In the early days of 3D printers, most builds used smooth rods and bearings that rode on them. But these days, printers are shipping with either V-slot extrusions with Delrin wheels or linear rails. Which is best? Everyone seems to have an opinion, but [Spencer] decided to compare them using some well-defined experiments, and he shares his results in the video below.
Common wisdom is that linear rails create a better print quality, but [Spencer] didn’t really find that much difference. He does admit, however, that he isn’t an expert on setting up linear rails, so perhaps there’s something he could have done better. He did note that the rails were quieter but that, for both cases, the noise generated by the moving rails was only a small fraction of the total noise generated by the printer. The rails were also more stable in terms of resonance. Input shaping can help overcome that, though, so it probably isn’t that important in a modern printer. Three-Axis Platform
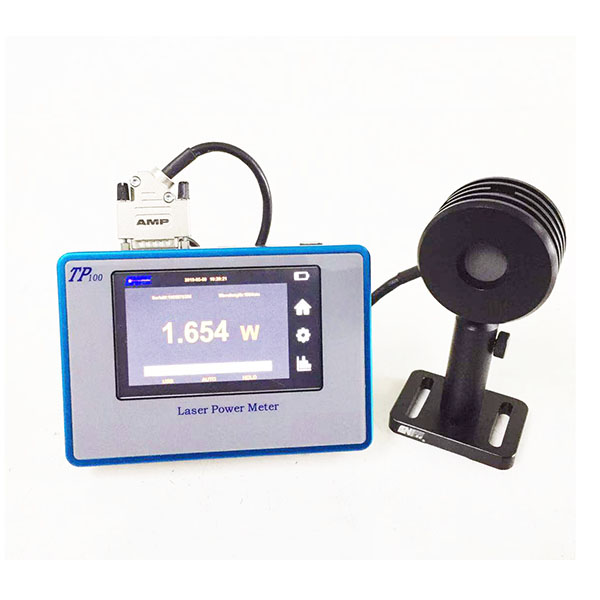
What do you think? Are linear rail upgrades worth it? Let us know in the comments. We’ve been 3D printing long enough that we are hard-pressed to complain much about any of the prints we produce today on printers that cost a fraction of what we spent on our first ones.
Of course, you could go with string. Putting rails together with or without slots is its own art form.
One problem of V-rail is, that the rubber gears wear out, or In worst cases they are not perfectly round…
And concentric nuts can be a pita.
Just trying to get them with the perfect amount of tension can be tedious, especially if there’s more than one.
I hear polycarbonate wheels help with that.
PC wheels are harder than aluminum. so you’re wearing the aluminum instead.
something’s gotta give. I prefer it to be an easily replaceable piece of rubber
Polycarbonate is not harder than aluminum.
Anonymous is right that polycarbonate is harder than (at least most) types of aluminum, but you’re also right in the sense that it wears down aluminum rails faster than rubber does.
In the real world, just because a material is softer than another doesn’t mean it causes no wear to the harder material at all- and standard polycarbonate is pretty close – about 80% as hard as 6061 aluminum (at least on the Brinnell scale).
All that said, I’m not sure the aluminum wear would ever become a problem over the lifespan of a well-maintained 3d printer; the rail/wheel assemblies I know have a way to adjust the clearance between the wheels and the rail so you can easily remove the tiny bit of play caused by wear.
Some grades of polycarbonate might be reinforced with glassfiber. Then I would assume they can abrade aluminium guides quicker than rubber.
Makes me think of the ancient Egyptians cutting stone with copper saws and/or ropes with sand.
One infamous example from cars is that small particles of something harder (EG iron/steel swarf from component wear) can get embedded in a soft material (EG aluminium carrier) and then wear a harder component (EG camshaft) that is running against that supposedly softer material due to the abrasion.
I swapped my felting wheels out for polycarbonate and the poly wears as dust vs delrin that tends to shred.
Some silicone lubricant applied to the rails really cuts this out and I’ve been running a few hundred hours on then without any wear on either the wheels or the rails. Delrin wheels were worn down after 50 hours.
Also consider how much easier it is to integrate linear rails. I designed and built a v-wheel printer many years ago and upgraded it to linear rails a year ago. The whole thing got a lot simpler and it was easier to place things without having to worry about whether the carriages would interfere.
Also, are the wheels even still cheaper? The prices of linear rails have dropped significantly over the past few years. I was pricing out a new design for a cheap cube and was originally going to do smooth rods for the z to make it cheaper but once I factored in all the parts and shipping the linear rails were actually cheaper.
Most of the time you are mounting the linear rail to an extrusion, so you would have to compare the price of the rail to just the wheels. Even then, the extrusions are like 5$/m.
