I n 2010, management at New Dawn Mining, like many miners, had been looking for ways to economically increase the output of their mines. The Turk gold mine, after nearly 80 years of intermittent production, was a good candidate for improvements. There were roughly 400,000 tonnes of historical tailings that could be ground finer and retreated, and the milling circuit looked like it would perform better in general with the addition of a fine grinding mill.
“Turk mine is a sulphide-hosted ore body,” says Ian Saunders, president and CEO of New Dawn. “You can liberate the gold and get a reasonable recovery as long as you have the technology to get it to an ultra-fine state at a reasonable cost.” But doing that had not always been possible. Optimise Production
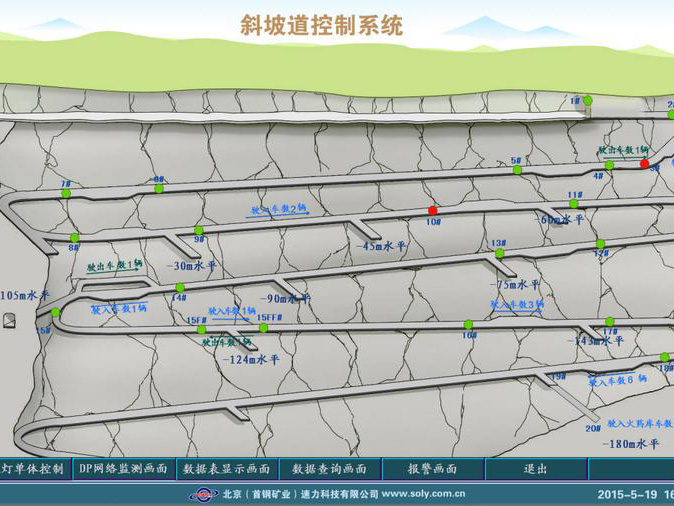
Since purchasing the mine in 1996, New Dawn subsidiary Casmyn Mining Zimbabwe has operated conventional ball mills, using 80- to 100-millimetre (mm) steel balls to grind the particularly hard ore (a 22.5 Bond work index) to 45 microns (P90). But using ball mills to achieve particle sizes that small is neither energy-efficient nor operationally efficient. Saunders explains that “with any change in parameters from the ‘ideal,’ you get a rapid deterioration of the performance of the mill.”
Fortunately, another milling technology has started to come into its own. Although stirred mills have been around in some form for years, mines have been slow to adopt them due to high capital costs and high energy consumption. A 2010 pilot project at Turk, however, showed that a new vertical-axis stirred mill, from South African company Deswik, could help recover gold from the company’s tailings at an incremental cost of roughly half the price of gold. New Dawn ordered a unit in 2011 from Knelson Milling Solutions, a joint venture between Deswik and Canadian firm Knelson.
Shortly thereafter, that partnership was acquired by FLSmidth. The new owners, wanting to properly model and optimize its new mills, proposed an on-site optimization study to get field data. Happy to get help wringing out every bit of performance from their purchase, New Dawn agreed.
Stirred mills are particularly effective for the fine and ultra-fine grinding sizes where the performance of standard ball mills typically falls off: below 100 microns. The output particle size in a ball mill is largely a function of the size of the steel balls used as grinding media. Large media can impart more energy to the feed material, grinding it effectively, but it is difficult for smaller particles to get trapped between the balls. That limits the size to which the feed material can be ground. While smaller media are able to more easily trap smaller particles, in a horizontal-axis and gravity-powered ball mill, they cannot impart enough energy to effectively grind the feed material.
Stirred mills, like the VXP2500 that New Dawn bought, overcome these problems by using smaller ceramic grinding media – from two to four mm in diameter – while using rotating discs to impart additional energy to the mix. Twelve thick, perforated discs, each slightly smaller in diameter than the inside wall of the mill, are spaced along a vertical shaft in the centre of the mill. The discs rotate through the slurry, agitating the mixture and grinding the feed material between the grinding media and between the discs and the wall.
“The advantage is that we’re able to put in a lot higher energy per unit volume into the grinding process,” says David Rahal, product manager for FLSmidth’s fine grinding equipment.
In optimizing a stirred mill for a particular use, though, a relatively minor design change can add a whole host of factors to consider. Besides the hardness and coarseness of the feed material, several interrelated parameters influence the grinding performance of a stirred mill. The disc diameter, feed flow rate, disc tip speed, grinding media type and media fill level figure into the overall performance, as do the relationships between each of these variables. These all factor into the energy required and the operating cost.
To examine the trade-offs between production and cost, statistical software was used to develop a test matrix. For each data point – each unique combination of disc diameter, feed flow rate, and so on – the parameters were set and the mill was allowed to stabilize for 30 minutes. Once stabilized, the mill feed and discharge were sampled four times at 15-minute intervals, using a Malvern Mastersizer laser diffraction analyzer to determine particle size. The four samples were averaged for each data point, and a statistical analysis was performed on the results to isolate the effect of each parameter in terms of specific energy consumption (energy usage per mass of throughput, or kWh/t).
