The lifting industry, and the lifting challenges, are as varied in Africa as anywhere else. Julian Champkin reports.
Africa has too frequently been thought of solely as a market for exporting to, receiving goods and services from elsewhere. It has, though, its own long-established manufacturers, who themselves export cranes and lifting gear; and its own longestablished service companies, who have both the equipment and the expertise to carry out the heaviest of lifting operations. Semi Gantry Crane
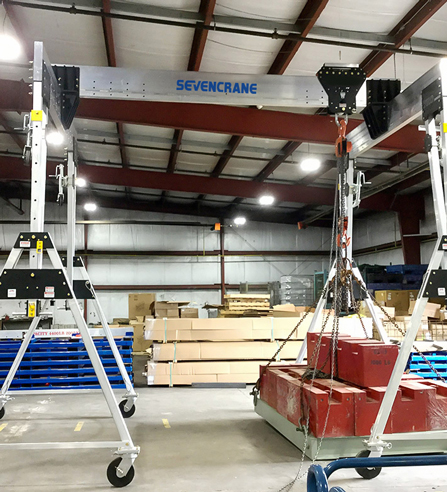
Manufacturers include RGM Cranes, who make overhead cranes and hoists in Benoni in South Africa’s East Rand. RGM has recently opened a new branch in KwaZulu, Natal, to add to their Rustenburg and Durban office and their service locations throughout the country. Morris Material Handling, also based in Benoni, is Africa’s largest crane company, making and supplying electric overhead travelling cranes, wire rope hoists, jib cranes, chain hoists and accessories. Morris was recently awarded the tender to design, manufacture and install a 100-ton engineered crane at the Vanderbijlpark steel mills of ArcelorMittal South Africa.
Vanderbijlpark Works is one of the world’s largest inland-operation steel mills. It has two blast furnaces and three basic oxygen furnaces. Production capacity is around seven million tonnes of liquid steel per annum; the company supplies over 60% of the steel used in South Africa and exports the rest to sub-Saharan Africa.
The new crane, serial number M10284, is a 37m span double girder, heavy duty slab handling machine. The slab tong fitted to the crane will be capable of handling varying sized slabs with a capacity of up to 100 tons. Operating at the hot strip mill, the crane will handle high volume of slabs and is critical to continued production at the mill. To ensure the crane is capable of feeding the mill at required production rates it will hoist at 9 m/min, cross travel at 70m/min and long travel at 100m/min; control is from a bridge mounted cabin. The completed crane will weigh in excess of 220t.
Condra, headquartered in Germiston, has a manufacturing pedigree going back more than 50 years and claims the highest local content of any African overhead crane supplier south of the Sahara Desert. It also exports worldwide. Mining, of course, is an African – and especially a South African – mainstay and mining applications account for more than half of Condra’s orders, from customers across sub-Saharan Africa and also in the Americas. Those orders are met by production at factories in Johannesburg and Cape Town. (Condra’s European market is served by a subsidiary company in Bulgaria.)
A recent Condra project has been at the Platreef platinum mine near Mokopane in Limpopo Province, South Africa. Platreef has been under development since 2020 by Ivanplats (Canada-based Ivanhoe Mines’ South African subsidiary). Production, scheduled to begin this year, will tap a 26-metre-thick flat ore body extending over several kilometres to deliver 12 megatons per annum over a lifespan of three decades, which will position Platreef among the largest platinum group metals (PGM) mines in the world. Annual yield is expected to exceed one million troy ounces of palladium, platinum, rhodium and gold, plus useful quantities of nickel and copper.
The mine itself consists of two vertical production shafts, a ventilation shaft, a concentrator, and associated supporting infrastructure. Condra has delivered electric hoists, two overhead cranes and a number of chain blocks to the project.
The electric cranes, of single-girder and double-girder overhead configuration, are for the filter building and the plant workshop; one of the machines has dustignition- proof rating to ATEX Zone 21/22 standard. Lifting capacity of the singlegirder crane is five tons; the double-girder crane will lift loads up to ten tons. Control of both cranes will be by radio remote with manual pendant back-up.
Two hoists accompanied delivery of the cranes: a short-headroom hoist for the tailings filter, and a K-Series hoist for the mill feed conveyor. Both will be used for maintenance work.
Condra was selected to manufacture the machines by consulting engineers Dowding Reynard and Associates. The overhead cranes and hoists are currently being installed.
Another Condra project is the manufacture of a service and maintenance crane for a pulp dryer line at Saiccor Mill at Umkomaas on South Africa’s KwaZulu- Natal south coast.
The double-girder electric overhead travelling crane will replace an existing machine supplied some years ago by a rival European firm, and has been designed to incorporate three hoists: a 25 ton main lifting unit and two 12,5-ton auxiliaries, all of them mechanically synchronised for tandem operation as well as offering individual lift.
The crane is intended to service all the machinery on the dryer line’s floor area of 80 x 25 metres, so its dimensions and capabilities are impressive. Its crane’s 25-metre span will deliver a maximum capacity of 50 tons and a lift height of 16 metres. Alternatively, the crane will lift up to 25 tons using the main hoist while, simultaneously, two independent loads of up to 12,5 tons can be managed by each auxiliary.