If you buy directly in china the wheels are dirt cheap, like 6$ for 10 cheap and you need only 3 per axis.
By comparison halve a meter rail and a block even in china quality costs 15-20$.
These arent costs worth discussion though for the convenience of jot having to deal with rubber dust, occasional looseness and eccentric nuts.
Not 3D printing, but with laser engravers, linear rails make quite a bit of difference in the quality of an engraved photographic image.
Really? I haven’t found that it makes any kind of noticeable difference
I am not very surprised the difference is very small. Those rails with linear bearings become a big advantage when there are big lateral forces. So it makes more sense for CNC milling machines. It can also help when for example the platform for the Z-axis is only suspended from one side.
It’s also quite possible that stability / resonance is mostly improved simply by the mass and stiffness of the steel rails themselves and has nothing to do with the bearings themselves.
“Evidence based answer” with a sample size of 1.
I total trust in that.
One is better than none. No statistical strength, but a starting point for hypotheses.
And from a guy who “does admit, however, that he isn’t an expert on setting up linear rails”
No mention of metrology skills either – I suspect a machinist channel like This Old Tony or Blondihacks would be able to spot the difference and accurately measure & characterise it pretty quickly.
i’m surprised people are still talking about v-slot with the special bearings. but i also really assertively hated the youtube presentation for this video, so i must say i don’t actually know what he’s talking about! golly this content cries out for a blog post with a handful of still photos instead of seeking around a video that seems to be mostly talking head with only brief close ups that are hard to decipher.
i bought a reprap kossel (delta, 3 symmetric towers with the head on arms between them) from mixshop (RIP) a decade ago. the original specs called for an extrusion that had a v-slot, with special bearings that fit in those slots. mixshop innovated and used regular 608 skateboard bearings, with an extrusion that has an appropriate slot for them! much cheaper, and imo it’s perfect. i don’t know what this extrusion is called but it’s about an inch square, and it seems to be intentional that the groove fits the 608. it also fits the T-nuts for securing all the other components, of course.
i did not like the ‘trucks’ that rode on the rail from the factory, though. it had interference between bolt heads and the arms, such that it restricted the build area significantly. and there was no adjusting the roller tension — it was factory set by a piece of laser-cut plywood. so i built new trucks for it, with the tension set by adjustment screws.
https://galexander.org/kossel/kossel067.jpeg
i’m not going to claim it’s “as good as” anything else…my mechanical engineering is very much on a scale that runs from ‘give up’ to ‘try again’ and tops out at ‘good enough’! and this is good enough. so far as i can tell, if i was to tighten up the tolerances on this printer, the first thing to attack would be the traxxas ball joints, which have a little hysteresis (maybe it’s my fault, i’m not disparaging anyone). by comparison to that source of slop, the linear movement seems perfect.
That’s T-slot, it’s pretty ubiquitous. I made my modded D-bot with it in the places where I didn’t need V-slot (local prices were insane, v-slot was like 3x more expensive). Honestly that design looks like shit… you’re rolling steel against aluminum and it doesn’t have anything but the tiny side lip to keep the bearing from moving horizontally. If it wears down it will probably start skidding instead of rolling. But it is cheap, that’s for sure
lasted a decade in the task assigned to it :)
I’d think that a linear encoder so it can run closed loop and not continue printing misaligned after an obstruction would maybe be more useful than overbuilding the rails.
Closed loop is usually the answer. Actually I’d say always, but “always “ is sort of an open loop in its own way.
The other possibility of course is to only print after the head has moved on one direction thus eliminating lash/slop as a factor.
Anybody knows the best oil for both of these? Any oil we use will get sticky after some times. The issue we have is that we can only oil them once a year so we need to find an oil That will stay functional for one year terms.
What kind of oil did you try? Sewing machine oil never got sticky in my experience
I assemble laboratory machines for a living that have high-precision (linear) rails and we use White Lithium (bearing) grease.
Grease is thicker than oil and may look a bit filthy after a while, but it remains functional for far longer than your average oil which tends to evaporate and turn into a (sticky) residue. If the bearing is in a closed environment it can last a decade.
For most industrial bearings, “oil” is basically just used for corrosion resistance while shipping, and you’re supposed to pack the carriage with bearing grease (often lithium) when they’re in use. Sometimes the manufacturer even wants you to specifically strip the oil with a solvent before greasing the bearing as the light oil simply isn’t up to the task of lubrication.
A year is typically no problem for bearing grease, though there are of course exceptions. The real question is what kind of shear/load the lubricant experiences in use, distance traveled, temperature, and contaminants. For a 3D printer, none of these would likely be issues, except maybe travel distance.
Shell Gadus S2 V220 or similar should work great for them.
