Since we are talking brakes this month, let’s do a little comparison of the most popular brake systems that brought us from the days of dragging a flat plate against the wagon wheel or mashing your foot down on a mechanical linkage arm that eventually either slowed the car down or gave you one really strong leg. What I’m talking about are the power-assisted brake systems we find on modern cars and trucks. Related Articles - Reading what you can’t see: TPMS sensor signals - Understanding TPMS sensor signal transmission limitations - The Average Price on an Air Filter Replacement from Mobile Maintenance Providers
These days, we don’t even consider power brakes as something that needed inventing, but merely a standard feature that we now come to expect out of our daily transportation. Well, you may not have heard the term in a while, but “power brakes” had to start somewhere. Brake Expander Wheel Cylinder

Probably the first place to look is what got it all started: Pascal’s law of hydraulics, the law of fluids in motion and how they can be used to increase force.
Pascal’s law states that when there is an increase in pressure at any point in a confined fluid, there is an equal increase at every other point in the container.
It took Pascal to open our eyes to what could be done “hydraulically” with a fluid.
Around 1918, a young inventor took the Pascal idea and applied it to brakes. His name was Malcolm Lougheed (later he changed the spelling of his name to Lockheed). In 1921, the Model A Duesenberg became the first car to have hydraulic brakes.
Although they were not power assisted, the effectiveness of the brakes was well noted, compared to the mechanical brake systems that were common at the time.
In the early 1920s, Pierce-Arrow became the first carmaker to take Pascal’s basic theory and add a vacuum assist to the hydraulic brake system. This inventive way of assisting the driver while braking is now part of our everyday driving experience. We don’t even call them “power brakes” anymore.
In 1938, there was a car called a Tincher that used air assisted brakes, but wasn’t really considered a power-assisted system. Hydrovac Starting in the early 1940s, one of my favorite types of brake systems to study is the hydrovac brake system. If you’re a connoisseur of mechanical things, this is one you’ll need to get close with. Explaining this brake system is an Olympic event. In my book, it’s one of the true “mechanical” marvels of the brake world. At first glance, there are so many things going on at the same time that it looks like it shouldn’t work, but it does.
As you apply pressure to the brake pedal, the fluid pressure is increased (Pascal’s law) to a slave cylinder and the individual wheel cylinders. As more pressure is applied, the added pressure overcomes a sliding valve that then pushes a triangular arm that, in turn, rotates valves to close an atmospheric valve and open a vacuum valve. This vacuum valve then pulls the vacuum air into a large chamber that pushes a large bellow against the valve in the slave cylinder, tripling the available fluid pressure to the wheels. Get all that?
The harder you pushed on the brake pedal, the more the bellows pushed the fluid toward the wheel cylinders. As you let up on the pedal, the internal valve started to close, lowering the vacuum pressure until it reached atmospheric air pressure.
Last year, I restored a 1956 fire/rescue truck. One of the things I had to go through completely was the brake system. I’m still amazed at how this brake system works. For nearly 30 years, this was one of the most common brake systems on most large trucks and some cars. To this day, you can still find the hydrovac system used in certain applications. In fact, rebuilt units, rebuild kits and refurbished components are still available.
As long as this system has a good supply of vacuum and clean fluid, the power brake system will do the job. Stand on the brake pedal with a lot of force and I’ll guarantee you it will put the stop on those brake shoes with a crisp jolt that can throw you up against the windshield. But the thrill for me is still watching the action of the internal parts of this mechanical marvel.
If you would like more information on this system, there are several videos and informative sites on the Internet. I also found an early 1950s military training video that explained it all in detail.
Hydroboost The next system is a hydroboost system. The big difference between this and the hydrovac system is the fact that there is no vacuum used to operate the “power” in the power assist. Generally, the power was generated by the power steering pump. In some cases, an electric motor applied the needed power to increase the pressure on the brake fluid.
In these systems, when the pressure is applied by the brake pedal, a port in the master cylinder allows the higher pressure of the power steering system to aide in the overall pressure of the brake system.
This is a great system for the hobbyist who wants a clean look or doesn’t want the bulky vacuum unit under the hood. I also see this type of unit on larger delivery trucks and commercial units.
Having less parts to be concerned with vs. the hydrovac unit makes this a very reliable system. Today, you can find these units on some production cars, delivery vans, large trucks and commercial vehicles. If space is at a premium, the hydroboost system is a good choice for that special project car.
Vacuum Boost Vacuum boost power brakes are by far the most popular type of assisted brakes. As with the last two examples, the idea is to apply additional pressure to the brake fluid, allowing less effort from the operator.
