A Practical Guide to PPAs
CEO Point of View: AI Predictions 2024 100kw Diesel Generator
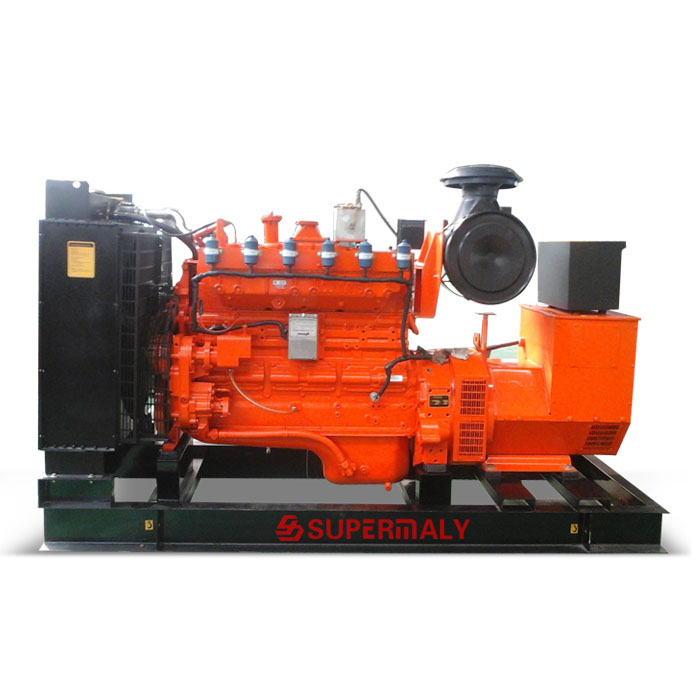
Reducing greenhouse gas emissions and costs.
The oil and gas industry is facing increasing demands to clarify the implications of the energy transition, regarding operations and business models. In addition, the industry faces pressure to outline how it can reduce greenhouse gas emissions and meet the goals of the Paris Agreement.
Oil and gas operators' use of renewable sources to electrify their platforms could play a key role in reducing their carbon footprint over the coming decades, and to reduce energy-related emissions in line with international climate targets.
Sia Partners analyzed how power is supplied to offshore platforms, and how different technologies can contribute to a more eco-friendly industry, aiming for Net-0, while remaining cost-effective.
There are ample, cost-effective opportunities to reduce the intensity of emissions by minimizing flaring of associated gas and venting of CO2, tackling methane emissions, and integrating renewables and low-carbon electricity into new upstream and liquefied natural gas (LNG) developments. As of today, 15% of global energy-related GHG emissions come from the process of extracting oil and gas and delivering it to consumers.
One of the challenges facing oil and gas production is finding a suitable, sustainable and cost-effective source of energy to supply the platforms, in particular, offshore platforms, which are more challenging due to their location.
Sia Partners assessed the specificities of powering an offshore platform. An uninterrupted power supply is essential, as many pieces of equipment of the platform need to be powered (see below).
In addition to this, Sia Partners took a deeper look at how power is supplied to these platforms, and analyzed current and prospective supply methods. Sia Partners looked into five different methods, in particular: what each method entails, and whether it can achieve Net-0 while being cost-efficient.
Diesel generators stationed at sea require additional features and configurations to those on land. Generators used on oil platforms must be made with materials and coatings that can withstand the extreme temperatures, water, salinity and wind present at sea. They are also designed to not require frequent maintenance and overhaul, as it can be difficult for a maintenance crew to go offshore and provide these services.
Typically, these offshore drilling rigs diesel engines use 20 to 30 m3 diesel fuel per day, depending on the operations.
Offshore oil and gas sites are located in isolated and locations with harsh weather conditions. In order to meet the power needs of an oil platform, while optimizing costs, it is interesting to equip it with reliable generator sets adapted to the oil and gas installations. Having a spare emergency diesel generator might be useful. It is a reliable, self-propelled machine capable of providing a source of emergency power. Autonomy is certainly one of the main advantages of a generator.
On the other hand, the big drawback of diesel combustion is the emissions released into the atmosphere, not only greenhouse gasses, but other air pollutants (sulfur dioxide, nitrogen oxides, and airborne particles such as soot, etc.). Moreover, the combined release of carbon dioxide (CO2) and nitrous oxide (N2O) intensifies the greenhouse effect. It is the worst case scenario in terms of emissions. One diesel generator of 1100 kVA will emit around 318 tons of CO2 per year (fuel emissions and cleaning).