I’d like to add that the only other time oil would be used is for a hydrostatic system. Used to work for a metal forming press OEM and some of the machine models used hydro-static gibs to center the slide/ram of the press.
But, that was a system where the oil was pressurized and constantly circulating.
Rule I: never mix lubrication products. It needs thoroughly cleaning before applying a different product.
Rule II: there is a lot of dirt in the air. An open drive will attract dirt. And that is bad. So clean and reapply.
In theory a grease might not be the best solution, because it does not release (enough) oil during micro movements. But oils might need a continuous lubrication system, so that does not work well with 3d printer rails :). And we are here at a point of not so large forces, all that might not matter at all.
So grease like stuff is it.
It exists a whole line of products for permanent lubrication of mechanical components with intermittent movement or slideway oil/grease for machine tools with lots of voodoo in it.
LHL-X100, RENOLIT LI IDM 000, MOLYKOTE® G-Rapid Plus Paste is one I like much!.
Problem might be to buy a quantity for a 3d printers… They normally sell in 100 liters or more and are expensive. Might want to look for sample seller.
Lithium grease base stuff should be cheap and available.
Vactra is an oil. So no.
Also not printing, but I’d be interested to know if anyone ever dared build a CNC using wheels rather than linear rails. Particularly a more “mill” than “router” style CNC, optimised for milling small things (accurate to the same level as typical 3d prints, not to the 10s of micrometres a lathe or profesional mill gets down to) out of aluminium or even the softest steels, even if this is done with a corded palm router as the spindle. Thanks
Heck my cnc uses steel bearings on aluminium.
If those Clint as wheels. On my earliest videos. I can cut wood from stickers on the bottom of wood.
V wheels are cheap, linear rails are better objectively. Saying we have input shaping to bring the worse method up to speed with the rival doesn’t negate that linear rails are just better.. Creality uses: oh right.
Creality uses linear rods and rails in their latest machines, sometimes it pays to not be ignorant :-) K1 Series, V3 series and the new K2 when it’s released soon, all using linear rods or rails in some combination.
Recirculating ball bearing rails are a superior product in terms of rigidity, but aren’t that great in abrasive environments. Many have nice seals and wipers however. They’re also heavy (good and bad) and generally have some minimal base friction from the bearings moving through the races and grease, and the friction of the wipers and seals. Nice part is that the friction is constant regardless of load (to a point of course!) Another nice thing about the rigidity is that you can use one linear bearing in quite a few cases, and because of their superior load carrying capacity, you can get away with a frame that’s slightly out of square in many cases, because the increased stress doesn’t significantly increase friction. Of course a frame out of alignment should always be avoided, but this is the hacker community so let’s embrace the fact that we can’t always hold the tolerance we hope for.
As I said though, they are heavy, which naturally slows down printing. The quality however, will always be better.
Soo, you are basically comparing extruded aluminium profile to ground steel bearing grooves. ~0,1mm vs 0,01mm and comparable straightness tolerances for the rail.
There is huge variability with the former even when staying within spec and it is always YMMV. Clearances will change along the path inevitably and there is nothing to be done to improve things significantly.
With linear rails as long as you drill hole pattern close enough, one can align the linear rail nearly perfectly and slides will always have tight clearances and usually there are also at least a couple tighter/looser variants available from the manufacturer if needed.
Since it seems no one else has already said it:(?)
Both of the options are good enough for this application and there are other factors that affect quality more.
I’ve never even heard the “common wisdom” that linear rails are better for print quality.
Oh boy! My wheels are worn out on my ender 3 S1 Pro. Just ordered rails from gulf coast. I could have used this article 2 weeks ago. 😏
lots of text. I'll just watch the video and ignore the comments.
Linear rails vs Vslots isnt even a discussion in my mind at least for 3d printslers and other small cnc machines. No matter how perfectly you get the rollers to perform initially, they requelire so much more fuss withthe wheels wearing out. the carriage getting loose and dealing with awful eccentric nuts that the small increase in price to use liniear rails is always worth taking.
There isnt a machine for which that cost cut makes sense and isnt a budget for which wasting more time and having more frustration is worth it for that little in price increase.
This is one of those areas where people forget total syatem cost and total running cost to penny pinch in a way that will coke back to bite them.
It makes sense for the absolute cheapest printer/cnc manufacturers who do not care about their users, the longevity of the machines or anything else but the cost, but not to any user of these products.
Of course there is one exception, and it barely is, but for exceedingly large machines it can be understood that rails might be prohibitive there.
Please be kind and respectful to help make the comments section excellent. (Comment Policy)
This site uses Akismet to reduce spam. Learn how your comment data is processed.

Electric Motor Linear By using our website and services, you expressly agree to the placement of our performance, functionality and advertising cookies. Learn more