To revisit this article, visit My Profile, then View saved stories.
It all started with baby clothes. When Rosario Hevia got pregnant with her second child, she started to notice just how many children’s garments are wasted. The gendered onesies she bought for her firstborn, a daughter, were in perfect condition, but they wouldn’t suit her new baby boy. She started to focus on textile waste in her home country of Chile. Hevia’s engineering background means she is constantly adding numbers, finding solutions, and improving systems. Chile is the main consumer of fast fashion in Latin America, so the issue felt pressing on a societal level, not just a personal one. Woollen Yarn Recycling Machine

While she was holding her one-day-old baby boy at the clinic in 2018, she decided to build Travieso, a used-baby-clothing marketplace and upcycling business. A few months later, she decided to quit her position as deputy director of financial planning for Latam Airlines Group to grow her business.
As Travieso gained popularity in Santiago, Hevia soon had old damaged fabric piling up. She was receiving 400 kilograms—more than 880 pounds—of textile waste every month by the end of 2019. Hevia started researching alternatives for the clothes that couldn’t be upcycled or resold, which amounted to about 20% of the donations she received at the time. “We went to the Ministry for the Environment, the municipalities, the big department stores that claimed to recycle sustainably. Everyone simply replied, ‘We donate it.” And she insisted: “But I’m talking about the clothes in poor condition, and they said, ‘Oh, no, they’re thrown away.’” She couldn’t find any viable solution in Chile at the time.
But Hevia kept searching. By the end of 2019, she heard of an old yarn factory up for sale. That was it. She would create yarn out of textile waste for her new company called Ecocitex, a portmanteau of Economía Circular Textil (Textile Circular Economy).
Hevia’s understanding of Chilean textile waste came from statistics published by the journal Diario Financiero in 2018 revealing that Chile produced 550 tons of textile waste every year. She felt hopeful with her yarn factory. “I [have the capacity to] process 20 tons per month, so 240 a year,” she says. But in November 2021, shocking images from the Atacama desert emerged from Chile, revealing 39,000 tons of discarded clothing abandoned in makeshift landfills. It was worse than Hevia thought. The photos went viral all over the world, with international outlets like Al Jazeera and the BBC covering the heaps. “What saddened me most about this news was that the problem went viral all over the world but not the solutions,” said Hevia. It only gave her further resolve to make Ecocitex work.
In the company’s courtyard in Santiago, there are bins for dropping off clothes to be recycled and pre-worn garments for sale. The recycling costs the donor 990 Chilean pesos per kilogram—around $1.20—for clothing in poor condition without non-textile elements such as zippers, buttons, or sequins.
There’s a reason for that fee. “The only way to eliminate textile waste is to educate and involve the consumer,” Rosario says. She explains that consumers struggle to differentiate donation from recycling, which is labor-intensive: “You donate clothes in good condition, it’s like donating a washing machine that still works, but when something is broken or stained, that’s a recycling service.”
The process at the factory is quite fascinating. Ecocitex’s employees—Hevia works with Abriendo Puertas to hire some formerly incarcerated women—start to classify what will be sold, upcycled, recycled, or used as eco-fill (scraps of clothing used to fill boxing bags, cushions, or furniture). Nothing ends up in the trash, and they process about a ton per week. (They could process more but only create the amount of yarn that sustains their business relative to their current sales.)
The old clothes that will be recycled in the yarn factory are cut and separated by color. There are bundles of clothes of various colors, different tones of blue, green, and yellow that will later turn into a unique turquoise eco-yarn. That pile of color-selected fabric first goes through a guillotine and then through large, loud old machines supervised and controlled by Ecocitex’s operators.
After the different fabrics have been combined, processed, and turned into texturized bales, a chemical binder, sanitizer, antistatics, and droplets of water are added. No dying or washing processes are involved to avoid releasing toxic chemicals into the water. Hevia knows that textile industries play a big role in polluting clean water. Ecocitex’s yarn is also colorfast because it is made with clothes that have already been washed and worn.
During the final stage, a large machine turns the processed tissue into a cotton-candy-like fabric that is cut into strips, creating the first weak version of the yarn. Finally, another machine twists the resulting strands to build a stronger, finished yarn. On a recent Monday, Rosario proudly displays the final results. “I’m loving it! Each color is created by hand, thanks to that initial garment selection,” she says. The yarn is ready for new creations.
Ecocitex’s next challenge is getting more companies and brands involved to achieve a real circular economy. Hevia explains, “If we want to solve an industrial problem, we need an industrial solution.” Ecocitex’s yarn is currently sold in physical and online stores, on Amazon and Mercado Libre, and through its website.
Currently, micro-entrepreneurs are Ecocitex’s main sales force, with 67 partners—boutiques, small business owners, and designers—distributed across Chile and more knitters emerging than ever before during the pandemic. Fabiana Ávila, a 23-year-old designer, is one of these new knitters who learned the craft during confinement and is creating avant-garde knitwear using Ecocitex’s yarn. A teacher told her about Ecocitex, which sparked her interest in the product to create new pieces for her design projects. “The textile industry is one of the biggest polluters, and we, as a new generation of designers, should bear that in mind,” Ávila says. “We can continue to create and stay on trend but in an environmentally friendly way.”
Ávila works as a costume designer in Santiago, and during her spare time, she designs new pieces and knits with her mother, Evelyn Salazar, at home while watching Breaking Bad. Salazar also learned to knit during the pandemic by watching YouTube videos and fell in love with the craft. She helps her daughter create new pieces: “She is the mastermind; she’s like my boss.”
Salazar explains that Ecocitex’s yarn is expensive compared to other products in the market. A skein of eco-yarn Vanguardia costs 2,990 Chilean pesos (around$ 3.70). Salazar says that she can buy a skein of traditional yarn at certain markets for 1,000 pesos ($1.25), but she finds added value in Ecocitex’s. “You must purchase a surplus because each color is unique, and you won’t be able to purchase that exact color again. I find that brilliant!”
Despite knowing there’s a long way to go, Hevia feels hopeful. “I’m impressed by how fast we went viral. We got 163,000 followers in just two years, we’ve been on TV, we are even talking to Vogue today.” She also finds relief in knowing that more people are invested in change. “I feel that we are finally talking about the problem, and that is the first step for real change. Now we need to put words into action.”
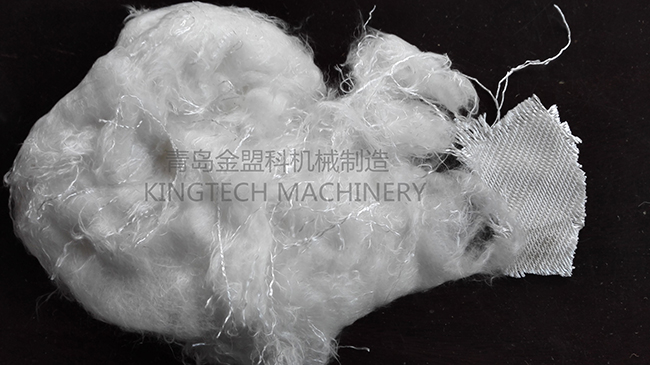
Filtration Recycling © 2024 Condé Nast. All rights reserved. Vogue may earn a portion of sales from products that are purchased through our site as part of our Affiliate Partnerships with retailers. The material on this site may not be reproduced, distributed, transmitted, cached or otherwise used, except with the prior written permission of Condé Nast. Ad Choices