With last week’s introduction of the new Toyota Tacoma pickup and the previous week’s introduction of the new Ford Ranger truck, we have now seen two examples of manufacturers who are offering both coil and leaf spring rear suspension versions of their vehicles. The two suspensions are very different and require very different frames to attach to, so why would any manufacturer choose to offer both? Why not just offer one and call it a day? Let’s look at the differences between leaf springs and coil springs to find out.
It’s hard to pinpoint the first use of leaf springs in history because if you think about it, a bow and arrow is really a leaf spring turned vertical, but the leaf spring as we know and love it first showed up in 1804 in a patent by British inventor Obadiah Elliot. Prior versions had been in use since around 1750 on carriages used by the French aristocracy, and since they provided such a superior ride, by the end of the 18th century, most carriages had them. At that time, the springs were fully elliptic, meaning they were essentially two leaf springs stacked on top of each other like this: Truck Small Spring Pin
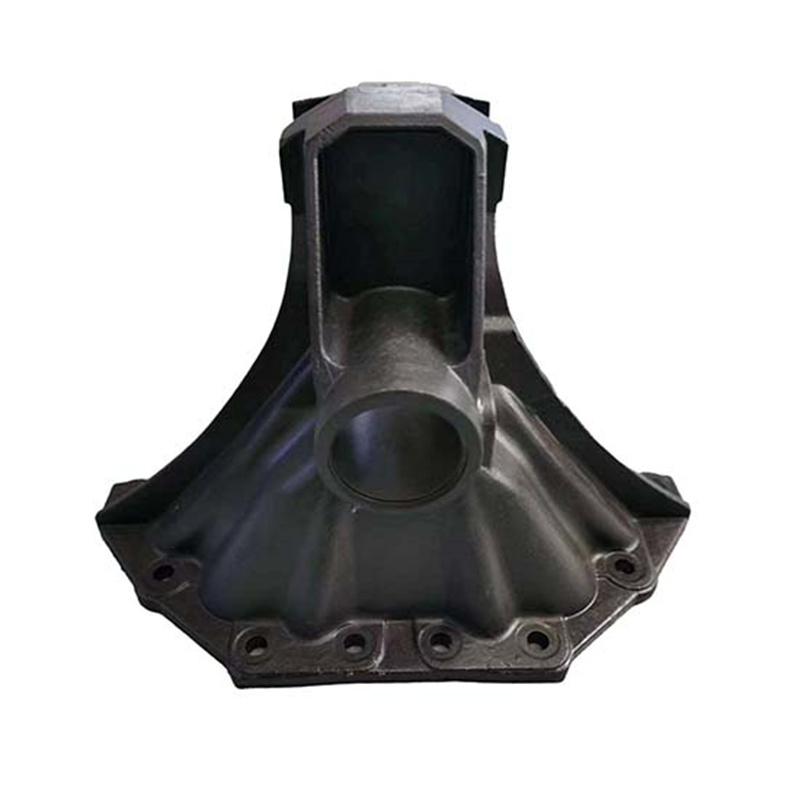
Many different variations of leaf springs were tried. Here is one that has a 3/4 elliptical spring:
Look closely and you’ll see that the end of this leaf spring is attached to the end of another leaf spring that spans across the carriage. These guys were throwing anything out there to see if it would stick. Today’s leaf springs are semi-elliptical:
There’s a single bolt that goes through the spring “eye” on each end. One bolts one side of the spring directly to the frame, the other bolts the other side of the spring to a “shackle,” which allows the fore-aft length of the spring to change as it flattens under load and bows back when the load lets up. Here’s a look at a shackle, via our friends at Quadratec:
The spring is fastened roughly at its center to the axle-tube via U-bolts shown in silver here:
As the industrial age progressed, leaf springs would find their way into many other applications. Trains used them, for example, and still do today. When automobiles first came on the scene at the end of the 19th century and early 20th century, they started out as simply motorized carriages, including the leaf spring suspensions you’d expect to find on a typical carriage. Henry Ford’s Quadricycle used fully elliptical springs on the front axle as did the Benz patent wagon for which Carl Benz filed a patent in 1893 (see below). Leaf springs would be ubiquitous for the next 50 years for both front and rear axle applications before slowly being replaced by coil springs on front axles starting in the 40’s and 50’s. Leaf springs stayed popular in rear axle applications and are still used today in most pickup trucks (that’s the new Tacoma’s rear axle above).