Condra undertook the contract as a turnkey project. Manoeuvrability on the dryer line floor is limited by in machinery already in place, making conventional access and installation impossible. Installation will therefore be done through the plant’s roof. Production will continue uninterrupted during the process.
All components of the new crane, including end-carriages, 25-metre-long box girders, crabs and hoists, will be lowered through a hole in the roof for insitu crane assembly.
Three Durban-based lifting subcontractors will work with Condra to install the crane. Yellow Dot Coatings has been appointed to open the plant’s roof, after which Lovemore Bros will rig all components and use its 550-ton mobile crane to luff them one by one above and through the roof opening, lowering them precisely into position for assembly by Natal Cranes, Condra’s Durban-based agent.
After installation, Natal Cranes will also oversee commissioning.
Condra’s 12,5/25,0/12,5-ton overhead travelling crane was ordered as part of a 7,7-billion rand upgrade and expansion of the mill, making it one of the biggest dedicated dissolving pulp plants in the world. Global demand is increasing for this key input in textile manufacture, food processing and pharmaceutical production.
The pulp dryer line to be serviced by the new crane is noted for a corrosive environment resulting from the use of steam-heated drying cylinders to dry the sheet-form pulp ahead of packing and shipping. Manufacture of the crane from carefully selected materials and the use of anti-corrosion finishes will afford protection. All motor and electric panel insulation has been protected to Standard IP65, while the panels themselves and all handrails are of stainless steel. Crane platforms have been fitted with fiberglass grating instead of steel chequer plate, and all crane components are coated with a special anticorrosion finish.
The crane’s load lifts are failsafe. Its three hoists are fitted with secondary emergency brakes on the rope drums to back up standard brakes on the electric motors.
The new crane will become Condra’s second to work at the plant, joining a single-girder overhead crane manufactured by Condra in 1984. Competition for the contract was keen. Five companies from Europe and Africa submitted tenders. Local content allows Condra to deliver overhead cranes with the lowest possible lifetime cost. This, and the proven reliability of Condra’s existing installation, is thought to have reinforced a competitively priced bid to secure the turnkey contract. The new crane is scheduled for commissioning early in 2024.
Among supply and service firms, Paterson Simons have been involved in West and Central Africa since 1948, commissioning and installing overhead cranes and other lifting equipment. Volta River Authority (VRA) is the national generator and supplier of electricity in Ghana. It was established in 1961 to manage output from the then newly-commissioned Volta dam, and now generates thermal power also. Pasico Ghana, a subsidiary of Paterson Simons, in the latter part of 2023 completed an installation of an overhead crane at VRA’s thermal energy plant in Aboadze, Ghana.
The crane is a 62t/15t model from Konecranes. To reduce shipping costs the crane was ‘spliced’ by Konecranes to enable containerised shipment, and assembled on site by the Pasico team before lifting into position. The crane is rated for outdoor use above the thermal plant in a harsh coastal environment and will be used for lifting the rotors, each of approximately 50t, for maintenance and repairs, and to offload containers and lift other heavy items as and when necessary.
This is the second Konecranes Overhead Crane at VRA Aboadze. The first, of similar 62t/15t capacity, was installed, also by Paterson Simons, in 2017.
In addition to the overhead cranes, over the years Paterson Simons has supplied forklifts, mobile hydraulic cranes and aftermarket support to Volta River Authority. The company also offer crane certification, overhead crane operator training and inspections across the West and Central African region.
Vanguard, based in Johannesburg, provides a lifting, transporting, moving and installation service to the heavy industry and infrastructure markets. It owns and maintains the largest fleet of heavy lift equipment in the southern hemisphere including stand jacks, and hydraulic lift systems. The company lays claim to the highest non-crane-assisted lift on the African continent, with the lifting of a 90m-long, 1,200-ton conveyor section at the First Quantum Mine in Zambia: the final position was 60m from ground level.
More recently, with the lifting and placing of the press crown onto the last press in the five-press Jier tandem line at the Ford Motor Company in Silverton Pretoria, Vanguard officially completed the heavy lifting of what is the biggest tandem line to be installed in South Africa. The fully assembled crown and lifting gear weighed in at 367t and in order to clear the tie bars had to be lifted to a height of 14.75m.
The installation forms part of a $1.5bn investment by Ford into upgrading their production facilities in the region. Vanguard’s responsibility is an allencompassing Turnkey Operation, including the complete logistics: the heavy transport of the consignment from Richards Bay to Silverton; off-loading and final positioning of the five presses and associated automated handling stations; the full installation, including all electrical and PLC programming; commissioning; and the final hand over to the client.
In association with related investments in the Silverton Development, Vanguard in the course of the next four months will install and commission a further 14 presses, three of which are even bigger than the Jier Tandem line. “Vanguard”, says senior field manager Patrick Valentine “are very proud to be part of this development in Silverton. To be entrusted with the turnkey installation from Richards Bay to final hand over of a working line to the customer of a plant as sophisticated as this is a feather in our cap. I am pleased to say that so far all has gone according to plan.”
