam. But this is a big opportunity for our customers, who are fabricating panels and parts that are offering new solutions for the transportation industry.”
Hardex XPP foam core offers lightweight panels for truck trailer flooring and sidewalls, which can then be recycled into truck skirts and fairings. Photo Credit: Getty Images
Can foam core really stand up to the in-service abuse seen by truck trailer floors? “So far, we are confident that these panels will be able to resist the loads seen in truck floors and sidewalls, but this is what we are working through as part of various development projects,” says Pospisil. “If more resistance is needed, then panel manufacturers can apply another ply of glass/PP tape, for example, or reinforce localized areas.”
He notes the goal is to replace plywood, which has become much harder to obtain, more expensive and is also heavy. “By replacing plywood with Hardex XPP foam in these flooring panels, it is possible to drop 300-400 kilograms per truck trailer,” says Pospisil. “And, at the end of life for these panels, it’s then possible to shred them, regranulate and extrude the recycled material as side fairings or truck skirts. So, this is a real opportunity to establish a circular product and process chain for these transportation companies.”
Another large market for lightweight, recyclable panels is RVs, where Hardex XPP foam cored-panels can be recycled and reused as edge trim. Photo Credit: Getty Images
He notes another large opportunity is in recreational vehicles (RVs). “We are again looking at sidewalls but also furniture,” says Pospisil. “We are offering significantly lower-weight in a foam-cored panel that has no moisture absorption and can be recycled back into bandings that are already used in RV interior trims and cabinetry. We think this lighter weight construction for furniture will also be attractive for builders of boats, yachts and other marine vessels.”
There are multiple types of PP foam including: expanded PP (EPP), cross-linked PP and extruded PP foam, also abbreviated as XPP. “EPP is a lower modulus particle foam that you will see used in better quality cycling helmet, for example,” says Pospisil. “Our material is XPP but it is extruded foam, not cross-linked. However, our product is much different than EPP and crosslinked PP because we have developed a special grade of polymeric foamthat gives both high mechanical properties and recyclability. We have also developed a unique know-how to get even higher performance than is standard since XPP began widespread development in 2017-18.”
Pospisil says Spur started looking at this new development in XPP foam in 2016 to replace wood in pallets. “But then COVID hit, and we pivoted to producing masks and personal protection equipment. We got back on track with our XPP development in 2021 and by 2022 had samples to show to the automotive industry. We then scaled our production and are now finalizing our machine to make standard size foam boards [2440 x 1220 millimeters, 5-100 mm thick] per our customers’ requirements. In June, we will begin producing these Hardex XPP foam boards in high volume to fulfill serial production orders placed last year. We think now is a good time to work with CompositesWorld and let the composites industry know that we are ready to grow our applications and offer new opportunities for fabricators and OEMs to achieve lightweight and sustainability.”
Manned deepsea exploration calls for a highly engineered composites solution that saves weight and preserves life — at 6,500-psi service pressure.
Shocker Composites and R&M International are developing a supply chain for recycled CF with zero knockdown vs. virgin fiber, lower cost and, eventually, lengths delivering structural properties close to continuous fiber.
Fast-reacting resins and speedier processes are making economical volume manufacturing possible.
Suppliers of thermoplastics and carbon fiber chime in regarding PEEK vs. PEKK, and now PAEK, as well as in-situ consolidation — the supply chain for thermoplastic tape composites continues to evolve.

Aluminum Mylar Shield CompositesWorld is the source for reliable news and information on what’s happening in fiber-reinforced composites manufacturing. Learn More