So, what made them so popular and why is a 250+ year old technology still being used today? The simple answer is that leaf spring suspensions are cheap and they work. In the basic leaf spring suspension used on so many pickup trucks today, known as the Hotchkiss suspension, the leaf springs form the entire suspension aside from the dampers. The springs locate the axle as well as hold the vehicle up.
This makes a Hotchkiss suspension, like the one above on the new Ford Ranger, extremely cheap. There are no linkages, ball joints, or control arms. Everything is contained within the springs themselves, and the springs are made of simple strips of steel clamped together with U-bolts. There are two bushings on each leaf spring and two leaf springs per axle. It doesn’t get much simpler than that.
While an axle held together with leaf springs may be simple and cheap, it doesn’t offer the suspension designer much flexibility when it comes to ride and handling. Leaf springs take up a lot of space, and as cars developed in the 30’s and 40’s to include independent front suspensions (a basic example of which is shown above), the use of leaf springs in the front slowly stopped. There just wasn’t room for these long springs up there and there wasn’t a good way to attach leaf springs to these newfangled independent suspensions. That’s not to say it wasn’t tried. Mercedes used a pair of transverse leaf springs in 1938 to act as both springs and upper and lower control arms.
And the classic Fiat 500 did something similar with the lower control arm:
Oh, and just for fun, here’s an Autobianchi: You can see that the spring isn’t really taking place of the lower control arm (the ends of the spring are clamped to each lower control arm), but it is acting as the spring for both the rear wheels:
This type of setup didn’t last long though. Over the years, the typical upper/lower arm front suspension with coil springs came to dominate the industry due to that setup’s versatility and tunability, and soon leaf springs were relegated to rear axle use only. Then, as independent rear suspensions became more prevalent, leaf springs were phased out of cars altogether. There were some exceptions: the Corvette used a transverse leaf spring in the C2 through the C7 and Volvo still uses one in the XC90 today. Check out the Volvo’s here:
The main difference is that the later Corvettes and Volvo use springs made not from the usual steel plates, but from various composites. This change was done to combat the biggest problem leaf springs have which is friction.
A leaf spring is just a bunch of bowed steel plates stacked atop one another with a pin (bolt) near the center holding them together, with little friction pads between the plates at the ends. It’s not really important to this discussion, but here’s a look at those friction pads:
As a leaf spring flexes, the steel plates that make up the spring have to slide against each other. This sliding causes friction, and any time you have friction, you also have something called stiction. Friction has an odd property which is that the amount of friction between two objects is different when the objects are stationary vs when they are moving. When two objects are sitting stationary against each other, there is what is called static friction between them. But when these same objects are moving against each other, the friction is called kinetic friction. The odd thing is that kinetic friction is always lower than static friction; this means that the force required to start an object sliding is greater than the force needed to keep it moving.
How this impacts leaf springs is that when the spring is sitting still, the plates are locked together by static friction and the spring doesn’t want to bend. Once a force big enough to break through the friction comes along, the plates will start to slide against each other and allow the spring to bend. Once bending (and sliding) starts, it takes less force to continue bending the spring. This translates into a kind of stickiness in leaf springs. They tend to “jump” instead of deflecting smoothly. You can feel this in a slightly jerky ride that leaf springs have. Not a problem for the back of a pickup but not good for a luxury car, for instance. Also, all that movement between the leaves will eventually mean squeaks and groans develop. The aforementioned leaf spring pads/isolators at the end of leaves are there to help reduce this.
Volvo and Corvette solved this problem by using a spring made out of a single leaf, called a mono-leaf, which avoids the sliding issue.