In terms of costs, one must take into account the cost of the generator, its installation, the purchase and storage costs of diesel fuel, as well as the maintenance of the generator.
This brings us to a total estimated cost of around $2,500,000 for the acquisition of 1 generator, and one year of diesel and O&M for this generator. One platform can have 10 generators onboard to cover its needs, which brings us to $25,000,000 for the acquisition of the generators and 1 year of use for the platform.
From installation to maintenance to consumption, a generator requires regular monitoring. This comes into account when looking at the effort deployed to maintain it.
Lastly, the diesel needs to be acquired, in a historical context of strong volatility, and stocked, on a platform where space is scarce.
Gasses associated with oil production (known as "off-gasses") or gas extraction, can be recovered to avoid release into the atmosphere, and used to power gas generators. This solution is particularly well suited to the needs of the oil and gas sector in producing emergency energy and guaranteeing a continuous supply.
For example at Kaombo, a TotalEnergies innovative ultra-deep-water offshore project in Angola, the so-called “fuel gas” which comes from the wells, is compressed and then partly used as fuel gas for the gas turbine generators, and partly exported onshore (Angola LNG) to be transformed into electricity.
The internal combustion engine is a good option for a small gas flow. Many natural gas-compatible engine designs, ranging from a few tens of KW to a few MW, are available on the market. An engine can even use the associated gas from one or more oil wells and produce electricity for operating purposes and for injection into the electrical grid.
One advantage is that the rig can use an otherwise unused gas, avoiding flaring it and to wasting an energy source.
Despite this positive point, with few exceptions, the engines available are designed to run on clean natural gas, i.e., nearly pure methane. The direct use of associated gas, which contains inert gasses and heavier hydrocarbons (butane, propane), poses stability problems. It is thus necessary either to restrict the engine (by using a lean mixture) or to pass by a rudimentary treatment of the natural gas. The use of the locally produced associated gas is therefore more polluting than pure gas, and negatively impacts the emissions issue.
Compared to diesel generators, however, the cost impacts are beneficial, because the platform is no longer required buy and store diesel for the generator and, instead, uses locally produced resources. To estimate this gain in terms of costs, we can base ourselves on the same hypothesis as for the diesel generators:
This brings us to a total estimated cost of around $18,000 and $53,000 for the acquisition of one gas turbine generator and its operations and maintenance for 1 year. One platform can have 10 generators onboard to cover its needs, which brings us to around $180,000 to $530,000. This amounts to around $24,500,000 of savings per year for one platform, notably thanks to the gas supplied on site.
While diesel-powered generators, followed by gas generators, are the most common ways to power offshore operations, they are not the only methods available. Technology is ever-changing and as technology advances, new methods are being developed to more efficiently power offshore rigs.
After analyzing the existing fossil-based power supply of offshore platforms, Sia Partners analyzed alternative methods, as well as their impacts in terms of greenhouse gas emissions and costs.
Offshore oil and gas rigs can be connected to the onshore electric network via subsea cables. Currents will be transmitted via submarine cables to offshore facilities, often tens of kilometers from the coast.
Norway, with its significant North Sea oil reserves, is a pioneer in offshore power solutions and has been utilizing subsea cables in the Utsira High region, sometimes 200 km from shore.
Many offshore platforms are heading for this type of electrification thanks to several drivers:
Indeed, compared to generators, electrical power from shore will prevent NOx emissions and a large part of CO2 emissions, depending on how the electricity from the local network is produced. In Norway and the European Union, for example, we observe that the annual reduction of CO2 emissions from the platform will attain 120,000 to 1,533,000 Tons of CO2. This does depend on the distance from shore (50 to 300 km), on the power requirement (100 MW to 250 MW), and the location of the platform. Regardless of these criteria, CO2 emissions will always be lower when using the grid connection than generators.
The use of submarine electrical cables also reduces life cycle operating costs compared to traditional gas turbines. Given the specificities of each project (nature, application, regulatory framework), the level of investment depends on the assigned power (MW) and cable length (km). For a given distance, investment choices between gas turbines, for example, and subsea High Voltage Direct Current links, are largely dictated by power requirements.