‘Ex Africa semper aliquid novi,’ wrote Pliny the Elder around the year 70 AD: Out of Africa there is always something new.
Vanguard successfully completed a complex lifting operation to set upright a barque rigged sailing vessel, named the Europa, at Victoria and Alfred Waterfront Yard, Cape Town. The vessel, which weighs 650t and measures 44.5m in length, had slipped from its keel supports and rolled onto its starboard side during relaunching operations.
Vanguard were contracted to engineer and perform a righting operation to realign the vessel with the centre line of the track system. The restricted workable space surrounding the vessel made a crane lift impossible. Vanguard’s engineering team therefore designed a bespoke lifting solution.
The solution consisted of four hydraulic gantry systems, which were positioned over the vessel and between the masts to minimise further impact to the masts and rigging. Once the 400t and 600t capacity systems were in place at the bow, and 500t capacity systems at the stern, the header beams were lifted into position and four 186t capacity strand jacks were installed.
The strand jack system was rigged to keel brackets that had been custom fabricated for the operation. It provided a high degree of accuracy and enabled the Vanguard team to lift and upright the vessel in a controlled and precise manner. Once the vertical lift had been completed, Vanguard completed a transverse skidding operation to realign the vessel with the track system. “Vanguard were delighted to work for Resolve Marine and alongside Trinity Marine Architects on this unique project. The extensive planning and engineering work that was involved is evident in the precision of the execution,” commented Bryan Hodgkinson, Director at Vanguard. “It was a true team effort and the success of the project is testament to the knowledge and experience within the business”.
A steadily increasing order intake from general industry and consulting engineers has led BB Cranes of Cape Town to step up production to meet demand.
The upgrading of water and wastewater treatment plants in the Western and Eastern Cape is providing much of the additional business. Cranes and hoists are key to these plants.
BB Cranes, based in Rivergate, has supplied most of the consulting firms overseeing upgrades and expansion of the Western Cape’s water treatment reticulation, including the associated pump stations.
“The Victoria & Alfred Waterfront’s seawater desalination plant is currently our most visible involvement,” said BB senior sales executive Stephen Brink Jnr. “We installed a 3,2-ton single-girder overhead crane there in mid-September 2023, and also four monorail hoists with associated structures.”
Design and supply of the hoists was carried out by Condra, BB Cranes’ parent company in Johannesburg, with BB Cranes itself undertaking girder manufacture, crane assembly, delivery to site, installation and commissioning. BB will also supply local service support.
The seawater desalination plant at the V&A Waterfront is a project under construction by Proxa Water to deliver a reliable supply of potable water to the precinct, replacing dependency on city dams which have in recent years been threatened by drought.
Proxa Water’s order on BB Cranes is the company’s third, following BB’s supply of similar equipment to several Proxa projects outside South Africa
Brink said that a bigger order for the company in terms of unit numbers was one for eight cranes and hoists recently placed by an unnamed customer, to be installed at a wastewater treatment works in the Eastern Cape. These are a mix of overhead machines of various designs, a jib crane, and several monorail hoists with supporting structures.
BB Cranes recently delivered two other five-ton monorail hoists to the same customer, for new bus depots servicing Mitchells Plain, Khayelitsha, Claremont and Wynberg.
Cape Town’s shipbuilders, too, have placed orders on BB Cranes to manage growing demand. Two Oceans Marine, a manufacturer of high-end custom catamarans, is building a new factory and equipping it with two identical double-girder overhead travelling cranes to lift and position boat engines and other components, as well as the completed vessels themselves.
These cranes will be fitted with dual 2,5-ton hoists from Condra’s compact SH Series. Again, overall design and the supply of the hoist units was carried out by Condra, with BB executing girder manufacture and assembly.
Cape Town is home to two other luxury catamaran manufacturers, both of which also have BB cranes installed in their factories. An anticipated requirement is for a very large machine, an 80-ton giant overhead crane needed for construction of an ultra-large catamaran with a price tag approaching R200 million, expected to be ordered soon. If secured, this will be BB’s biggest ever crane installation. Smaller orders include two single-girder overhead machines supplied to a manufacturer of vehicle trailers.
Brink said that BB Cranes’ work to increase company competitiveness is ongoing.
“For us, the pay-off is the steadily increasing number of customers placing repeat orders in spite of an influx of cheap imported product from rival firms. One customer was this year compelled to order a replacement crane from us because of the failure of a cheaper machine,” he noted.
“That failure cost the customer downtime and lost production because of a lack of spares availability. Condra spare parts are always in stock. Pay a little bit extra at the start of things, and there will always be payback in the medium term.”

Rubber Tyred Gantry Crane Progressive Media International Limited. Registered Office: 40-42 Hatton Garden, London, EC1N 8EB, UK.Copyright 2024 Progressive Media International Limited. All rights reserved.