There is another thing that we need to discuss when it comes to leaf springs: axle wrap. When engine torque tries to accelerate a vehicle by rotating its axle shafts, it at the same time tries to rotate the axle housing in the opposite direction. Since the axle housing is being held in place by the springs, the torque twists the springs into an “S” shape like this:
Here’s a video of it in action:
If the engine has enough torque to break traction, the spring will then snap back straight. When the tire regains traction, the process starts over again. In bad cases, this cycle can happen several times per second and cause a massive vibration or “hop” in the axle. Drag cars want to avoid this.
The exact same thing can happen under braking but in the opposite direction.
Invented back in 1763 by British inventor R. Tradwell (yes, those Brits were clever, weren’t they), coil springs didn’t really show up in cars much at all until the late 30’s and 40’s. With the advent of independent front suspensions, it became clear that leaf springs wouldn’t work, so an alternative was needed, and coil springs fit the bill perfectly. They are easy to make and don’t take up a lot of space. On top of that. It is easy to make a coil spring softer or stiffer or longer or shorter to suit your needs.
Coil springs don’t suffer from the same friction issue that leaf springs do since there aren’t multiple pieces involved. As a coil spring compresses, there aren’t parts of it sliding against each other. This means they provide a much smoother ride.
The downside is that coil springs can only do one job. They provide a force when compressed or stretched. That’s it. Nothing more. They cannot also be used to locate an axle so if you want to use coil springs in a suspension, you have to provide some other means to keep the axle in place. Control arms and links provide this function, but this means more parts and that costs money.
Before we can decide which of these is better, we need to know how each affects the way the vehicle rides and handles. I’ve already mentioned the effect of friction in leaf springs on ride but are there other things we need to consider?
Since leaf springs do the job of locating the axle, their stiffness is a factor in the lateral stiffness of the whole axle, and lateral stiffness is very important to good handling and steering response. A softer spring will be able to bend more in all directions which means less lateral stiffness, although there are things we can do in the design of the spring to partially offset this. In a coil spring suspension, the lateral stiffness is a function of the links, especially if there is a Panhard rod or Watts linkage, and is completely independent of the spring stiffness.
When the body and frame of a vehicle with leaf springs rolls in a turn, or when the axle rolls over a single wheel bump, the spring has to accommodate the angle difference between the axle and the body/frame. Since the spring is rigidly attached to the axle (via the U-bolts shown earlier), it wants to stay at the angle of the axle (i.e. it wants to remain clamped flat against that axle; see oversimplification below), but since the ends are attached to the frame, they want to stay at the angle of the frame. The result is a twisting of the bushings at each end where the springs bolt to the frame via the spring “eyes” and a twisting of the spring leaves where they are thinnest.
This twisting resists the body roll and puts additional stress on the rubber bushings in the leaf “eyes” that the two bolts go through. Bushings can be designed to accommodate twisting but these same bushings have to provide the lateral stiffness of the axle as well and these multiple functions mean compromises have to be made in their design.
When the body of a vehicle with coil spring suspension rolls in a turn, there is a similar angle difference between the axle and the body but coil springs can more easily bend and flex to accommodate the angle. Think of the spring from a ball point pen and how easy it is to bend it. A car spring is of course much harder to bend, but you get the idea. The bushings in the links can also be a simpler design since they only have to resist twisting and compression. There is never any force on them trying to push the bushings sideways.
In my life as a suspension designer, I have always been a proponent of separating functions and giving each part as little to do as possible. When you ask suspension components to do many different things, compromise becomes inevitable. If you can separate functions into specific components, you can design each component to more optimally perform those functions. For that reason alone, I prefer a coil spring suspension because I am not asking those springs to be more than just springs. Let the links do the job of locating and controlling the axle. That’s what they are good at and it gives the designer much more flexibility in how the axle performs.
