Precision punching technology is not new, but it might be unfamiliar to a new generation entering the metal fabrication industry—at least until they discover how many things can be done on one of these machines. Sergeyryzhov/iStock/Getty Images Plus
Metal fabricating might be a small portion of the overall U.S. manufacturing sector, but it still employs more than 1.45 million people at more than 60,000 private companies. Those numbers are slowly returning to pre-pandemic levels, which means a new generation of workers is replacing the baby boomers, who are embarking on their retirement journeys. Train Parts
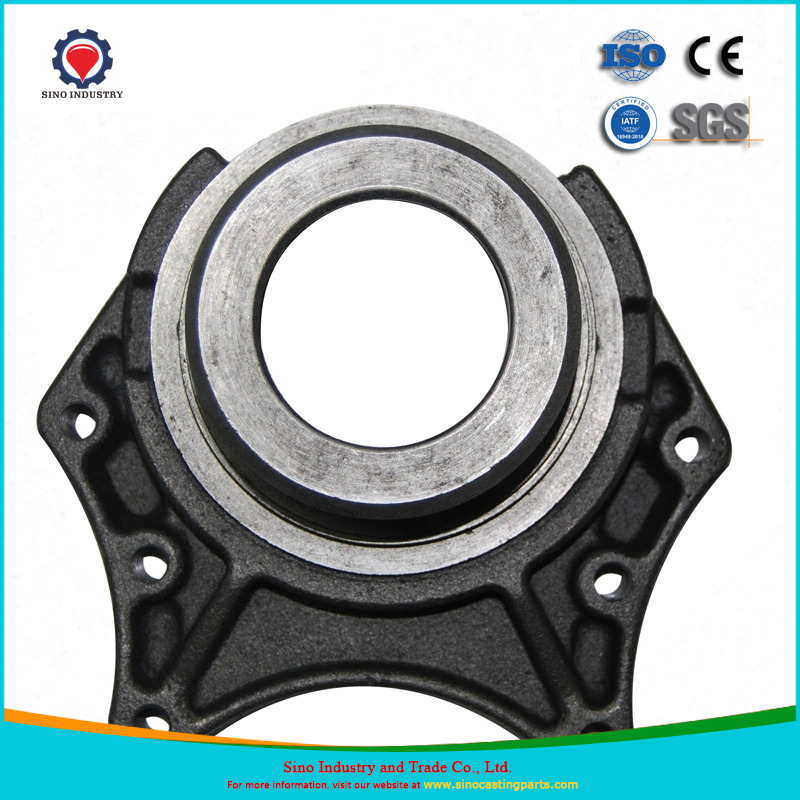
With that changeover comes a fresh set of eyes. Those new to metal fabricating might not have the depth of blanking, bending, and welding knowledge of those that they replace, but they do bring a fresh perspective that often results in a very challenging question: “Why do we do it like that?”
No matter how long you’ve been in the business, that question forces even metal fabricating veterans to consider possible alternatives. In the spirit of continuous improvement, everything deserves to be looked at with a critical eye.
That’s the perspective many are taking with precision punching machines. The metal fabricating workhorse that was the dominant CNC machine in shops for the tail end of the 20th century can still be found in shops because the technology has something to offer. At one time, it was unparalleled as a holemaking machine, but today’s high-powered fiber laser cutting machines are challenging that title. But these machines still stand alone when it comes to not only punching out blanks of different sizes, but also creating forms. No secondary processes are required.
Jeff Tyl, North American fabrication and aftermarket sales manager, Murata Machinery USA Inc., recently went to visit a job shop after crossing paths with someone from the company at a trade show. The trade show attendee was looking at turning equipment and noticed the Muratec punching machine at work. He really had no idea what such a machine could do.
Tyl said that on the follow-up visit to the job shop, he began to understand why the booth visitor was so interested in the punching machine. The shop had a basic plasma cutting table in the back that provided blanks that often needed deburring before they went off to secondary operations.
