Overload devices protect motors, motor control equipment, and motor branch-circuit conductors against excessive heating due to motor overloads and failure to start, but not against overcurrent (e.g., short circuits or ground faults). We covered overloads in Part 1.
Motor branch-circuit short-circuit and ground-fault protective devices protect the motor, the motor control equipment, and the conductors against overcurrent, but not against overload. They are generally called overcurrent protective devices (OCPDs), and we’ll look at them next. Dc Ammeter Digital

The motor branch-circuit OCPD must comply with Sec. 430.52(B), (C), and (if torque motors) (D) [Sec. 430.52(A)]. Section 430.52(B) is straightforward: A motor branch-circuit OCPD must be able to carry the motor’s starting current (Fig. 1).
But Sec. 430.52(C) has changed extensively with the 2023 revision — or at least it looks that way at first glance. To determine the size of the OCPD that will protect the motor branch circuit against short circuits and ground faults, you now use Table 430.52(C)(1) instead of Table 430.52.
Another change is Exception No. 1 and Exception No. 2 in the 2020 NEC are now Sec. 430.52(C)(1)(a) and (b) in the 2023 NEC. The actual requirements are the same as in the 2020 NEC. If the value from the table doesn’t correspond to the standard ampere ratings and settings provided in Sec. 240.6, you can use the next higher standard rating or setting [Sec. 430.52(C)(1)(a)]. If the OCPD doesn’t have a high enough ampere rating to permit starting the motor, you have four options [Sec. 430.52(C)(1)(b)].
A motor can be protected against overload, short circuit, and ground fault by a single OCPD sized to the overload requirements in Sec. 430.32 [Sec. 430.55]. The “next size up protection” rule for branch circuits [Sec. 430.52(C)(1)(a)] does not apply to motor feeder OCPDs.
In some cases where there are 3-phase and single-phase motors on the same feeder, the current on L1, L2, and L3 (or Phase 1, Phase 2, and Phase 3) will be different. The “group” is determined by balancing out the motor currents between different phases (lines) of the motor feeder.
Motor control conductors that are not tapped from the motor branch-circuit conductors are classified as a Class 1 remote-control circuit and must have overcurrent protection per Sec. 724.43 [430.72(A)]. In previous Code revisions, this was Sec. 725.43. However, with the 2023 revision, Class 1 circuit requirements were moved from Art. 725 to the new Art. 724.
Overcurrent protection for conductors 14 AWG and larger must comply with the conductor ampacity from Table 310.16. Overcurrent protection for 18 AWG cannot exceed 7A; for 16 AWG conductors, the limit is 10A.
Motor control circuit conductors that are tapped from the motor branch-circuit OCPD and extend beyond the tap enclosure must have overcurrent protection that complies with Sec. 430.72(B)(1) (separate OCPD) or (2) (branch-circuit OCPD). Essentially, you are going to use Table 430.72(B)(2).
Motor control circuit conductors must have a disconnect [Sec. 430.75(A)]. Where these conductors are tapped from the controller disconnect, the controller disconnect can serve as the disconnect for the control circuit conductors [Sec. 430.102(A)]. Where control circuit conductors are not tapped from the controller disconnect (supplied by a Class 1 control circuit), a disconnect located adjacent to the controller disconnect is required (Fig. 2).
Circuit breakers and molded-case switches can serve as motor controllers [Sec. 480.83(A)]. Anything else you use to do that job must have a horsepower rating of at least that of the motor.
The motor controller can be a general-use snap switch for motors rated 2 hp or less where the motor FLC is not more than 80% of the ampere rating of the switch [Sec. 480.83(C)(2)].
Each motor controller must have a disconnect within sight from the controller, and each motor must have a disconnect within sight from the motor. The controller disconnect (if within sight from the motor) can also serve as the disconnect for the motor [Sec. 430.102(B)]. Either the controller disconnect or the motor disconnect required by Sec. 430.102 must be readily accessible [Sec. 430.107].
The disconnect for the motor controller and/or the motor must be one of the seven types listed in Sec. 430.109(A)(1) through (7). For example, a listed horsepower-rated motor circuit switch or a listed molded-case circuit breaker.
For stationary motors of 1⁄8 hp or less, the branch-circuit OCPD can serve as the disconnect [Sec. 430.109(B)]. For stationary motors rated 2 hp or less and 300V or less, the disconnect can be a general-use AC snap switch (not a general-use AC-DC snap switch) where the motor’s full-load current (FLC) as listed in Tables 430.247 through 250 is not more than 80% of the ampere rating of the switch [Sec. 430.109(C)].