Now let’s get back to what started this discussion in the first place. Both Toyota and Ford have decided to offer their new mid-size pickups with both a leaf spring and a coil spring rear suspension. In the case of Ford, coil springs are only available on the top end Raptor version while it looks like Toyota is offering it as an option although it is not yet clear if that option will be available across their range.
Pickup trucks have historically been extremely profitable for manufacturers, and they will do anything to protect those profits. In fact, if you took the Ford F-series line and made it a separate company, it would be one of the largest and certainly one of the most profitable companies in the world. Anything that adds even a few pennies of additional cost to these trucks must be fully justified and shown to add to the profitability of the company in the long term. Dodge made this calculation many years ago when they made a coil spring rear suspension standard in their pickups. They knew they needed to compete on a different level with Ford and Chevy and decided this would set them apart. So far it’s been successful for them.
Ford and Toyota don’t need to set themselves apart though. Toyota has dominated the mid-size pickup market for years and Ford is no slouch with the Ranger lineup. They must have had good reason to offer a more expensive suspension in their vehicles and I think those reasons are twofold. First, they know a coil suspension offers better ride and handling and they can advertise that to their customers. Second, these suspensions are either optional or part of a more expensive package so they can charge extra money for them. This takes the profitability issue off the table. Make an option desirable to the customer by offering them some additional value + charge them extra cash for it = money in the bank.
the Coils out back on a smallish truck also allow for less overhang out back. Better departure angles and what not. IFS up front is less flexible, but the springs out back certainly increase flex opportunity depending on a few things.
The off-roaders say you absolutely need coil springs. Articulation, man! But then there’s Rory Irish’s Trail Mater, leaf springs front and rear, rescuing the “wheelers” around Moab.
I like working on leaf springs because, unlike coil springs, they won’t try to kill me.
If you want to see a fun and extreme example of axle hop – watch Bullet – when he hits reverse and stands on it in his Mustang, you can watch the rear wheel bounce and oscillate as the springs wrap and unwrap – pretty graphic example
Thank you for reminding me of one of my favorite cartoons from my childhood (so long ago), “Gerald McBoing-Boing.”
I was baffled when I first found out that brand new cars were still using leaf springs, I’d assumed they’d been abandoned in the 60’s.
Should I lubricate the leaf springs in my ’64 F100 crewcab? I happen to have run across a grease gun fitting that appears to be designed for lubing them through the hole in the leaf.
About 5 years ago, an authentic Shelby America Cobra came into the shop I was working at for a tuneup and I was quite surprised that the front suspension utilized an inverted transverse 6 in. thick stack up at center leaf spring.
Now if I could just work myself up to care about trucks then I might care about coil springs on trucks.
Back in the 60s, the Chevy half ton pickups had coil springs with long trailing arms and the GMCs were leaf springs. (This was when there was much less commonality between the divisions and they used different engines also). The rear suspension used on Nascar Cup cars for many years were derived from this and the trailing links called “truck arms”.
I remember my dad’s C20 chevy having trailing arms and coil springs. I guess they wanted to cheap out during the malaise era and go back to leaves.
If you want to be really confused, look at the torsion springs on ’60-62 GM trucks. Cool as hell, ride fantastic, easy to lower (or raise if that’s your thing), but not a ton of aftermarket support. Short lived because it supposedly infringed on some patents or something.
The Nissan Patrol Ute has been offered in leaf or coil spring in Australia around 18 years ago. I’m not in that scene, so I’m not sure how different the chassis are between them.
Regarding axle wrap, 60s/70s Chrysler products located the axle forward, about 1/3 the distance from the front eye instead of 1/2 (or centred). This made axle wrap much less likely, I’ve never had it happen in my Charger even with hard launches.
In the US we had something called “traction bars” or “ladder bars”. They were additional solid pieces that mounted under the leaf springs and were designed to prevent (or at least minimize) axle wrap and the attendant wheel hop. They often used the existing u-bolts (or included replacements) to bolt on under the axle and were attached to or near the front shackle: they allowed the suspension to pivot and operate normally, but were rigid and would prevent any changes to the distance between the axle and front shackle, if that makes sense. When the axle wraps and the spring becomes S-shaped, the front-to-back lengths of the spring halves will change.