Despite some logistical issues native to underdeveloped areas, FLSmidth’s engineers got most of the data they were looking for. The study indicated, for example, that larger disc sizes were actually less efficient – too much power was being transferred to the wall of the mill. In response, New Dawn reduced the size of the discs at Turk from 950 mm to 920 mm, and FLSmidth has since decreased the disc diameters at other installations, too.
Further, with no noticeable difference in grinding efficiency between different tip speeds, the Turk mill is now running at a lower tip speed of 10 metres per second to reduce wear and power consumption. The mill is also using lighter, or less dense, grinding media, because this allows the mill to be filled to a greater volume, increasing throughput.
With all the changes recommended by the study, the stirred mill now contributes about 400 grams of gold per day from re-treated tailings to the roughly 1.45 kilograms per day of total production at Turk. Saunders expects the re-treatment program to run for 36 to 48 months before exhausting the supply of historical tailings. After that, New Dawn intends to repurpose the mill into the main grinding circuit at the mine. By altering the primary ball mills to coarser grinds and letting the stirred mill work in its fine grinding “sweet spot,” the plant should be able to simultaneously increase feed flow rates and grinding efficiency.
“The addition of the stirred mill [to the main grinding circuit] could increase capacity by 60 to 70 per cent with no additional capital costs,” says Saunders. “That fundamentally changes the economics of the mine.”
The real-world data FLSmidth collected, meanwhile, is being used to refine the company’s models and improve its understanding of how to design and optimize its stirred mills. Some of the trends discovered, like the effect of disc diameter, are immediately applicable to other sites. Others may still require on-site optimization. Saunders seems perplexed that more companies have not jumped on emerging technologies like this sooner: “I think the only differentiator [in terms of value] between companies these days, with the [decreasing] quality of ore bodies, is that you’ve got those that are okay to think out of the box a little bit and look at these innovative technologies, even though there is an element of risk that it won’t perform.”
There is no doubt the future of mining is automation. But what does that look like, and how will we get there?
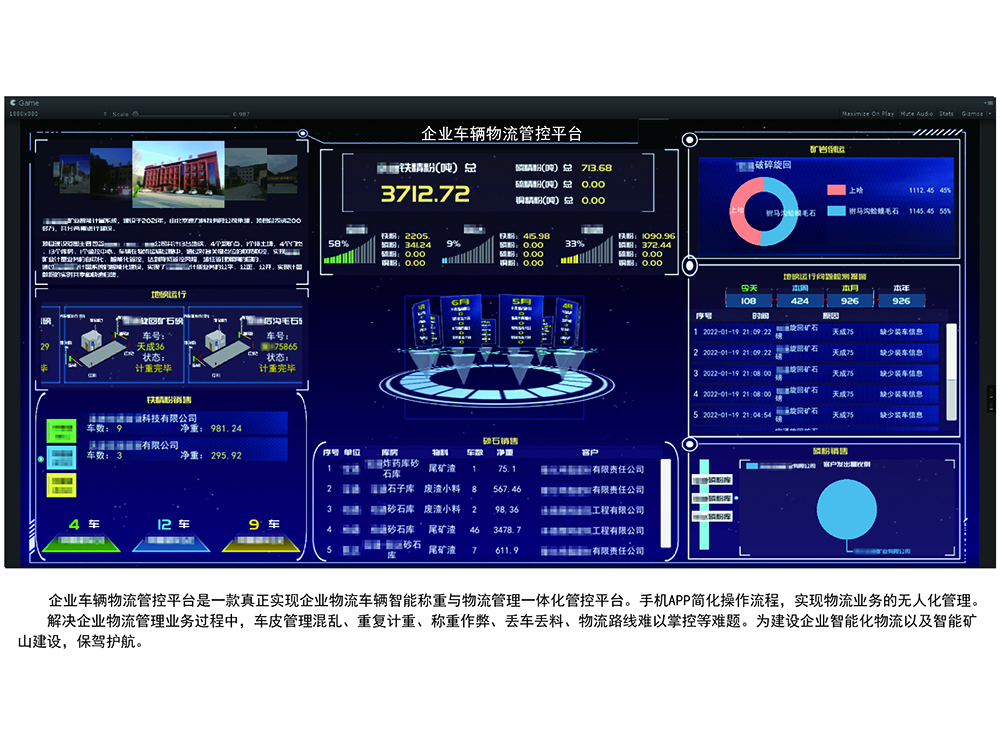
Variable Cave Production Thickness Buoyed by pressure to cut costs and improve recovery, new flotation technologies are on the rise