A horsepower-rated attachment plug and receptacle, flanged surface inlet and cord connector, or cord connector having a horsepower rating of at least the motor rating can be used as a motor disconnect [Sec. 430.109(F)].
The installation provisions of Part I through Part IX apply to adjustable-speed drives (ASDs) unless modified or supplemented by Part X [Sec. 430.120].
Circuit conductors for an ASD must have an ampacity of at least 125% of the rated input current of the ASD [Sec. 430.122(A)]. ASDs can have multiple power ratings and corresponding input currents [Sec. 430.122(A) Note].
The conductors between the power conversion equipment and the motor must have an ampacity equal to or greater than 125% of the motor’s full-load current (FLC) as listed in Tables 430.247 through 250 [Sec. 430.122(B)].
Exception: If the power conversion equipment is listed and marked as “Suitable for Output Motor Conductor Protection,” the conductor between the power conversion equipment and the motor must have an ampacity equal to or greater than the larger of:
(1) 125% of the motor’s full-load current (FLC) as determined by Sec. 430.6(A) or (B).
(2) The ampacity of the minimum conductor size marked on the power conversion equipment.
Informational Note No. 1: The minimum ampacity required of output conductors is often different from that of the conductors supplying the power conversion equipment. See Sec. 430.130 and Sec. 430.131 for branch-circuit protection requirements.
Informational Note No. 2: Circuit conductors on the output of an ASD are susceptible to breakdown under certain conditions due to the characteristics of the output waveform of the drive. Factors affecting the conductors include (but are not limited to) the output voltage, frequency and current, the length of the conductors, the spacing between the conductors, and the dielectric strength of the conductor insulation. Methods to mitigate breakdown include consideration of one or more of these factors.
Conductors supplying several motors or a motor and other loads (including power conversion equipment) must have ampacity per Sec. 430.24, using the rated input current of the power conversion equipment for purposes of calculating ampacity [Sec. 430.122(D)].
Where the ASD is marked to indicate that motor overload protection is included, additional overload protection is not required [Sec. 430.124(A)].
The disconnect for an ASD must have a rating of at least 115% of the rated input current of the conversion unit [Sec. 430.128].
Circuits containing power conversion equipment must be protected by a branch-circuit OCPD [Sec. 430.130(A)]. The rating and type of protection must be determined by Sec. 430.52(C)(1), (3), (5), or (6) using the motor’s full-load current (FLC) rating as determined by Sec. 430.6(A) or (B). This differs from the previous Code revision, where you used the FLC ratings listed in Tables 430.248 and 430.250 [Sec. 430.130(A)(1)].
Exception: You are allowed to determine the rating and type of protection using Table 430.52(C)(1) with the power conversion equipment’s rated input current where the power conversion equipment is listed and marked “Suitable for Output Motor Conductor Protection.”
Informational Note 1: Motor conductor branch-circuit short-circuit and ground-fault protection from the power conversion equipment to the motor is provided by power conversion equipment that is listed and marked “Suitable for Output Motor Conductor Protection.”
Informational Note 2: A motor branch circuit using power conversion equipment, including equipment listed and marked “Suitable for Output Motor Conductor Protection,” includes the input circuit to the power conversion equipment.
Where maximum branch-circuit OCPD ratings are stipulated for specific device types in the manufacturer’s instruction for the power conversion equipment (or otherwise marked on the equipment), you can’t exceed them even if Sec. 430.130(A)(1) permits higher values [Sec. 430.130(A)(2)].
Article 430 in the 2023 Code has a fair number of changes from the 2020 Code. Many of these are editorial in nature, with the goal of making Art. 430 easier to understand and apply — but it will never be easy to understand or apply.
To avoid mistakes, mentally separate overload protection from overcurrent (and ground-fault) protection.
These materials are provided by Mike Holt Enterprises in Leesburg, Fla. To view Code training materials offered by this company, visit www.mikeholt.com/code.
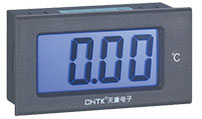
3 Phase Power Monitor Mike Holt is the owner of Mike Holt Enterprises (www.MikeHolt.com), one of the largest electrical publishers in the United States. He earned a master's degree in the Business Administration Program (MBA) from the University of Miami. He earned his reputation as a National Electrical Code (NEC) expert by working his way up through the electrical trade. Formally a construction editor for two different trade publications, Mike started his career as an apprentice electrician and eventually became a master electrician, an electrical inspector, a contractor, and an educator. Mike has taught more than 1,000 classes on 30 different electrical-related subjects — ranging from alarm installations to exam preparation and voltage drop calculations. He continues to produce seminars, videos, books, and online training for the trade as well as contribute monthly Code content to EC&M magazine.