Here’s a pic that should describe them a bit better than I’m doing: https://www.umiperformance.com/home/wp-content/uploads/UMI-Traction-Bar-Promo-Image.jpg
(No connection with the company – found it via GIS)
I think the owners added them to every late 1960s/early 1970s Camaro and Chevelle.
Yeah, everyone who was 20 and had a Camaro had those things on it. (Though I usually saw square ones.)
Yep, the square yellow ones were very popular.
Yellow was more visible, so people could easily see how bad-ass the car was. 🙂
Trucks are just becoming cars. They got popular and trendy because everyone wants to look adventurous these days, especially so for the kind of people who will never take them off-road. These people buy them and realize they actually kind of suck as road cars, like Wranglers, because their primary purpose is not to be a comfortable road car. The focus is on their utility or their off-road capabilities. So now we see truck prices skyrocketing. They’re adding comfort features that have long been on normal road vehicles, like coils and nice leather seats, or gimmick features like multiple silly touchscreens. I’ve rolled my eyes for years at people buying trucks who will never use them for more than their spring mulch run to home Depot, then spending the rest of the year with an empty bed getting absolutely rocked over potholes. Now, they’re just paying more for an oversized car with a huge storage area.
So what perfect car do you drive?
He doesn’t have to, but I bet he drives something more in line with his circumstances than the folks he’s commenting on. I see the same thing he does, people driving loaded trucks that have never seen a day of work, the beds are spotless. Now if someone wants to spend and drive that, more power to them, but I’ll roll my eyes.
The answer is always a minivan. Or a Miata.
Or both. I’ve got my daily fun car, and a minivan for camping/hauling stuff. It’s a perfect combo.
It’s a Golf. Want a fast car, Golf R or GTI. Want a cheap car? Just find a second hand one. Need to transport a lot? Get a Golf estate (wagon).
My answer is a Miata AND a truck. Trucks are just better for greasy car parts and manure. And my significant otter likes to garden.
I drive a Honda Ridgeline Pickup Truck. It has Rear Independent Suspension coil springs. With Unibody construction and Rear Independent Suspension. The ride quality and handling is the reason most people buy Ridgeline. The midsized pickup truck ride especially is not good. People put up with it. Tacoma and others tow more and better off-road. But on road or road imperfections like potholes, broken pavement,expansion joints in highway,washboard road. The Ridgeline would give better ride. Rock crawling and moderate off-roading Tacoma and other competitors way to go. But majority of their buyers are not off-roading. Ram 1500 coil springs Air Suspension So these manufacturers are trying to improve ride quality in pickup trucks. The laughed at Ridgeline and still do. They call it a city truck that is stupid. On the highway or city it’s hard to beat it’s ride. The tarmac is its playground.
I’m a big fan of the ridgeline actually. Buddy has a first gen and it’s been a tank. It has enough towing, offroad ability, and bed space for 90% of scenarios, with far fewer compromises to daily use than a typical truck. This really is the answer. I understand that size is a big part of the truck vibe, and I get that some people want the look of a larger, boxier truck, but they are absolutely sacrificing fuel economy and ease of driving in parking lots or in narrow lanes.
I use my Ram 2500 diesel as a “truck” quite a bit plus its my daily driver. I have 16k miles towing my 12k lbs 5th wheel which doesnt include all the times I’ve had the bed full with stone, concrete, etc.
Even though it has rear coils, it rides pretty rough in every day life with the bed empty because the rear axle can handle 6000 pounds. But once I put a ton of stone in there or hook up a 5th wheel, the rear squats significantly due to the coils. I had to install lift assist devices to prevent it from squatting so much. Just ironic that putting coil springs in a heavy duty truck to “improve ride quality” can turn out to be a big PIA if you actually use it as a truck a lot.
Nevermind. Answered my own question.