“Right then, I told them you can common-line cut some of these parts on a turret punch, and you’re going to save money on the scrap. You also can use a pincher wheel, which creates a groove in the sheet, and you’re going to have easier breakouts,” he said. “Also with the turret punch, you are not going to have slag buildup like you get on the plasma, so no cleanup is needed.”
The job shop was receptive to the message, according to Tyl, because the person in charge of the plasma cutting operation was new to the job. He looked at the old process and thought that there had to be a better way. The punching machine is likely to be that tool to make it happen.
“If you think about it, a punch press itself is automation on its own,” Tyl said, referring to the machine’s ability to do so much. In many instances, with the use of the right tooling, parts can avoid secondary bending or processing and move directly to assembly, painting, welding, or shipping.
That message has been lost on the younger generation of metal fabricators that didn’t grow up in the early days of CNC punching technology. A punching machine can address multiple fabricating functions and deliver high tolerances (+/- 0.004 in. in some instances) and repeatability on forms that a human operator and a press brake would be hard-pressed to match.
FIGURE 1. Conventional turret punch presses have long had difficulty with downward extrusions. As the formed work is lifted off the upper surface of the die during sheet movement, modern tooling eliminates degradation of the form stemming from interference with the die.
For those that have only been in shops that had laser cutting machines dominating blanking chores, here are five examples of how punching can reduce the cost associated with producing a part.
Adding fasteners to sheet metal is not unique. Most shops typically have some sort of hardware insertion capabilities on the shop floor.
What if the workpiece didn’t have to be directed to the hardware insertion area for something like a weld nut? What if it could be handled during the blanking process?
Tyl said the ability to tap sheet metal is something that some operators in the fabricating industry don’t realize is possible. They see a hardware insertion machine on the shop floor and think that’s where the weld nut ought to be affixed to the workpiece.
That doesn’t have to be the case. A tapping tool can provide the threads necessary to avoid adding something like a weld nut. In cases where the sheet metal is not thick enough to provide the room for the tapped threads, the combination of an extrusion tool (see Figure 1) and the tapping tool can make it happen. The punch drives through the sheet metal, shears the surface, and forces the material to flow into the die opening. That creates enough surface area for the tapping tool to introduce five or six threads into the extruded hole, eliminating the need for a weld nut and the time and scheduling required to move a pallet full of workpieces to the hardware insertion machine.
“When compared to international counterparts, the U.S. [metal fabricating market] typically likes higher-strength material,” Tyl said. “When A36 or A1011 kind of material might work, a lot of people push to get that grade to A50 or higher.”
The ASTM A572 Grade 50 steel is a high-strength/low-alloy plate. It has a high strength-to-weight ratio and is resistant to corrosion. It’s also more expensive than other lighter-gauge alternatives.
If you could deliver the same strength characteristics in a lighter-gauge, more affordable material, would you want to explore that option? Well, that option is available with the use of something called a roller tool (see Figure 2).
The roller tool creates a form in the sheet metal by pinching the material between two ball bearings in the upper tool assembly and the single ball bearing in the lower assembly. Because the tool is in an auto index station within the turret, the tool can create forms, also called ribs, in any shape. The ribs can be started or ended anywhere on the sheet.
These contoured forms in the sheet metal provide extra strength in the material, allowing it to demonstrate greater resistance to deformation from external forces than normally would exist without the ribs. That’s why the forms are often seen in cabinets and office furniture, where lightweight materials are desired, but rigidity is expected.
FIGURE 2. A roller tool can be used to create ribs in contour using the auto index in the turret. These ribs offer sheet metal extra strength that normally wouldn’t be available.
“It really takes an engineer to understand that a punch press and the right tooling can offer up this type of capability,” Tyl explained.
Tyl recalled a job shop that wanted to know if it was possible to create tread plate made from a high-tensile-strength aluminum on a punching machine, thus avoiding the secondary forming operation on a press brake.
In this example, having input from the punching tool designers really helped, Tyl said. The application engineers at Mate Precision Technologies came up with an upforming tool that did the trick.
