Most automatic machine tool tending systems involve standard, plug-and-play equipment for robotically loading and unloading CNC lathes and machining centres for turning and milling.
In an unusual application, Ott-Jakob Spanntechnik in Germany has been supplied a special variant of Halter CNC Automation’s LoadAssistant robot cells that allows deep hole drilling to be similarly automated. These are supplied in England, Wales and Scotland by 1st Machine Tool Accessories . Angle Line Steel
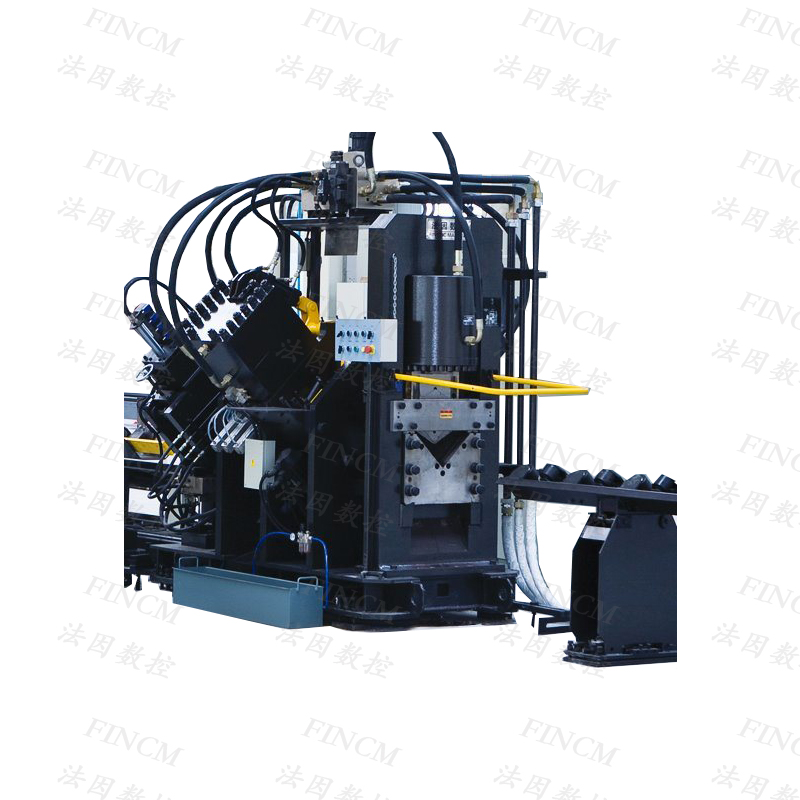
Ott-Jakob Spanntechnik is a manufacturer of manual and automatic tool clamping systems for machine tool spindles. Materials processed are mainly high-alloy steel, plus to a lesser extent aluminium and non-ferrous metals.
Four-fifths of its 2-axis lathes are equipped with bar magazines and it is always looking for opportunities to automate. This has been extended to a TBT ML250 deep hole drilling machine that produces the holes via which coolant will subsequently flow through the spindle.
Until recently, the machine was used in two-shift production where one employee, who was also busy in other areas of the factory, manually loaded the TBT ML250 with raw parts and removed the finished shafts.
With cycle times ranging from three minutes to about half an hour, depending on the size of the workpiece, the operator needed to be more or less permanently in attendance, hence the desire to automate the machine.
Series production team leader Florian Hartmann explains: "We have for some time been using standard LoadAssistant robot cells from Halter, a Universal Compact 12 and a Universal Premium 35, to feed a pair of CNC lathes. "We continue to have a positive experience with these systems, so we asked the company for a solution to automate loading and unloading of our deep hole drilling centre.
"This resulted in the supply of a LoadAssistant Universal Premium 35 having special features in terms of the design and flexibility of the cell, allowing not one but four parts at a time to be loaded into the machine."