I can definitely see that as far as the coils. But it sounds like you’re someone who uses your truck for what a truck is actually meant for, and you have to accept the compromises because it’s a necessity. My original comment isn’t directed at you at all! Same for anyone who actually takes their 4wd car offroad or otherwise uses their car for its intended utilitarian purpose as a vehicle.
Wow this is nearly a cut a paste of hundreds of Jalopnik comments on every story about every 4wd vehicle.
I know people on here shit on big trucks a lot. I don’t mind trucks and fully understand the appeal of a vehicle with so much utility, size, etc. My original comment wasn’t aimed at anyone who actually takes their 4wd car offroad or otherwise uses their car for its intended utilitarian purpose. True truck people/jeep people etc have always understood there are downsides like road noise, firm ride, etc and accepted it, but as they got popular, you now have the stereotypical sorority girl who gets a white jeep and hates those things about it. So now the market has started to cater to them, and these formerly utilitarian vehicles have become nearly luxury at this point. I’m the owner of an awd subaru crosstrek with an offroad setup as my daily, living in a beach town. I thought I’d have more opportunities to use it offroad, but I’ve found myself putting up with harsher ride quality, louder ride, and worse fuel economy for just a couple days a year. So I’m selling it for a better daily.
I agree with you on people using trucks as essentially commuter cars. I’ve always preferred small compact cars like the 3 door Yaris I had for 10 years or sports coupes. I never wanted a truck but eventually got one from my company. I work remote so not much commuting in it but I was shockingly surprised by how much I like it. I live in Texas and it’s quite nice to see over a car when using a right turn lane. It’s also nice to see a traffic light when you’re driving behind a large SUV or truck. The back seats are mostly occupied by my two dogs and 4X4 has come in handy at least once a month since it floods or snows/ices the areas I do drive. I have a bed cover and I really like having the ability to lock up everything in there when I do road trips every other month. I had a temp vehicle before that was an SUV and someone broke into it to see what was under my cargo cover, they only stole a small bag of clothes. I’ll probably switch back to an SUV because the high ride is an advantage in a city that is mostly large trucks and SUVs who regularly run stop signs and traffic lights. Overall, I now believe trucks are fantastic if you need an all-around vehicle that you plan to use as engineered. In an ideal world, I would love to now have a midsize truck for road trips and an EV for weekly use.
Fair enough! Especially since it sounds like youre taking advantage of the utility. And I absolutely get the ride height thing, my weekender is an S2000 so you’re basically on the ground and the limited vis can be annoying at times. If you’re using a truck for it’s intended purpose, then you’re someone who should have one. The folks I was really poking fun at are those who never use them for what they’re built for, and are just accepting all the downsides of a truck simply to have a truck, or look trendy.
A slightly off-topic question about rear suspensions on pickups: I live in Australia and have always known commercial pickups like the Hilux to have bouncy, skittish rear suspensions when empty and feel like a pogo stick over rough roads and speed humps unless loaded.
Last year I went to the US and rented a U-Haul Chevy Silverado, and surprisingly the ride was so soft, almost luxurious, with a slightly unsettling amount of body roll and much less bounciness in the rear.
Is this because of the greater mass of the Silverado, the suspension design, or just market preferences?
Design and market preference. Your Aussie Hilux is designed with rear springs that will ride better with a heavy load in the bed. The American pickups are designed to ride well empty because thats how much American trucks spend most of their time.
They don’t ride that well empty full sized ride better than midsized. As said in my other post. We have a Honda Ridgeline Pickup Truck. The Unibody platform with Rear Independent Suspension.
I’m sure there’s a much longer list of relatively recent cars that used a transverse leaf rear suspension, but I believe quite a few of the GM W-bodies can be added to that list.
Also, let’s not forget torsion bars.
It took me a lot of starring to try and figure out how the suspension worked on the Toyota Mega Cruiser. I was expecting big ol coils like the HMMWV. Turns out it used torsion bars. Makes all the sense in the world now that I know.
I have a few more thoughts.