In this application, the outer perimeter of the workpiece is punched out. Then, an upform tool comes from the bottom tool, pushing up into the material almost 3/8 to ½ in. as the sheet is held in place. When done, the upforming tool retracts into the bottom die to keep from scratching the material and is repositioned for the next upform (see Figure 3).
“By taking their secondary processes offline and bringing the forming into the first stage of processing, they produced parts faster. Their time studies verified that,” Tyl said.
A well-placed slot in a part design can translate into a better design and product flow on the shop floor. The welder might have to step up, but the nature of today’s shop is all about contributing where one can.
In many instances, a part leaving the punching machine is either headed to the bending or welding department. With a punched slot in the right place, sometimes that part might be able to skip the press brake and go right to the welding department.
Tyl said that by removing the material in a potential bend line, a welder can manually make the bend himself. The full tonnage of a press brake driving a punch into the material isn’t necessary to make the form.
The slot also can act as a guide for where the subsequent weld needs to be placed. Welding wire filling that open space is going to create a much stronger bond than if the welder simply was welding the bend line exterior to the surface of another workpiece.
“How many times in a production setting have parts been taken to the weld station to realize that they were never press broken? Then you have to go back and fix it again,” Tyl said. “All of that takes time and money. If you’ve put that slot in there at the first stage of processing, you understand where it needs to go.”
FIGURE 3. Forming tools have been developed so that they are only raised during the forming operation. The application of the tool improves the form shape and also the quality of the worksheet with minimum scratches.
Whereas a punching machine can deliver highly accurate and reliably consistent parts, the same can’t be said for a press brake. The simple presence of a human operator introduces the likelihood of inconsistency in results. At a press brake, an operator might not present the part flush with the backgauge or could even have the blank turned upside down when beginning the bending sequence. Even the best operator gets sidetracked every now and then.
This is where a punching machine can help to error-proof the press brake operation, according to Tyl. While the part is being blanked on the punching machine, a scribing tool (see Figure 4) can place an R or an L on the part to designate the righthand or lefthand sides. A multitool capable of punching all 26 alphabet characters into the material surface can write words. Tyl added that some shops that service the medical field actually use such a multitool to produce full sentences on medical parts.
The punching machine might not be the star of the show at FABTECH and other metal fabricating trade shows, but it still occupies an important place in the shop. It might grow in importance as more young people enter the industry and discover what the old punch press has to offer.
“If you think about a turret punch, whether it’s tapping a hole, marking a part, cutting a profile, or making a form, all of that is automation,” Tyl said. “If you’re looking at doing more than one process, you might be able to automate the whole task simply because of this type of machine.”
Editor’s Note: John Ripka, an application technician with Mate Precision Technologies, www.mate.com, contributed to this article.
FIGURE 4. A scribing tool can be used for markings or etchings on the surface of the sheet metal. The punching machine programming system takes care of the desired marking instructions.
See More by Dan Davis
Dan Davis is editor-in-chief of The Fabricator, the industry's most widely circulated metal fabricating magazine, and its sister publications, The Tube & Pipe Journal and The Welder. He has been with the publications since April 2002.
Read more from this issue
Find The Fabricator on Facebook
Find The Fabricator on Twitter
The Fabricator is North America's leading magazine for the metal forming and fabricating industry. The magazine delivers the news, technical articles, and case histories that enable fabricators to do their jobs more efficiently. The Fabricator has served the industry since 1970.
Easily access valuable industry resources now with full access to the digital edition of The Fabricator.
Easily access valuable industry resources now with full access to the digital edition of The Welder.
Easily access valuable industry resources now with full access to the digital edition of The Tube and Pipe Journal.
Easily access valuable industry resources now with full access to the digital edition of The Fabricator en Español.
Omar Nashashibi, co-founder of The Franklin Partnership and a lobbyist representing manufacturing trade associations, joins The Fabricator Podcast...
© 2024 FMA Communications, Inc. All rights reserved.

Stamping Accessory Not yet registered? Sign up