The greater the power requirements, the more economical the HVDC solution is, because it only requires an increase in the transmission capacity of the HVDC link (up to 1,000 MW) to cover these needs. If turbines are used, the number of turbines will have to be increased, which causes operating and maintenance costs to soar, which are very low with the HVDC solution. Submarine power cables greatly reduce life cycle operating costs compared to generators.
If we take Norway, and a reference region (e.g. European Union), where GHG emissions or energy efficiency regulations are less stringent, but where the price of electricity is higher than in Norway, we come to the following conclusions:
Fuel and offshore personnel costs for operation and maintenance are the two main operating expenses of the life-cycle. Then there are eco-taxes (Norway) or CO2 emission quotas (EU). The reduction in operating costs is significant with submarine links. The same is true for the GHG emissions of the platforms. Subsea cables also require less effort to maintain, and this method increases space on the rig where a generator would normally reside, reduces the weight of the platform and makes the work environment safer and healthier.
However, despite those many advantages, this method also comes with some constraints:
The examples clearly show that supplying power to offshore platforms via submarine cables is both an economical and environmentally friendly solution that also enhances operational safety. While each project must be analyzed individually, the scenarios are sufficiently compelling to consider this solution for both new projects and existing installations. High-voltage direct current technology has proven its benefits and is expected to be used by an increasing number of platforms in the years to come.
Offshore Oil & Gas platforms can be electrified with renewable energy powered by either fixed-bottom offshore wind turbines or floating wind turbines. Again, Norway is leading the way with the world’s largest floating wind farm, which recently generated its first power. The Hywind Tampen will have a total capacity of 60 MW and will provide approximately 35% of the electricity demand of the Gullfaks and Snorre oil and gas fields.
Just like with subsea cables, removing power generation from oil rigs increases space on the rig, reduces the weight of the platform and makes for a healthier and safer work environment. Using floating platforms also opens up the possibility to place more platforms and wind farms to increase the amount of as-needed power.
A major part of Greenhouse gas emissions on Oil & Gas platforms comes from the use of gas turbines. Indeed, in the UK Continental Shelf (UKCS), studies have found that around 70% of the GHG emissions from offshore oil and gas facilities comes from the gas turbine generators located on platforms. Therefore, since wind turbines generate carbon-free electricity, the impact of using wind turbines, rather than gas turbines, to generate electricity on Oil and Gas platforms has a major impact on GHG emissions. In addition, electrical power from wind turbines will prevent NOx emissions.
In 2021, the cost of wind turbines was about 1,3 M USD per MegaWatt. In the United States, the average estimated levelled cost of energy for commercial-scale offshore wind projects is around $84 per MWh. The trend is to produce larger turbines to decrease per-megawatt project costs. The average offshore wind generator capacity deployed in 2021 was 7.4 MW. The ongoing technological developments to produce larger capacity wind generators, will help maintain and reduce the costs of wind turbine electrification of the platforms. Moreover, installation of offshore wind turbines requires skills and resources similar to the installation of an oil platform, which means that oil platform builders are also able to install, connect and maintain offshore windmills, thus reducing costs.
However, despite considerable benefits, there are constraints such as the intermittency of energy. Indeed, in case of low wind, no electricity is produced. Nevertheless, this risk can be mitigated by installing floating turbines in deep water, far away from coasts where winds are stronger and more frequent. On the other hand, in case of strong winds, wind turbines have to be stopped to prevent damage. Consequently, the use of wind turbines has to be supported and completed by storage capacity to mitigate periods of low-production.
Where the sun can energize photovoltaic panels for a handful of hours a day and the wind can blow turbines for days on end, but, equally, disappear for extended periods without warning, the tide and waves are nearly constant. This unending movement of waves, currents and tides can be used to produce clean, renewable electricity.
To produce wave and tidal energy, different types of technologies exist, for example: buoys (structures moving up and down with the motion of the waves), or oscillating water columns (processing the “in” and “out” motion of the water entering the columns). Once electricity has been produced by wave or tidal energy devices, it can be transported through an underwater cable or stored in special batteries.
This electrification technology has a much lower level of maturity than those analyzed before.
The question has been raised and is being studied to power offshore oil & gas platforms, but today none make a real use of this technology, even though case studies deliver “promising results”.