I haven’t owned a leaf car in a while, and I’ve done most all my wrenching on coils or struts. Sometimes I’m a little jealous of leaf guys. A lift is SOOO much easier on a leaf vehicle. More lift? taller springs, or even a spring block (btw, that Ram dude with axle wrap…less spacer block my man.)
While it sounds that easy with my coil spring double live axle vehicle…it is not. Here is the list of things I needed to raise my vehicle 2 inches and keep it driving like stock(ish).
To say nothing of the other stuff like extended brake lines.
Thing my friend had to do to lift his Tacoma 2+ inches?
Thats it. Sure the kit for the springs comes with new u-bolts and such, but yeah, not much to it, especially since you can correct for pinion angle pretty easily and you don’t have to worry about lateral location.
Yes, it is much easier to lift a leaf spring vehicle (don’t forget that your Tacoma friend will also need longer brake lines to reach the lowered axle) but the end result will be significantly better in your case than his. The RAM dude may have gone overboard on his lift but the issues he has will still be there in the Tacoma, just not quite as bad. Lifts of any kind require a lot of care though. It’s almost impossible to not screw up the suspension geometry no matter if you have leaf or coil springs.
tell me about it. I’ve learned slowly what it takes to do it right and I still have a few issues to iron out.
Did you correct your headlights?
XJ Cherokees were a piece of cake to lift. Up to 3 inches you didn’t need anything besides springs and shocks. Over 3, you started to get into t-case drop or SYE, brake lines and drop pitman arm.
Wranglers can’t take much lift because of how short the driveshafts are.
Don’t forget the drop Pitman Arm.
And to lift a Wrangler or a Gladiator 2 inches…….blocks of rubber covered plastic-(or you could replace the control arms, shocks, and springs as I did… in the front- Spacers in the back on the leaf springs) BTW lifting a taco is about 3x more expensive than a Jeep.
Also, all that movement between the leaves will eventually mean squeaks and groans develop.
SO MUCH NOISE! Oh man I hate driving behind my friends Tacoma and Frontier off-road. Constant noise.
Since leaf springs do the job of locating the axle, their stiffness is a factor in the lateral stiffness of the whole axle, and lateral stiffness is very important to good handling and steering response.
Lateral stiffness also plays a big roll in trailer stability. More lateral stiffness, more stability. Probably why trucks have hung onto them for so long.
option although it is not yet clear if that option will be available across their range.
Standard on TRD sport, off-road, PRO as well as Trailhunter and limited. It will only be SR grade and 2wd models (including pre-runner) that get leaf.
They must have had good reason to offer a more expensive suspension in their vehicles
Reason #3. TNGA-F is a shared platform between many vehicles and types, from Flagship lexus to base level Tacoma. It only made sense to use a common type. Why they even included a leaf spring Tacoma I think is the real question. My guess is because it will be the payload leader.
Toyota may have used a “shared” platform but I feel very confident that the back half of the pickup frame has very little commonality with the back half of the SUV frame, no matter the platform. The requirements of a pickup box and an SUV “box” are just too different.
I’m sure there are differences, but there is a ton of commonality. Even the frame pitch is the same between Tundra, Sequoia and Tacoma. Toyota really wanted to reuse the rear end on these trucks. I’d love to know a little more about what axle Toyota is using because it could be common across all trucks now.
But like the Australian frame the body of the SUV provides insulation extra weight, and passengers or groceries etc provide the extra weight to dampen the noise.
Lateral stiffness and the overall way trailer weight is transmitted through the suspension to the axle is a lot more straightforward and lest costly to engineer with leaf springs. For a typical pickup, you have the trailer weight transmitted to the frame, and from the frame, through four points (ends of the leaf springs) to the axle, all spread through a nice, big rectangular area just by virtue of the way leave springs are hung. Towing forces are fairly widely distributed through the frame and leaf springs. And the whole suspension package stays simple and relatively lightweight.