Programming of all movements and thus the entire robot kinematics has been modified and a workpiece storage system has been installed on the left hand side of the machine at the front. The robot arm is equipped with a double-sided end effector with workpiece-specific gripper fingers that are adapted to the shaft diameters to be handled.
The robot cell provides component storage. It has a standard, 176-position grid plate able to hold shafts that are 20mm to 35 mm in diameter and 75mm to 250mm long. In addition, an 88-position grid plate for shafts from 35mm to 50mm in diameter and up to 550mm long has been supplied. Four shafts are transferred one by one from the grid plates to two buffer storage locations positioned immediately in front of the working area. To minimise machine idle time, the process is completed while the deep hole drilling machine is producing the previous four components.
The purpose of the additional transfers is to reduce the distance parts subsequently have to travel when the TBT machine has stopped and loading and unloading is in progress. When the drilling cycle finishes and the doors have opened, the robot uses its gripper to pick up the first new shaft, extract a finished component from the machining area, load the new workpiece to be drilled, and deposit the machined component into one of the same two buffer storage locations.
While swapping a new shaft for a deep hole drilled component, the system checks the position of the part in the machine and, if necessary, measures the length of the shaft again via an integrated sensor to prevent a possible collision. The unloading / loading procedure is repeated three more times in a continuous cycle, after which the buffer stations contain four finish-machined parts and four fresh shafts are in the machine for drilling.
The drilled components are transferred by the robot, to the rear of the robot cell from where they are removed by hand. Hartmann says “new territory” has been entered with this solution and optimisations have been made which is an ongoing process.
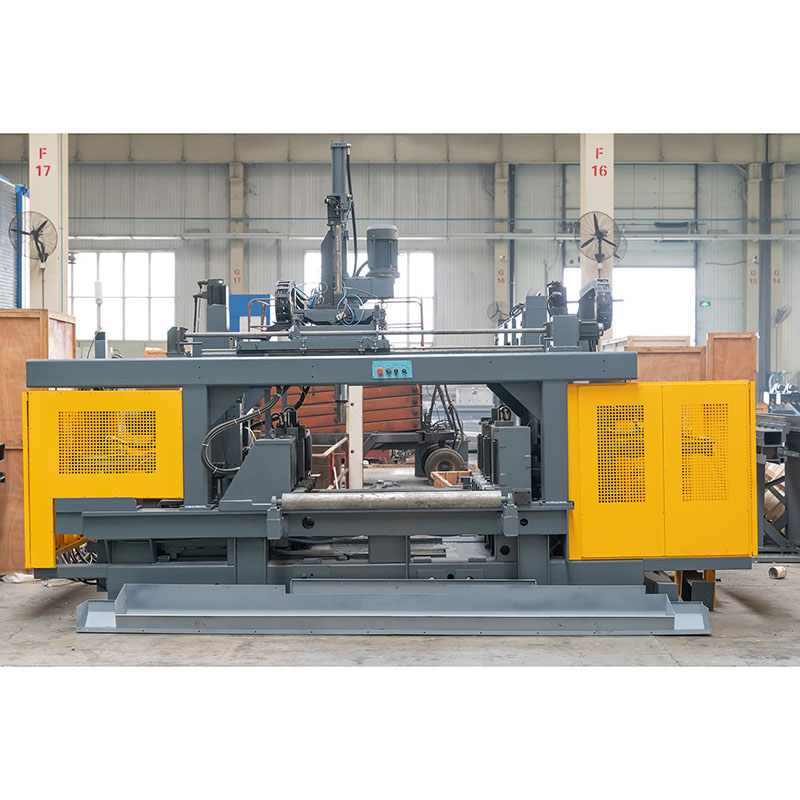
Price Drilling Machine He adds: “The average cycle for loading the machine is currently about 3.5 minutes, but we are working to further reduce the time taken. "With the robot feeding the deep hole drilling machine, the cell now produces components automatically over a single eight-hour shift and often runs an unattended shift as well, raising productivity further."