Hypothetically, every kWh of power generated by waves or tides saves around 1,000 g of CO2 compared to the same power generated by diesel, in addition to reductions in emission of all other types of greenhouse gas such as methane (CH4) and nitrous oxide (N2O). Wave and tide energy has one of the lowest carbon footprints of all energy types. On a life-cycle basis, tidal energy emits less than 22 gCO2.
Regarding costs, there is limited data from which to draw concrete figures. Examining existing tidal or wave energy projects can help provide financial guidance regarding upfront and maintenance costs. In general, generating electricity from tidal and waves costs 2 to 9 times higher than the peak average price for wind energy. Indeed, wave turbines must be more durable than wind turbines in order to withstand ocean currents. According to an estimate by the US Department of Energy, tidal energy costs $130 - 280 per megawatt-hour (MWh), while wind energy can cost as little as $20 per MWh.
Today, costs of wave and tidal power are generally very high because they are in the research phase and generally paid for by government or research grants. There are no energy companies utilizing wave energy at scale, something which would bring the costs down. Maintenance for these plants is projected to be expensive because they are submerged in constantly-moving saltwater. Also, wave energy plants will most likely need regular (and costly) maintenance.
In addition to high costs, one of the biggest cons of wave and tidal energy projects is that no utility currently has the ability to install wave farms because they are not yet large enough to provide a significant amount of electricity. While some wave energy systems have been tested in Scotland, Hawaii, and more recently Australia, their power generation capacity is only about 2.5MW at their peak. The industry is expected to grow, but it remains challenging to implement wave energy generators at a usable scale.
Finally, precautions must be taken to avoid undesirable effects on the environment. For example, these devices may alter ocean currents, disrupting the natural patterns of food and larvae. Also, if the turbines produce noise, it can disorientate marine animals, causing them to collide with devices or nearby land. Early research has shown that fish and marine mammals can avoid hitting the devices, but sometimes they do not. It is important for scientists to continue to research how local plants and animals respond to these devices.
This method is still very prospective, and not concretely applicable today, but is an interesting avenue to explore in the future.
Companies will need to consider all options as they work to meet their carbon reduction goals and offset the environmental impact of diesel generators.
Having analyzed the pros and cons of each electrification technology for oil and gas offshore platforms, Sia Partners concludes that the least emitting electrification methods, which are technologically feasible, are:
These two methods will also enable stakeholders to:
Partner, Energy, Utilities & Environment | Paris
Sia Partners integrates this data in its client database to send you marketing communications (invitations to events, newsletters and new commercial offers). This data will be kept for 3 years before being deleted and you can withdraw your consent to the processing of your data at any time. To learn more about the management of your personal data and to exercise your rights, please consult our Data Protection Policy.
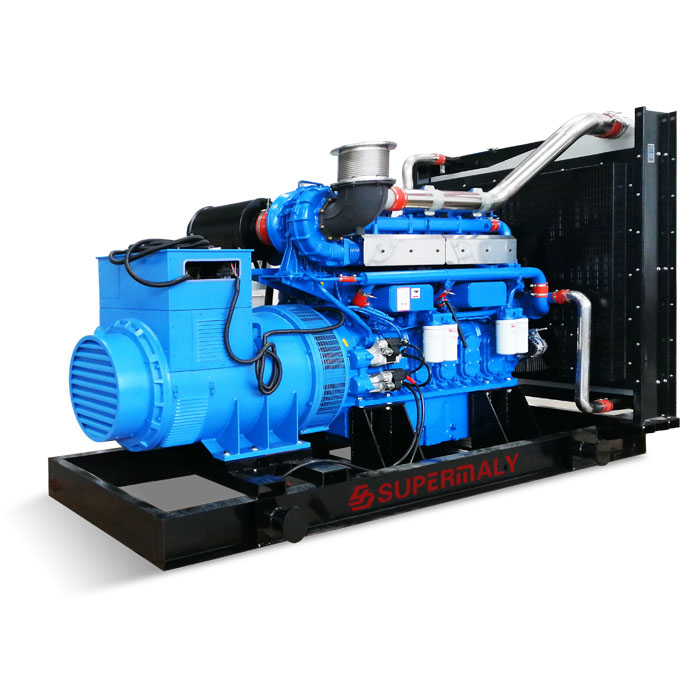
125 Kva Gas Generator Your data are used by Sia Partners to process your contact request. Please note that you have rights regarding your personal data. For more information, we invite you to read our data protection policy