With coils, you need heavy-duty suspension links to keep the axle located, and the links themselves have to be spread apart so they’re not concentrating all the towing forces in too small of an area (which hurts towing stability and overstresses components when the tail is trying to wag the dog.) Compactness, one of the advantages of coil spring suspensions, can be a hindrance in setting up for towing. So you wind up with relatively long radius arms to help locate the axle, and big sway bars and often additional load-distributing/leveling links to make the whole thing work. A lot more weight, bushings, attachment points and frame reinforcements to make it all work. More weight, more cost. Or more expensive materials if you’re trying to save weight — so even more cost. And the whole assembly may take up more room in between and under the frame rails.
Take a look at the classic original Range Rover/Discovery real coil spring suspension. The vehicles are no slouch for trailer capacity in their size and weight class (nowhere near a large American pickup…). But the rear suspension alone takes up virtually every inch of space from the middle of the frame to the rear bumper with just enough room to tuck the fuel tank in. Everywhere else you look you’ll find attachments and bushings for the various suspension members, the spring plates and pockets, and the remaining space has to be kept clear for the driveshaft and threading the exhaust through. Leaf springs would take up far less room, but wouldn’t have the articulation and ride controllability, especially for an off-road vehicle.
I’m curious: when did U.S. domestic cars start using coil springs? I’m guessing they first appeared on European vehicles and then migrated across the pond?
BTW I love how the topshot caption seems very out of place. As in, Huibert doesn’t strike me as the kinda guy who says things like “Boing Boing.”
Coil springs started coming in on front suspensions in the late 40’s. By the 50’s, it was pretty much across the board. The new directions in styling meant a solid front axle just wouldn’t work anymore. Engines needed to drop lower and front wheels needed to move further rearward. It all lead to the end of solid front axles and with it front leaf springs.
This was a great read! Thanks for the in-depth lesson on suspension. I now have a greater appreciation for the rear leaf suspension on my Volvo V60 wagon.
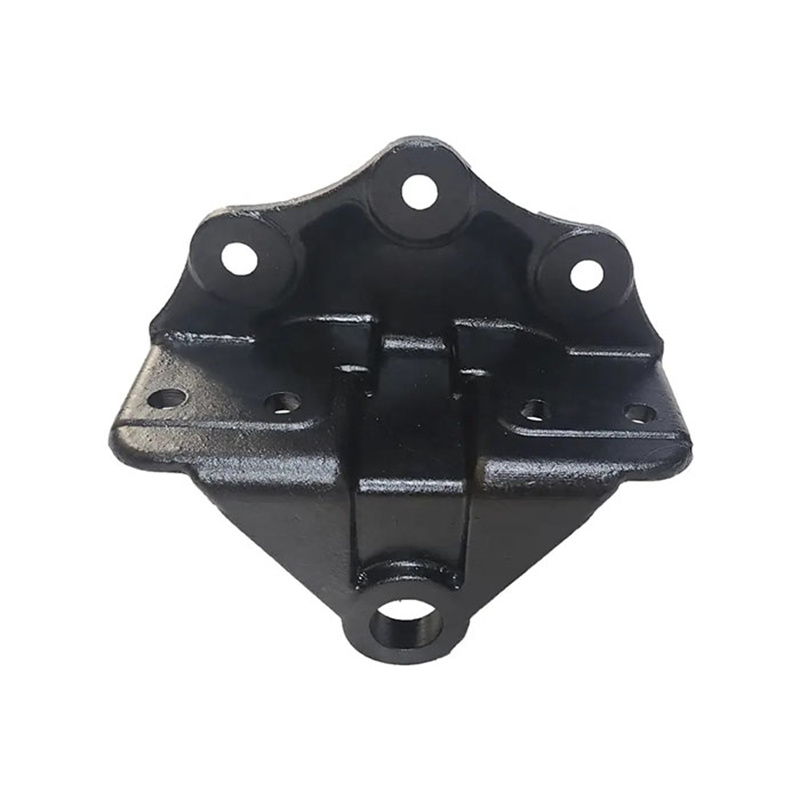
Suspension U Bolts © 2024 The Autopian. All Rights Reserved. Design by Jazel.