Vacuum brakes do not need a slave cylinder to add the extra push or a power steering pump to apply the pressure just good, old intake manifold vacuum. (Some diesels and small output engines used a belt-driven vacuum pump.) The principle is the same in each case, but the cost-effective vacuum booster wins out on average vehicles.
It’s a simple system that’s effective and downright reliable. The main principle behind vacuum boost brakes is to take atmospheric pressure and vacuum air and move one to the other.
Since the “atmosphere” wants to always balance the pressure, the vacuum is the “lack” of atmosphere air. So, as the plunger is pushed, a valve opens, allowing the air to move toward the vacuum section, which is turned into the added force against the brake fluid.
It’s impressive to think “air” is the real strength in the booster system. But it is. Think of it as wind moving from a high-pressure area to a low-pressure area: The larger the difference in “atmospheric” pressure, the more intense the wind. That speed is the key in making the vacuum booster so reactive to the touch of the brake pedal.
Mechanical things intrigue me; I love to see how they work and how they accomplish their tasks. These boosters are just a small part of what I find interesting in the world of automotive repair. The better I understand how any system works, the better I can make the right decisions on service and repairs.
Now in the 21st century, we have regenerative braking systems, anti-lock brakes and stability control. Along with the old standards, there are even more brake systems to study and get familiar with. Keeping up with the changes is just another part of being a good technician in today’s world.
While every day is another learning experience, I also think it’s a good idea to study the history of this automotive world. What’s old becomes new, but in a newer element. So when you see something that you believe is new and inventive, check the history books and you may find out that it’s not that new.
Tire changing is a straightforward procedure for most technicians, but the transition from ICE vehicles to EVs will introduce some changes.
As electric vehicles (EVs) rapidly transform the automotive landscape, routine tasks like tire changes will take on new complexity, requiring updated equipment and increased technician training. Tire changing is a straightforward procedure for most technicians, but the transition from ICE vehicles to EVs will introduce some changes, particularly when it comes to addressing the added weight of EVs.
In both rim clamp and pedestal tire changers, specific techniques are followed to ensure correct dismounting and mounting of tires.
To maintain the accuracy and reliability of newly programmed TPMS sensors, it’s important to keep your TPMS programming tool up to date.
Discover the benefits of TPMS for enhancing safety, fuel efficiency and peace of mind during long road trips.
Tips for diagnosing Porsche TPMS systems and performing relearns.
Tire-mounted sensors offer expanded capabilities for TPMS technology advancement.
Above all else, follow these four important steps for effective TPMS service.
The first step to a smooth ride and well-balanced tire has nothing to do with the balancer.
By performing these checks, you can avoid any misunderstandings that can lead to less than premium service.
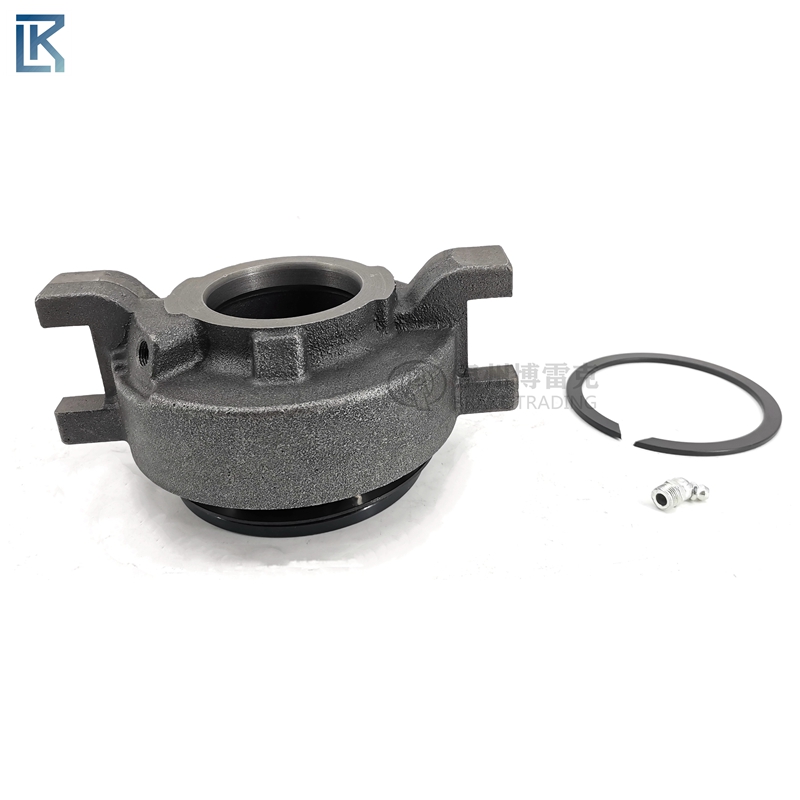
Original Piston Tire Review providing expert tire- and service-related content daily.