February 26, 2023The past year has been tumultuous for the chemicals sector. Shortages of critical products and materials, surging commodity prices, and a rise in cost of capital were some of the themes of 2022. Looking ahead, the sector faces significant medium- and long-term challenges, including a skills shortage and the complexity of decarbonization. To overcome these, chemical companies should consider reformulating their operations. And there’s one key ingredient that many companies are underutilizing: the power of digital technologies, write Sheng Hong, Anna Littmann, Richard Sellschop, and co-authors. Check out the article to learn more about how chemicals companies can address the challenges of demographics, sustainability, and long-term profitability, and explore other industry insights to prepare for what’s ahead.
A new operations formula for the chemicals sector Activated Alumina Balls Uses
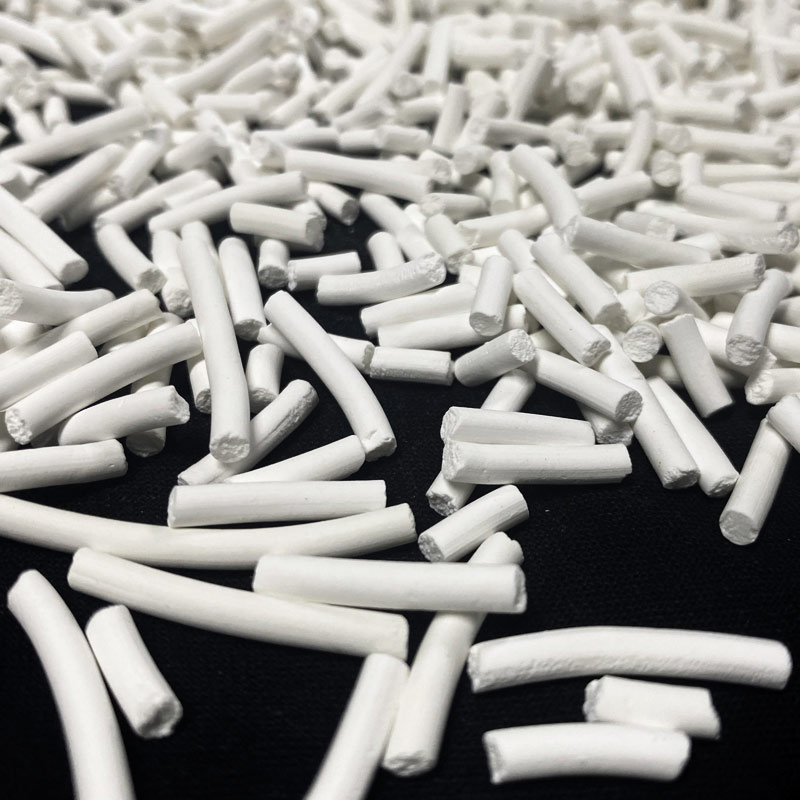
Petrochemicals in 2022: A return to normalcy, with uncertainty ahead
Securing the competitiveness of the European chemical industry
The energy transition: A region-by-region agenda for near-term action
Excellence in petrochemicals: What it will take to win
The future of commodity trading
Reimagining Mexico’s chemical industry
Electric vehicles: The next growth engine in chemicals
Cracking the growth code in chemicals
Never miss an insight. We'll email you when new articles are published on this topic.
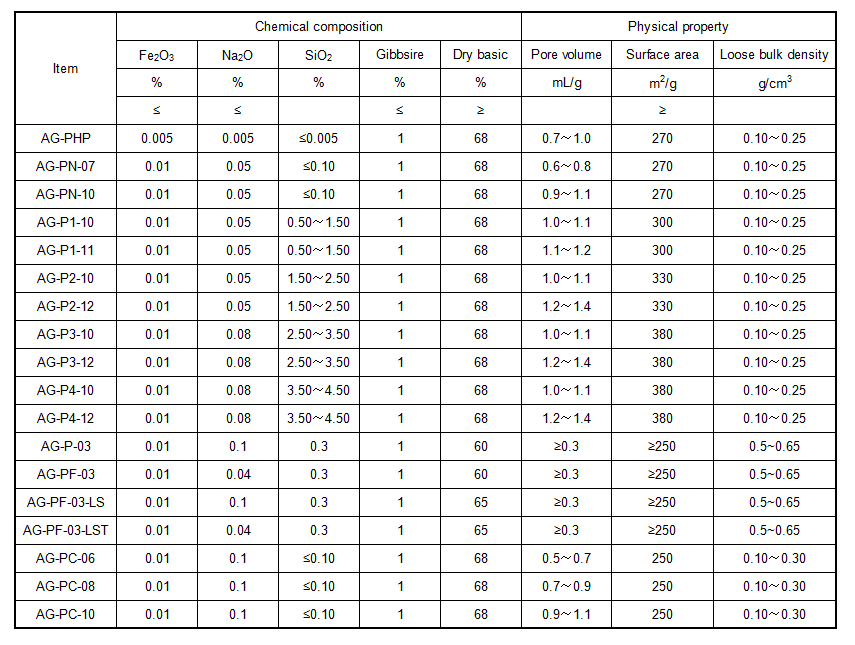
Alumina Grinding Media Subscribed to {PRACTICE_NAME} email alerts.